The Ceramic Molding Methods -- Dry pressing and Isostatic pressing
Generally speaking, the production process of ceramics can be divided into three stages: powder making → molding → firing. Today we will discuss the powder molding process. The raw material of ceramic products is loose powder material. The process of powder molding is to make the loose powder raw material or its aggregates into a green body or product with a certain size and strength through external force. In the molding process of ceramics, ceramic powder raw materials need to undergo certain processing before they can be made into blanks suitable for specific molding methods. According to the flow and rheological characteristics of the blank, ceramic molding methods can be divided into three categories: compression molding, plastic molding, and slurry molding.
The compression molding method, also known as the stamping process, is to add a small amount of binder to the powder (the water content must be controlled at 4%-7%, or even up to 1%-4%) for granulation, and then make it The granulated powder is placed in a mold (dry pressing is usually a steel mold, cold isostatic pressing is a rubber film), and pressurized on a pressure machine to form a green body of a certain shape. The characteristics of the compression molding method are that the binder content is low, it can be directly roasted without drying, and the shrinkage rate of the green body is small. high level of mechanization. Dry pressing and isostatic pressing are widely used in the pressing forming method. The principle, process and characteristics of each are introduced respectively, and the advantages and disadvantages of the two forming methods are compared.
1. Dry pressing
Dry pressing is to press the powder blank in the mold based on relatively high pressure. The essence is that the particles are close to each other in the mold under the action of external force, and the particles are firmly connected and kept in a certain shape by means of internal friction. craft. The technological process includes feeding, press molding, demoulding, blanking, and cleaning the mold.
1. Feeding: Fill the powder particles into the mold frame. In order to ensure the specification and quality of the green body, the feeding should be uniform and quantitative.
2. Pressure forming: use the relative movement between the molds to apply pressure to the loose powder, so that the powder is compacted into a dense green body. This process is a key process in press molding, and factors such as the magnitude of the applied pressure, pressing time and pressing method need to be controlled, and any change in conditions may lead to changes in the quality of the green body.
3. Demoulding: eject the formed body from the cavity of the mold.
4. Blank discharge: move the ejected and formed blank to the blank placing table or conveyor belt.
5. Clean the mold: if necessary, spray oil on the inner wall of the mold cavity to lubricate.
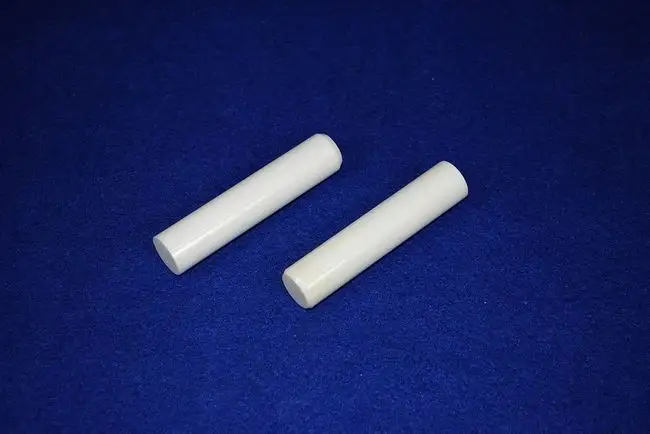
2. Isostatic pressing
The isostatic pressing method, also known as hydrostatic pressing, is a molding method that utilizes the incompressibility of liquid media and the uniform transmission of pressure. That is to say, the pressure on the sample in the high-pressure container is the same as that in the still water at the same depth, so it is called hydrostatic pressure or static pressure, and the forming process obtained according to this principle is called hydrostatic pressure. molding or isostatic pressing. Generally, the isostatic pressing of ceramic materials can be divided into wet bag isostatic pressing and dry bag isostatic pressing.
Compared with the dry pressing method, the biggest feature of the isostatic pressing method is that the powder material is in a state of three-dimensional compressive stress, so the performance and quality of the formed parts are significantly improved.
The advantages of isostatic pressing are specifically shown in the following points:
1. Dry pressing has only one or two pressure surfaces, while isostatic pressing is multi-axial pressure, that is, multi-directional pressure and multi-surface pressure, which is conducive to compacting the powder to a considerable density. At the same time, the linear displacement of the powder particles is small, and the friction work consumed in the movement of the powder particles is relatively small, which improves the pressing efficiency.
