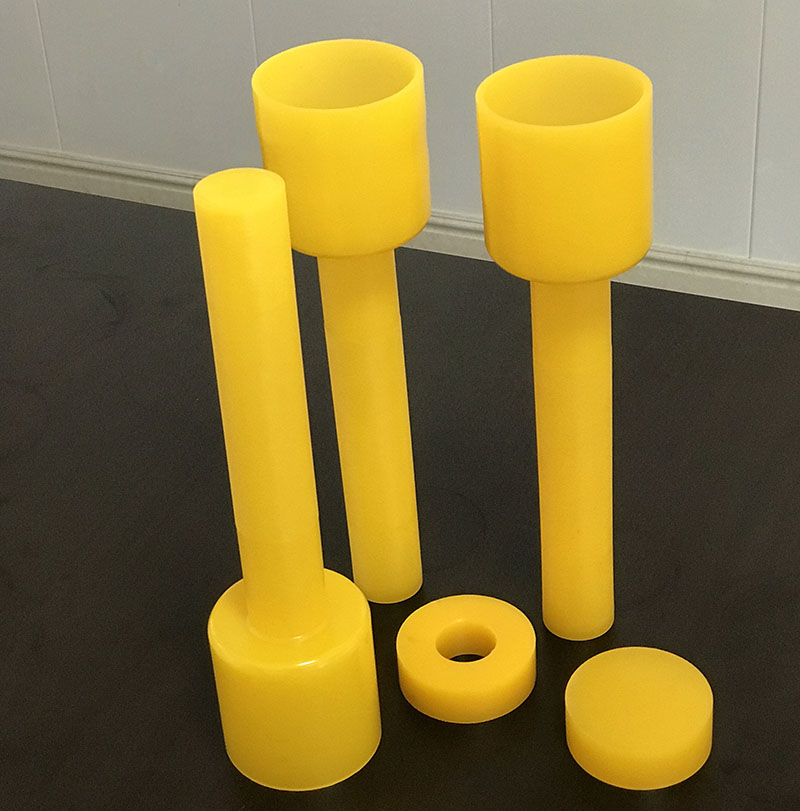
The Steps of Producting isostatic Pressing Molds/Bags
Categories: Wet bag CIP mold
Application: The Steps of Producting isostatic Pressing Molds/Bags
InquiryMain description:
The Steps of Producting isostatic Pressing Molds/Bags
The Steps of Producting isostatic Pressing Molds/Bags
The Steps of Producting isostatic Pressing Molds/Bags
The design and production of isostatic pressing molds require extensive experience. The design method of isostatic pressing molds needs to comprehensively consider multiple factors such as pressure, temperature, and time to ensure that the mold can achieve the ideal molding effect. The following are the steps for designing an isostatic pressing mold:
Determine mold size and shape: Determine the internal and external dimensions and shape of the mold according to product requirements.
Select materials: According to the application scenario and pressure requirements, select appropriate materials for the mold body and sealing ring.
Design the mold structure: According to the size and shape of the mold, design a reasonable structure to improve the molding effect and production efficiency.
Determine pressure parameters: Determine appropriate pressure and holding time based on product requirements and material properties.
Consider temperature factors: Temperature has a great impact on material performance and molding effects, so appropriate temperature control solutions need to be considered when designing the mold.
Optimize the sealing structure: The sealing performance of the isostatic mold is directly related to the molding effect and production efficiency, so a reasonable sealing structure needs to be designed to achieve good sealing performance.
Determine the cooling method: In order to ensure production efficiency and product quality, it is necessary to consider appropriate cooling methods when designing the mold to quickly cool the mold.
We support all kinds of customization, if you need it, please contact us.
Phone/whatsapp:+86 18234744811
Email:sales@highindustryco.com