Design and Manufacture the Full set of the Isostatic Pressing Molds/Bags
Isostatic polyurethane mold series products have the characteristics of long service life, high precision, small deformation and easy demoulding. They are widely used as ceramic isostatic molds, cemented carbide isostatic molds, rare earth permanent magnet material isostatic molds, graphite isostatic molds, etc. Isostatic pressing mold, etc.
Rubber products are more prone to oxidation, affecting accuracy and causing surface stickiness.
So, can molds made of polyurethane materials special for isostatic pressing solve these problems? The answer is yes. As a polymer material, polyurethane is specially formulated according to the requirements of the isostatic pressing industry. It has strong pressure resistance, oil resistance, fast rebound, and strong oxidation resistance. The hardness can also be adjusted according to needs to meet different processes. Therefore, isostatic pressing molds made of special polyurethane materials have high precision, long life, no deformation, and easy demoulding. They are replacing traditional isostatic pressing rubber molds and steel molds on different equipment.
Product Overview: Isostatic rubber molds are used for the molding of ceramic materials, tungsten and molybdenum materials, graphite materials, refractory materials, and alloy powders. They can be customized according to drawings or designed according to samples.
Product features: The deformation generated by the elastic mold when subjected to the pressure of the liquid medium is transmitted to the powder in the mold. The friction between the powder and the mold wall is small, the green body is evenly stressed, and the density distribution is uniform. The pre-pressed blank is encapsulated. In the elastic rubber mold, it is sealed and placed into a high-pressure cylinder, and the green body is pressed and formed through liquid transfer.
Product advantages: The mold cover is reasonably designed to ensure no leakage, and the blank is well formed and has a long service life. Including the fixtures used to process the blank, all can be customized! Steel molds are produced free of charge in certain quantities.
High rebound, fatigue resistance, low deformation rate, easy demoulding, used in dry bag and wet isostatic presses to press ceramic product blanks, graphite products, cemented carbide and other non-standard powder molding.
Accuracy: Materials formed by the isostatic pressing process are often used in important occasions or equipment, which require extremely high accuracy. If the mold precision is not enough, it will cause excessive post-processing and even lead to the scrapping of the product. Including the smoothness of the product surface, whether the mold will deform during the loading of powder materials, whether the compression rate in all directions is consistent after the mold receives pressure during the pressing process, etc. And whether the mold deforms and maintains its original accuracy after repeated use will also have an important impact on the molding quality of the product.
Ease of use: Whether the characteristics of the isostatic pressing mold can meet different pressing processes, and whether other auxiliary fixtures can be minimized during use. Whether it is easy to demould after use, whether the mold can rebound quickly, etc. will all have an impact on the operation.
Durability. The isostatic pressing mold works in a high-pressure environment and needs to be in contact with oil and other media. If the pressure resistance is not good, or it is not resistant to oil and chemicals, the performance will easily decline.
In view of these requirements for isostatic pressing molding, can the isostatic pressing rubber molds and steel molds used on traditional equipment meet these requirements? What are their disadvantages?
When steel molds are used to make products of many shapes, especially special-shaped parts, it will be difficult to demould. If the mold is cut open, seams will be formed on the surface of the product, which will affect the quality of the product, increase post-processing and increase costs.
The surface of the rubber isostatic pressing mold is not smooth enough, resulting in a rough surface of the finished product and increasing the workload of post-processing. At the same time, it will also cause a waste of materials. And these materials are often very expensive.
