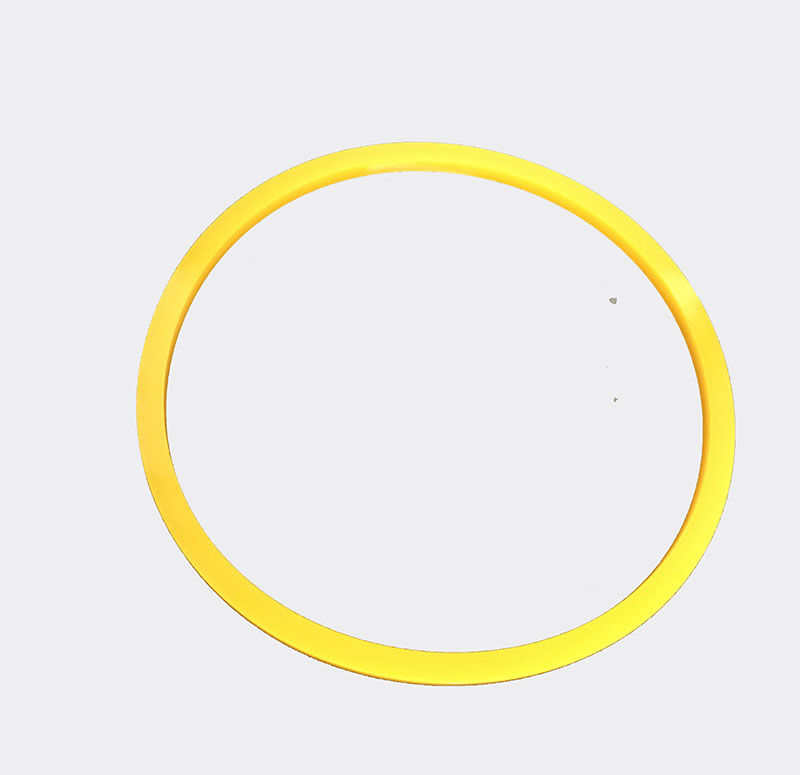
Isostatic Pressing Process and Characteristics
Categories: Cold isostatic pressing mold
Application: Isostatic Pressing Process and Characteristics
InquiryMain description:
Isostatic Pressing Process and Characteristics
Isostatic Pressing Process and Characteristics
Isostatic Pressing Process and Characteristics
The so-called isostatic pressing usually refers to cold isostatic pressing, which can be divided into two types according to the different forming processes, wet bag type and dry bag type.
Wet bag isostatic pressing technology is to put granulated ceramic powder or preformed body into a deformable rubber sheath, and then apply uniform pressure in all directions through the liquid. Remove the rubber sheath from the container. This is a discontinuous molding method. The advantages of this technology are relatively low cost, great flexibility in molding products of different shapes, and the pressure can reach 500 MPa. This technology can be used in the laboratory and in a certain scale of production, and it can form parts of medium complexity. Its disadvantage is that the number of molded products in a certain period of time is small.
Dry bag isostatic pressing molding technology is to fill batches of ceramic powder into flexible preforming molds, and then apply isostatic pressing. Since the mold is fixed in the equipment, when the pressing is completed, the shaped product is ejected. The "dry bag" type has a short molding cycle and a long service life of the mold, which is especially convenient for large-scale continuous industrial production. The mold materials used are polyurethane synthetic rubber or silicone rubber. Compared with wet bag isostatic pressing, the pressure of dry bag isostatic pressing is lower, generally within 200MPa. For isostatic pressing, the pressing time is usually only 1~2s.
Compared with steel mold pressing, isostatic pressing has the following advantages: ①It can form parts with concave, hollow, slender parts and other complex shapes; ②The friction loss is small and the forming pressure is large; ③The pressure is transmitted from all sides, Uniform distribution of green compact density, high crushing strength: ④ Low mold cost. The disadvantages of wet isostatic pressing are: the crushed size and shape are not easy to accurately control, the production efficiency is low, and it is not easy to implement automation. These shortcomings can be overcome to a certain extent by using dry bag isostatic pressing method.
Because cold isostatic pressing technology can improve product performance, improve product quality, and increase economic benefits, it has many compelling advantages compared with other molding processes. Therefore, the application field continues to expand and the technology is becoming more and more mature. So far, there are hundreds of types of products using isostatic pressing technology.
We support all kinds of customization, if you need it, please contact us.
Phone/whatsapp:+86 18234744811
Email:sales@highindustryco.com