Isostatic Pressing Molds for Ceramics and more Powders Molding
Isostatic press is a technology that realizes isostatic pressing at room temperature. It usually uses rubber or plastic as the covering mold material and liquid or elastomer as the pressure medium. Cold isostatic pressing is mainly used for the shaping and pressing of powder materials to provide preformed blanks for further sintering, forging or hot isostatic pressing processes.
The foundation of isostatic pressing technology is that the fluid medium transmits pressure equally and simultaneously in all directions. The key to isostatic pressing technology is to establish a leak-proof interface between the pressed material and the pressure medium.
Ceramic powders are all powders that have been batched and wet-milled, and then spray-dried and granulated before they can be formed on an isostatic press. However, when forming special refractory materials such as intrusion nozzles, integral plug rods, and integral tap holes for steelmaking, ingredients with low moisture or low binder (liquid) can be used for molding. High-temperature hot isostatic pressing technology simultaneously completes powder pressing and sintering processes under high-temperature and high-pressure conditions. It can produce fine grains close to the theoretical density and complex powder parts with uniform properties. Hot isostatic presses have become special equipment for producing 1% precision products in aviation, aerospace systems, metallurgy, industrial ceramics, various superhard material tools, abrasives, composite materials and other industries.
Used for tungsten, molybdenum, beryllium, titanium and other powder products, the grains are refined uniformly, without segregation, and can reach the theoretical density; hot isostatic pressing of high-temperature alloys, high-temperature ceramics, and high-alloy castings can eliminate internal stress, Internal defects such as pores, cracks, shrinkage cavities, and segregation can be improved to improve fatigue and fracture resistance. It is ideal for producing high-quality, high-end, new products such as aero-engine blades, aerospace rocket ablation-resistant throat liners, and spacecraft high-temperature fairings. equipment. Its working principle is to put the workpiece into the heating furnace, introduce high-pressure gas through the gas compressor, and heat the workpiece through the heating furnace. According