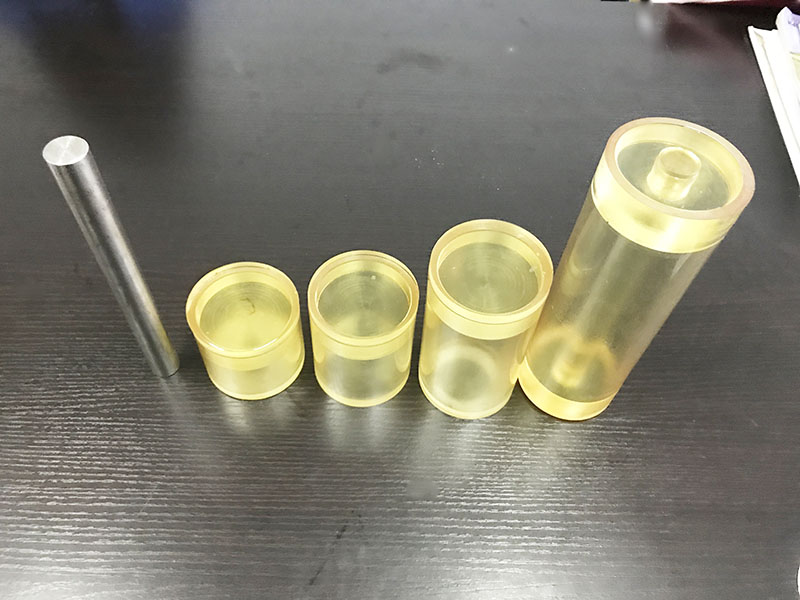

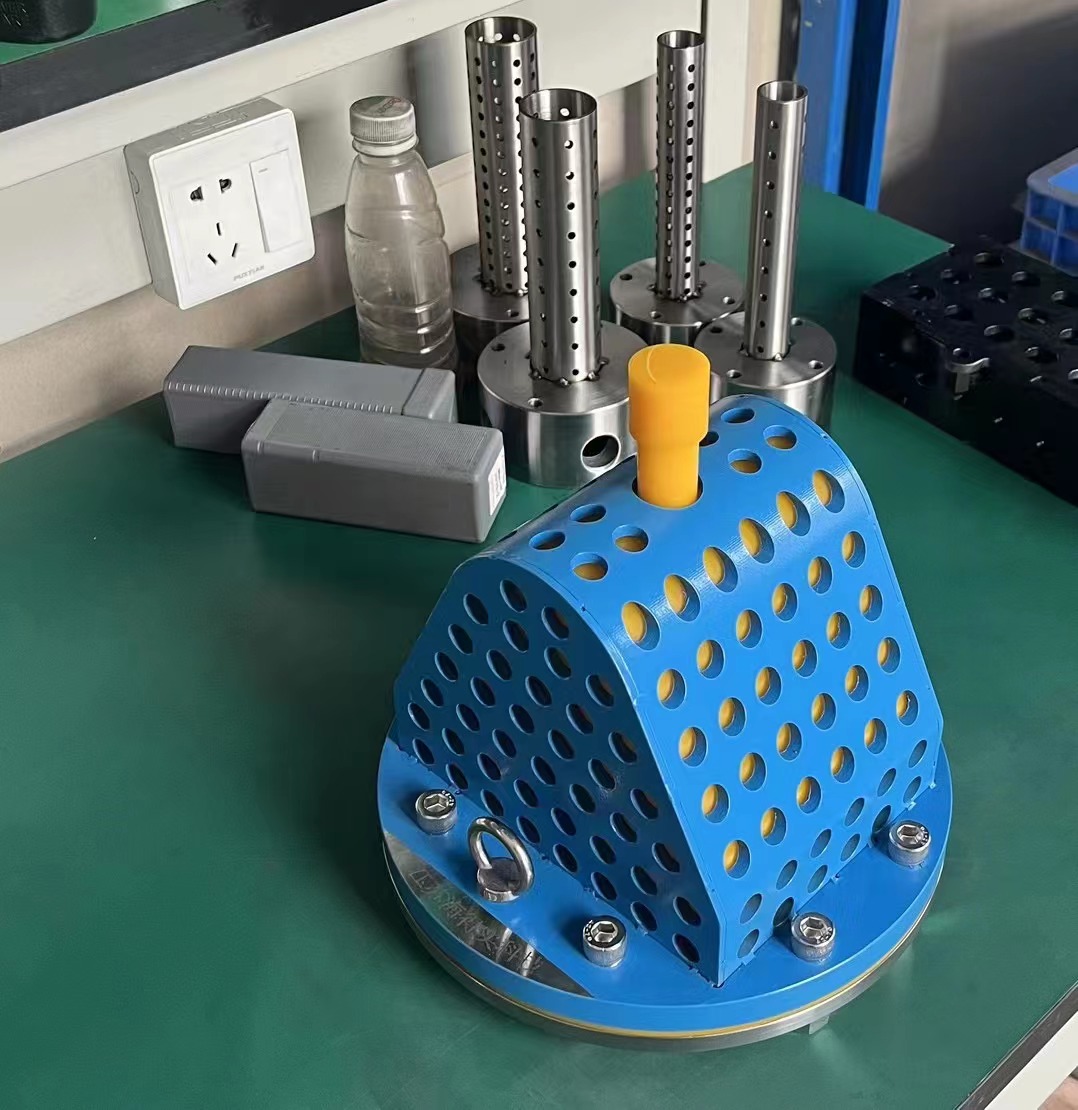

We support all kinds of customization, if you need it, please contact us.
Phone/whatsapp:+86 18234744811
Email:sales@highindustryco.com
Rubber mold Plastic mold Polyurethane Product Pu product