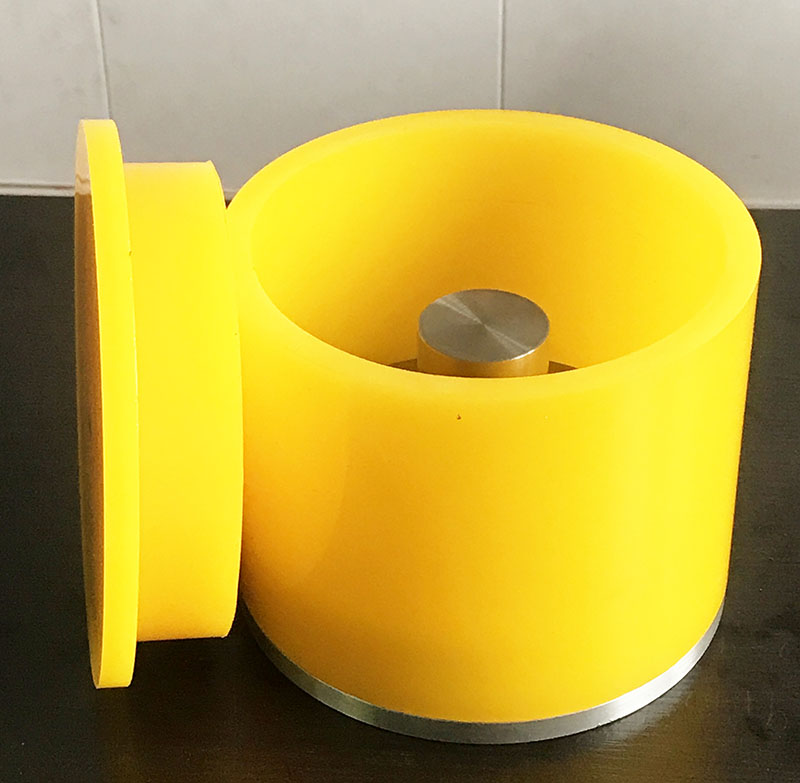
Isostatic Pressing for Metal Molding
Categories: DIP mold-dry bag isostatic press
Application: Isostatic Pressing for Metal Molding
InquiryMain description:
Isostatic Pressing for Metal Molding
Isostatic Pressing for Metal Molding
Isostatic Pressing for Metal Molding
Isostatic pressing is an advanced metal processing technology that uses the simultaneous application of pressure and temperature to convert metal powder into parts with high density and precise shape. This technology is
It is widely used in various industrial fields and plays an important role in improving production efficiency and product quality.
The basic principle of isostatic pressing is to load metal powder into a mold and apply pressure in a high-pressure environment. At the same time, by heating the mold, the metal powder has certain plasticity at a certain temperature. Under the combined action of pressure and temperature, the metal powder particles deform and fit together to form a dense part. Finally, through a cooling and solidification process, the result is a part with high density and precise shape.
Isostatic pressing technology has many advantages. First, because metal powders are so consistent and controllable, they can produce high-precision parts. Compared with traditional metal processing, isostatic pressing can reduce or eliminate subsequent processing steps and greatly improve production efficiency. In addition, this technology can also realize complex-shaped parts in one forming, reducing the time and material costs required for processing. Since there is no liquid metal in the isostatic forming process, there are no quality issues such as surface oxidation or contamination.
In practical applications, isostatic pressing is widely used in industries such as automotive, aerospace, electronics, and medical. For example, in automobile manufacturing, isostatic pressing enables the manufacture of engine parts, chassis components and cooling systems. In the aerospace field, this technology can make
Manufacture high-strength aerospace structural parts and engine components. In the fields of electronics and medical devices, isostatic pressing can produce high-precision, complex connectors and conductive parts.
To achieve high-quality isostatically pressed parts, the selection of process parameters is crucial. First, the appropriate pressure and temperature need to be determined based on specific material properties and part requirements. Pressure that is too low can result in parts that lack density, while pressure that is too high can cause parts to deform or crack. Temperatures that are too low may not allow the metal powder to achieve sufficient plasticity, while temperatures that are too high may cause excessive evaporation or the inability to eliminate gases.
In addition, mold design and lubricant selection also have an important impact on the quality and effect of isostatic forming. The mold should have a reasonable structure and appropriate wall thickness to ensure the consistency and stability of the part shape. Lubricant selection should take into account the impact on materials and the requirements of the production environment to reduce friction and wear.
In summary, isostatic pressing, as an advanced metal processing technology, is of great significance in improving production efficiency and product quality. In practical applications, reasonable selection of process parameters, design and optimization of mold structure, and selection of appropriate lubricants can all improve the effect of isostatic pressing. It is believed that with the continuous advancement of science and technology, isostatic pressing technology will play a greater role in more fields and bring more innovation and development to our industrial manufacturing.
Isostatic pressing molds for metal molding
We support all kinds of customization, if you need it, please contact us.
Phone/whatsapp:+86 18234744811
Email:sales@highindustryco.com