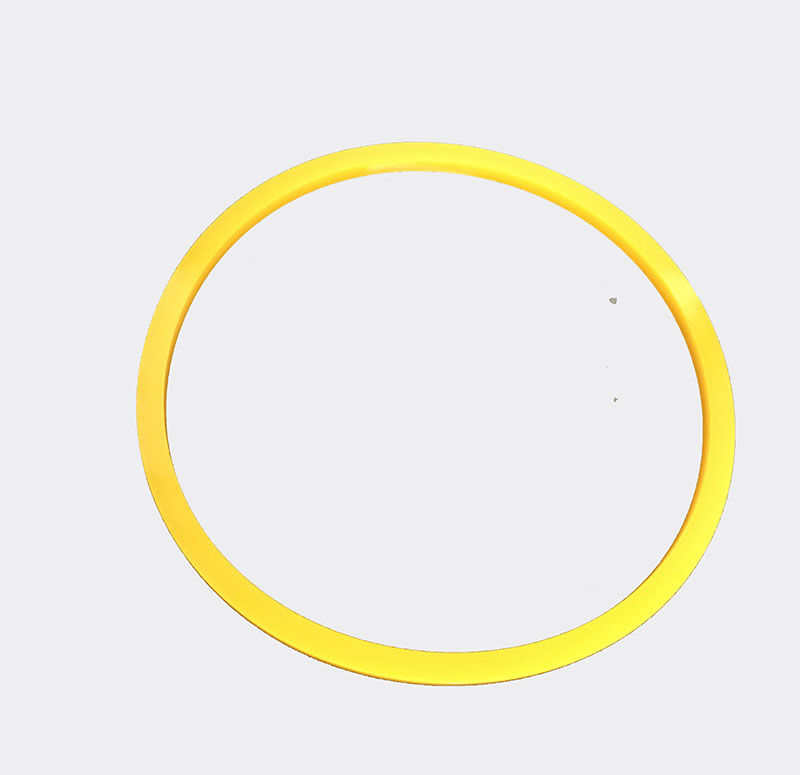
Cold Isostatic Pressing Mold for the Zirconia
Categories: Powder metallurgy bag mold
Application: Cold Isostatic Pressing Mold for the Zirconia
InquiryMain description:
Cold Isostatic Pressing Mold for the Zirconia
Cold Isostatic Pressing Mold for the Zirconia
Cold Isostatic Pressing Mold for the Zirconia
Zirconia is a very important structural and functional material. It has excellent physical and chemical properties. Its development, research and application have attracted great attention from all over the world. The preparation of uniformly dispersed nano-scale ZrO2 powder has naturally become This is an important thing, and it is also the key to ensuring its special performance.
Zirconia precision ceramic cold isostatic pressing (Cold Isostatic Pressing, CIP) directly acts on the powder or briquette in the elastic mold sleeve through the high-pressure pump to apply the static pressure generated by the fluid or gas, so that it is subjected to uniform pressure in all directions. suppress. The isostatic pressing of zirconia precision ceramics is divided into cold isostatic pressing and hot isostatic pressing according to its characteristics. Isostatic pressing technology can be used to manufacture new alloy products that are difficult to produce by casting technology. The products have uniform density and no residual stress. It has the advantages of no mold wall friction, no additives and binders, etc., and is usually used to manufacture high-density large and special-shaped parts.
Compared with steel mold pressing, isostatic pressing of zirconia precision ceramics has the following advantages:
①It can press parts with concave, hollow, slender parts and other complex shapes;
②The friction loss is small and the forming pressure is low;
③The pressure is transmitted from all sides, the density of the compact is evenly distributed, and the strength of the compact is high;
④The mold cost is low. The disadvantages of isostatic pressing are: the size and shape of the green compact are not easy to accurately control, the productivity is low, and it is not easy to implement automation. The latter disadvantage can be overcome to some extent by the dry bag isostatic method.
This method is called "dry bag" because the operator is not in contact with the liquid medium. The production rate of a single machine has reached 500-3800 pieces/hour. Dry bag isostatic pressing is generally suitable for the production of ceramic balls, tubes, filters, grinding wheels, spark villages, etc. The pressing pressure of ceramics is generally 70-200MPa. Usually just natural rubber, chlorine, rubber, polyurethane, polyvinyl chloride, etc. are used as molds.
CIP Molds/Bags
We support all kinds of customization, if you need it, please contact us.
Phone/whatsapp:+86 18234744811
Email:sales@highindustryco.com