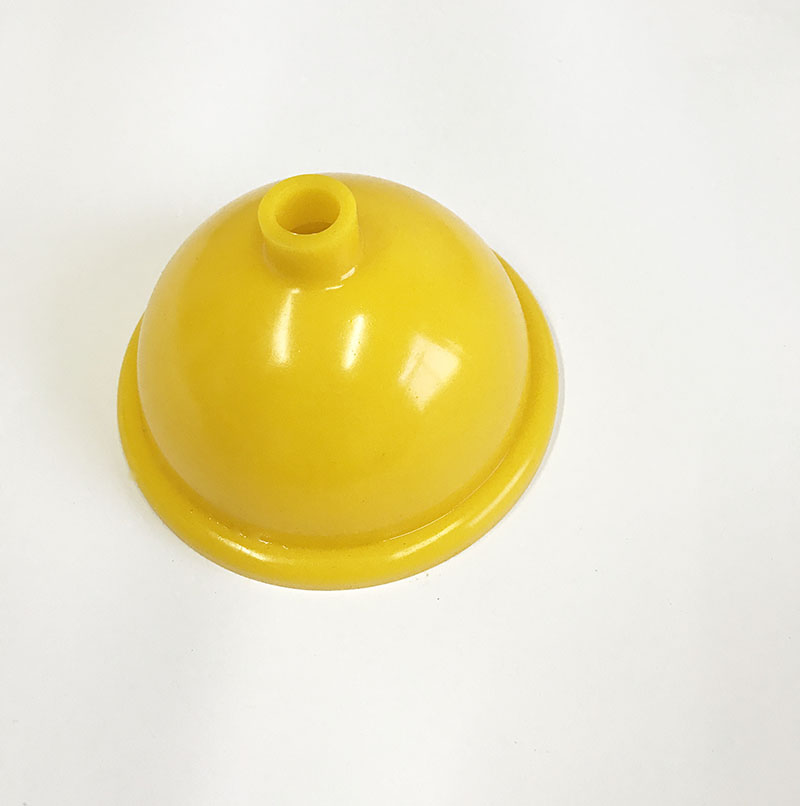
The Molding Process of Zirconia Ceramic
Categories: CIP powder forming bag mold
Application: The Molding Process of Zirconia Ceramic
InquiryMain description:
The Molding Process of Zirconia Ceramic
The Molding Process of Zirconia Ceramic
The Molding Process of Zirconia Ceramic
Zirconia ceramic molding is to mold zirconia ceramic powder into a molded body with a certain geometric shape. There are currently two methods for forming zirconia ceramic powders, namely dry forming and wet forming.
Representatives of dry forming processes are "isostatic pressing" and "compression molding".
Advantages of dry molding process: the process is relatively simple, suitable for industrial mass production; disadvantages: the light transmittance of the formed zirconia is low, and the performance is unstable.
The representative of the wet forming process is "slip casting".
The advantages of the wet forming process: the produced zirconia ceramic block has good light transmission after sintering, and the overall mechanical properties are high; the disadvantage: the entire production process is complicated and not suitable for industrial mass production.
(1) Compression molding
Compression molding is to pour zirconia powder into a precision steel mold and rely on external pressure to achieve molding.
The method is simple to operate, has high production efficiency, and is suitable for large-scale industrial production. However, the production of thick green bodies by compression molding is poor, the mold wears a lot, and the cost is high. Due to the uneven distribution of pressure in the radial and axial directions, the formed body often has defects such as delamination and cracks.
(2) Isostatic pressing
Isostatic pressing is to obtain a molded body by applying pressure through a liquid medium.
Because the liquid has the advantage of isotropy, the zirconia molded body after isostatic pressing has uniform density, high density and good appearance. The surface of the isostatic pressing molding is smooth, and there will be no defects such as drop corners or cracks. However, the isostatic pressing molding is carried out in a high-pressure container, which consumes a lot of energy and equipment maintenance costs are high. Due to the above characteristics, isostatic pressing is still the most important forming method in industrial production.
(3) Grouting molding
Grouting molding is to inject zirconia slurry with certain fluidity into a porous plaster mold, and discharge the water in the slurry through the plaster mold, and the shape of the inner surface of the plaster mold is the shape of the molded body.
The size of the pores of the plaster mold is very critical. If the pores are too large, the drainage will be too fast, and the molded body will easily crack. If the pores are too small, the drainage will be too slow, which will easily cause the strength of the molded body to be too low. Therefore, it is necessary to choose a plaster mold with moderate pores.
A Samples of Isostatic Pressing Molds
We support all kinds of customization, if you need it, please contact us.
Phone/whatsapp:+86 18234744811
Email:sales@highindustryco.com