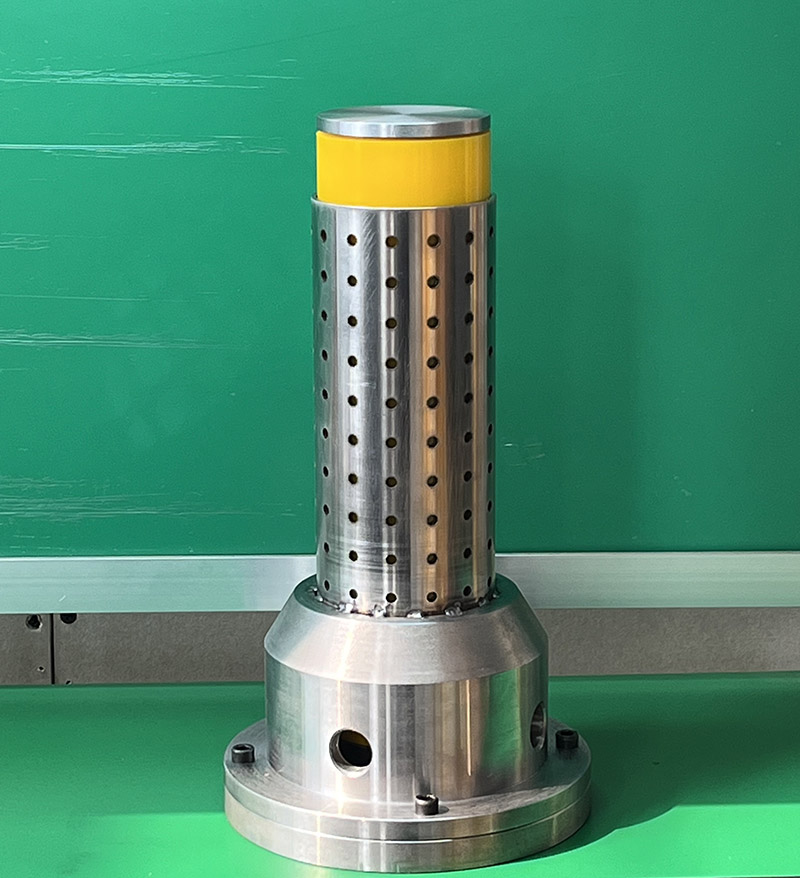
Polyurethane CIP Molds for Powder Metallurgy
Categories: DIP powder forming mold
Application: Polyurethane CIP Molds for Powder Metallurgy
InquiryMain description:
Polyurethane CIP Molds for Powder Metallurgy
Polyurethane CIP Molds for Powder Metallurgy
Polyurethane CIP Molds for Powder Metallurgy
Powder metallurgy is a forming and manufacturing technology consisting of three main processing stages. First, the main material is physical powder, divided into many small particles. Next, the powder is injected into or through the mold to create a weakly bonded structure (via cold welding) that is very close to the size of the object to be made. Typically pressures of 10-50 tons per square inch are used. In addition, in order to obtain the same compression ratio on more complex workpieces, it is usually necessary to use a lower punch and an upper punch. The ends are formed by applying pressure, high temperatures, long solidification times during which self-welding occurs, or any combination thereof. The two main technologies used to form and consolidate powders are sintering and metal injection molding. It became possible to develop rapid manufacturing techniques for producing products using metal powders. Because with this technology, the powder is melted rather than sintered, better mechanical strength is achieved. Powder metallurgy and ceramic sintering technology are closely related. Sintering involves producing hard, solid metal or ceramic sheets from starting powders. There is evidence that iron (iron) powder was melted into hard objects as early as 1200 BC. In these early manufacturing operations, iron was extracted by hand from the metal sponge after reduction and then reintroduced as a powder for melting or sintering.
A wider range of products can be obtained with powder processes than with direct alloying of molten materials. In melting operations, "phase rules" apply to all pure and combined elements and strictly define the distribution of liquid and solid phases that may exist for a given component. Additionally, alloying requires bulk melting of the raw materials, thereby creating undesirable chemical, thermal, and sealing limitations on manufacturing. Unfortunately, the handling of aluminum/iron powder poses significant problems. Other substances that are particularly reactive to atmospheric oxygen, such as tin, are sinterable in the atmosphere or in temporary coatings.
Powder consolidation
A part or article is produced by shaping a large quantity of powder and then consolidating it to form a metallurgical bond between the particles. This is achieved by a high-temperature diffusion process called sintering, sometimes assisted by external pressure. Although a small amount of liquid may be present during the sintering process, the material does not melt. Sintering can be thought of as welding particles into their original useful shape.
Cold isostatic pressing
Isostatic powder pressing is a mass-saving molding process. Fine metal particles are placed into a flexible mold, and then high-pressure gas or fluid is applied to the mold. The resulting article is then sintered in a furnace. This increases the strength of the part by binding metal particles. This manufacturing process produces very little scrap metal that can be used to create many different shapes. The metal powder is contained in an enclosure, such as a rubber membrane or a metal can, and is subjected to isostatic pressure, that is, an external pressure that is uniform in all directions. Since the pressure is isostatic, the pressed parts have a uniform density. Irregularly shaped powder particles must be used to provide adequate green strength in pressed parts. It is then sintered in a suitable atmosphere to obtain the desired product.
Jiangsu High Industry on the research and development and production of high-performance polyurethane isostatic pressing molds. Through in-depth cooperation with many isostatic pressing equipment manufacturers and in-depth study of the industry, the developed isostatic pressing polyurethane mold series products have the characteristics of long service life, high precision, small deformation, easy demoulding, etc., and are widely used in ceramics, etc. Static pressing mould, cemented carbide isostatic pressing mould, rare earth permanent magnet material isostatic pressing mould, graphite isostatic pressing mould, etc.
We support all kinds of customization, if you need it, please contact us.
Phone/whatsapp:+86 18234744811
Email:sales@highindustryco.com