to Pascal's law, the high-pressure gas will act on all surfaces of the workpiece evenly. Under the simultaneous action, the workpiece shrinks evenly and is sintered into finished products.
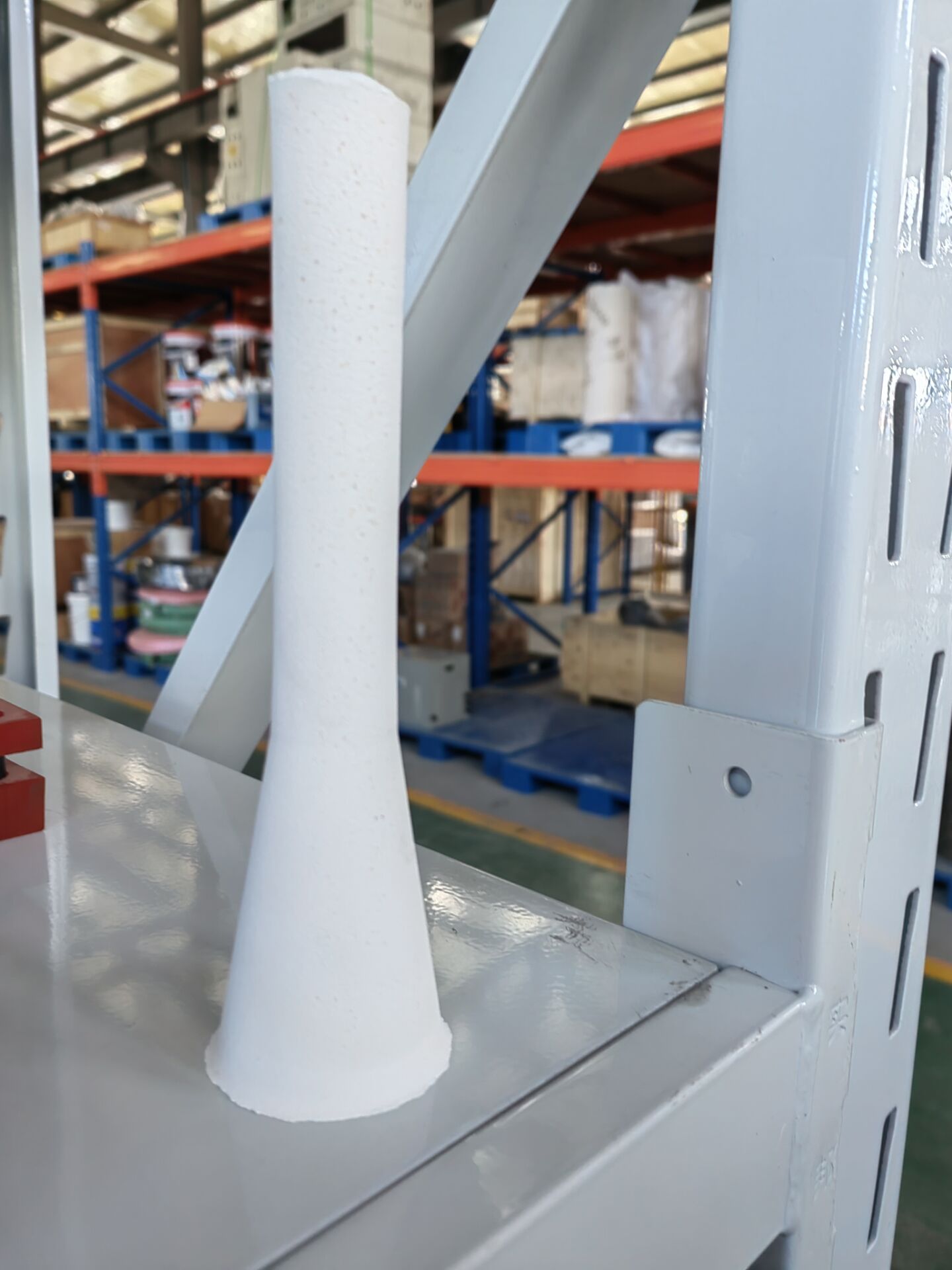
Jiangsu High Industry on the research and development and production of high-performance polyurethane isostatic pressing molds. Through in-depth cooperation with many isostatic pressing equipment manufacturers and in-depth study of the industry, the developed isostatic pressing polyurethane mold series products have the characteristics of long service life, high precision, small deformation, easy demoulding, etc., and are widely used in ceramics, etc. Static pressing mould, cemented carbide isostatic pressing mould, rare earth permanent magnet material isostatic pressing mould, graphite isostatic pressing mould, etc.
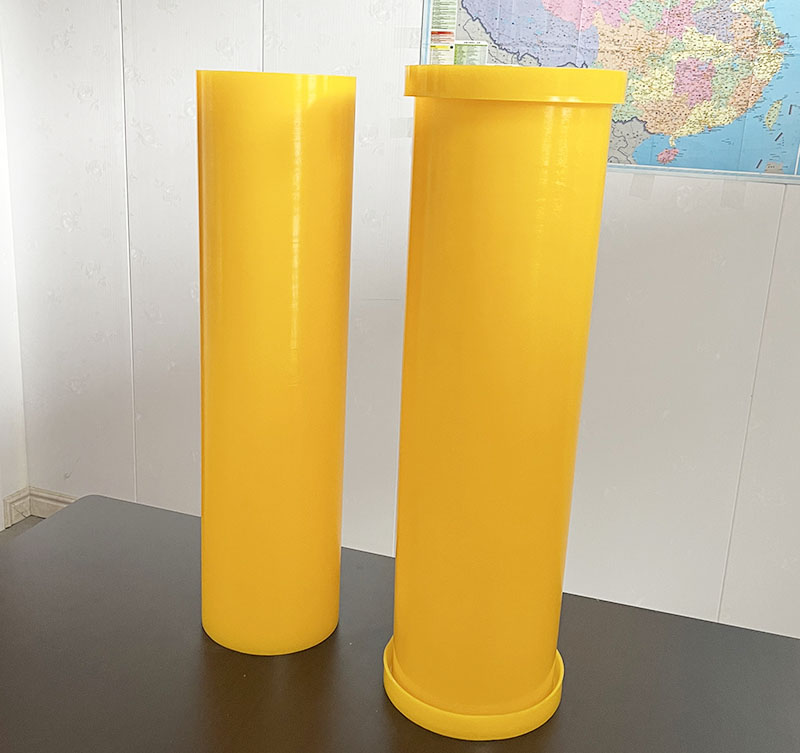
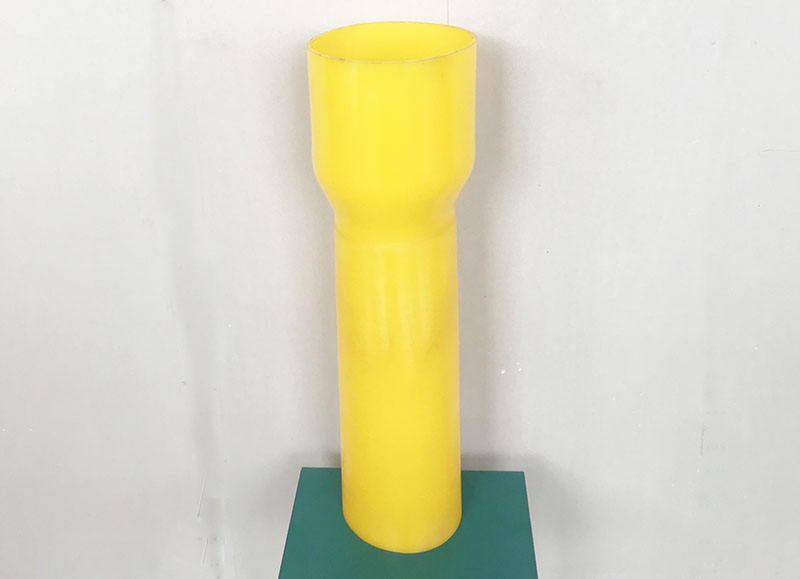
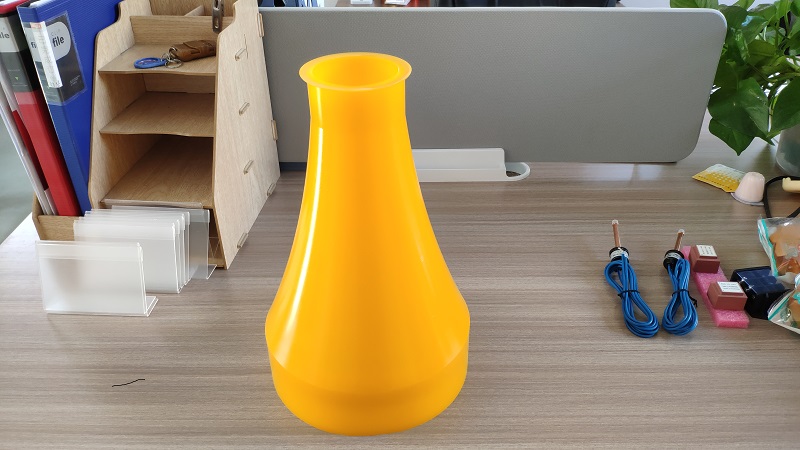
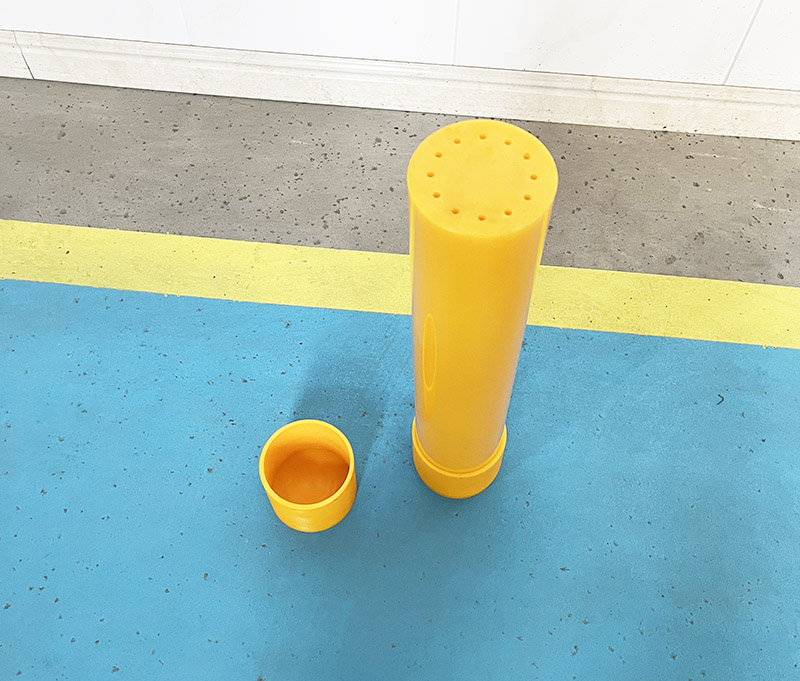
We support all kinds of customization, if you need it, please contact us.
Phone/whatsapp:+86 18234744811
Email:sales@highindustryco.com
Rubber mold Plastic mold Polyurethane Product Pu product