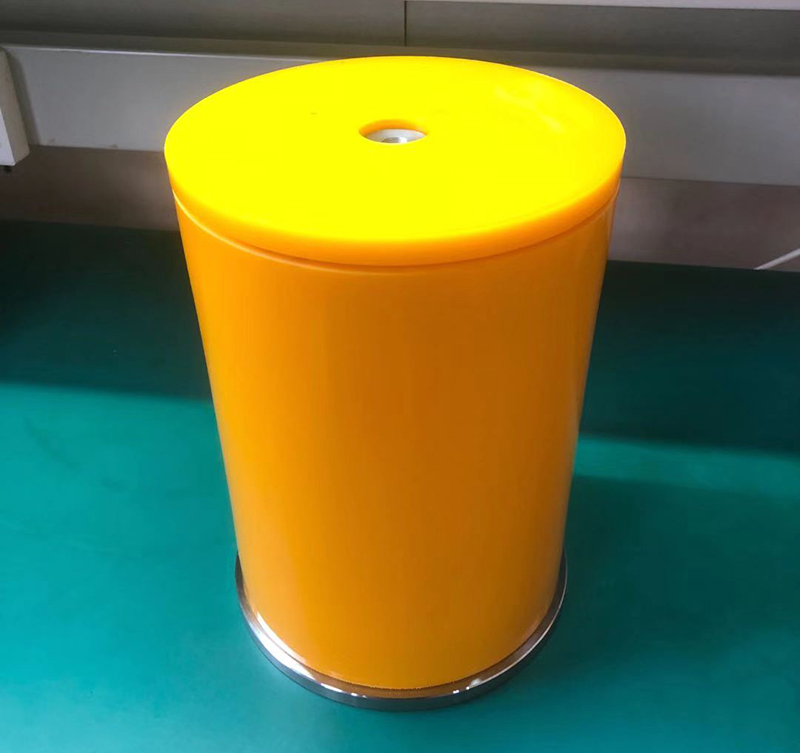
Isostatic Pressing Molds for Ceramic Products
Categories: Polyurethane CIP bag mold
Application: Isostatic Pressing Molds for Ceramic Products
InquiryMain description:
Isostatic Pressing Molds for Ceramic Products
Isostatic Pressing Molds for Ceramic Products
Isostatic Pressing Molds for Ceramic Products
The isostatic pressing of ceramic products completely abandons the plastic molding method of ceramic mud, does not need to consume plaster molds, has a high degree of automation, accurate shape and size of the green body, smooth surface, high density, good mechanical strength and high product quality. After the body is formed, it can directly enter the trimming process, etc., thereby simplifying the production process of daily-use ceramic products and reducing the production site and heat source consumption.
The isostatic pressing of ceramic products is the scientific application of Pascal's law in the forming method of ceramic products. The static mold is the concave surface of the forming plate and dish ceramic products, and it is cast a layer of wear-resistant plastic film on the convex static mold base; A wear-resistant plastic soft film similar in shape to discs and dish ceramic products is installed on the concave surface of the machine, and the wear-resistant plastic soft film is fixed and sealed on the movable mold. As a result, when the dynamic and static molds are pressed together, the cavity forms a space that is about twice as large as the volume of the daily-use ceramic body of the plate and dish. After applying an appropriate mold clamping pressure, the ceramic powder quickly fills up the space. Cavity and close the filling port, and finally feed high-pressure oil into the oil inlet of the movable mold. The high-pressure oil will force the wear-resistant plastic soft film to move towards the static mold and squeeze the ceramic powder. Therefore, the ceramic powder will It will be pressed into a uniform and dense disc and dish ceramic green body, which is the isostatic pressing molding process of disc and dish ceramic products.
It can be seen that the isostatic pressing molding process of disc and dish ceramic products is essentially that under the action of a suitable isostatic pressing molding system, the particles of each component of the ceramic powder move closer to each other to deform, etc., forcing the pores to The process of reducing the rate and densifying the structure of the ceramic body.
Jiangsu High Industry focuses on the research and production of isostatic pressing moulds, customizes various dry bag and cold isostatic pressing moulds, adapts to different models of various manufacturers at home and abroad, and deeply understands the needs of various industries. Alloy, graphite and other industries provide high-performance isostatic pressing mold rubber sleeves.
Product overview: Isostatic pressing rubber mold is used for the molding of ceramic materials, tungsten and molybdenum materials, graphite materials, refractory materials, and alloy powders. It can be customized according to drawings, and can be designed according to samples.
Product features: The deformation of the elastic mold under the pressure of the liquid medium is transmitted to the powder in the mold. The friction between the powder and the mold wall is small, the blank is uniformly stressed, and the density distribution is uniform, and the pre-pressed blank is encapsulated. In the elastic rubber mold, it is put into the high-pressure cylinder after sealing, and the green body is compressed and formed by liquid transfer.
Product advantages: The design of the mold cover is reasonable to ensure no water leakage, the blank is well formed, and the service life is long, including the fixture for processing the blank, which can be customized! There is a free amount of open steel molds.
We support all kinds of customization, if you need it, please contact us.
Phone/whatsapp:+86 18234744811
Email:sales@highindustryco.com