2. Compared with other compression moldings with approximately the same pressure strength, isostatic pressing can obtain higher green density, and it is uniform and dense in all directions, and does not have a large change due to different shape thickness.
3. Due to the little difference in the pressure direction of isostatic pressing, the friction between the powder particles and between the particles and the model is significantly reduced, so the phenomenon of stress in the green body rarely occurs.
4. The green body formed by isostatic pressing has high strength, the internal structure of the green body is uniform, and there is no particle orientation arrangement.
5. The moisture content of the powder used in isostatic pressing is very low (generally 1%-3%), and there is no need or little use of binders and lubricants. This is beneficial for reducing drying shrinkage and firing shrinkage.
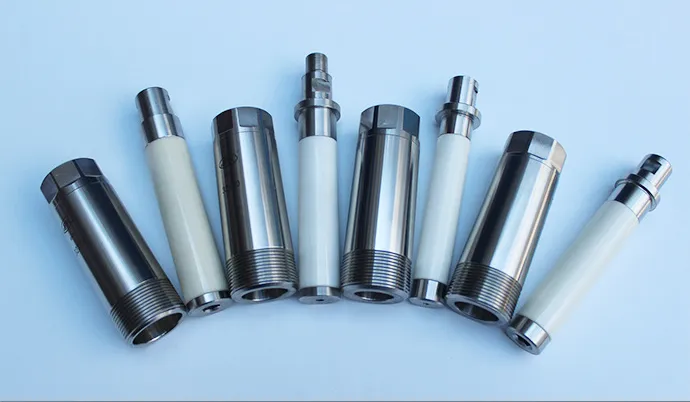
Isostatic pressing molds
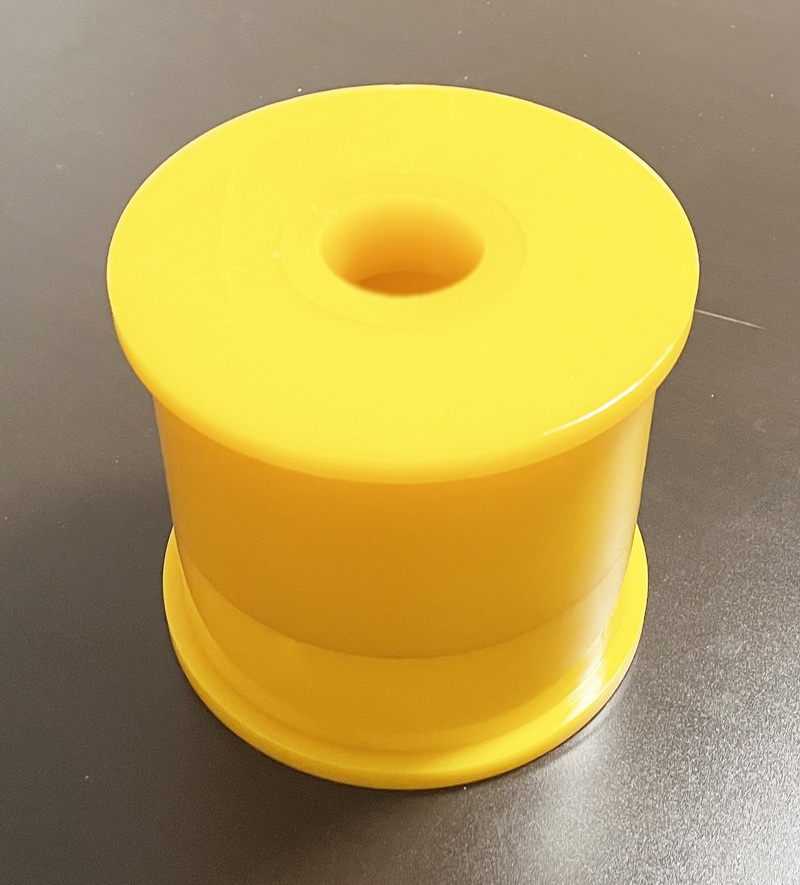
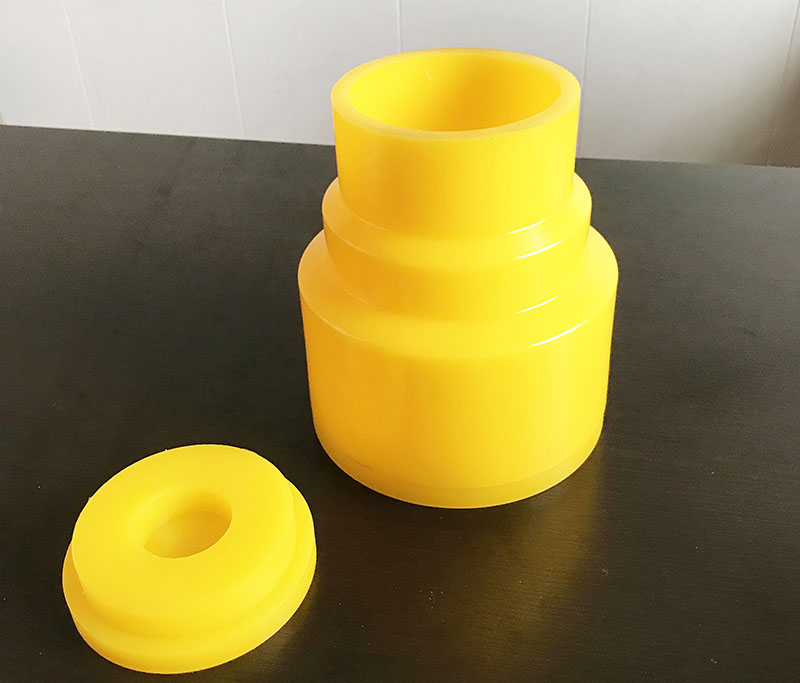
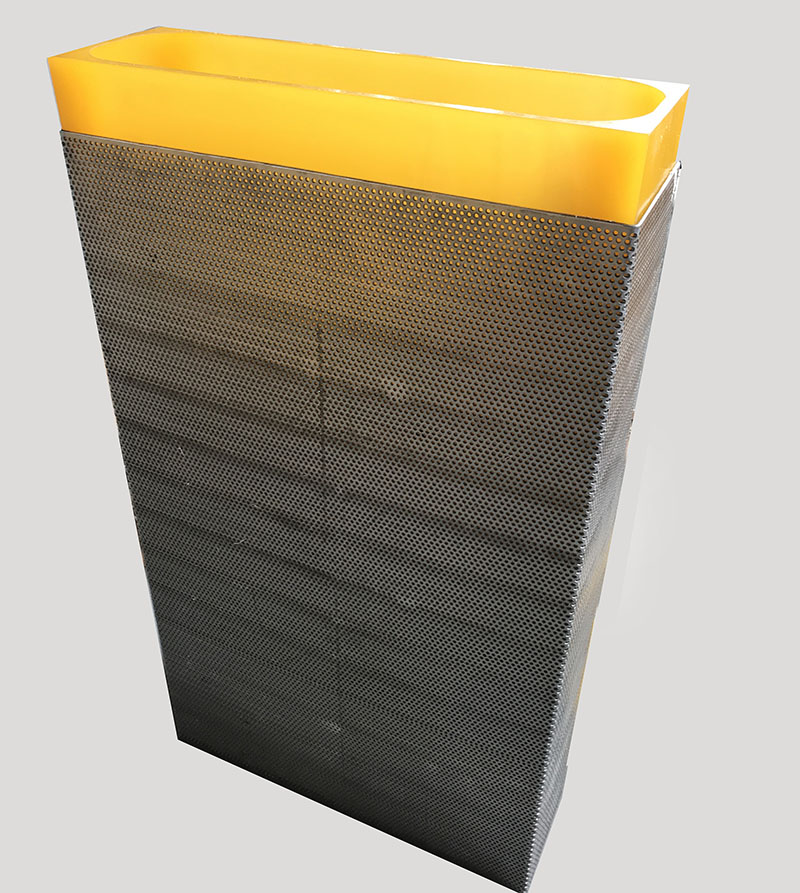
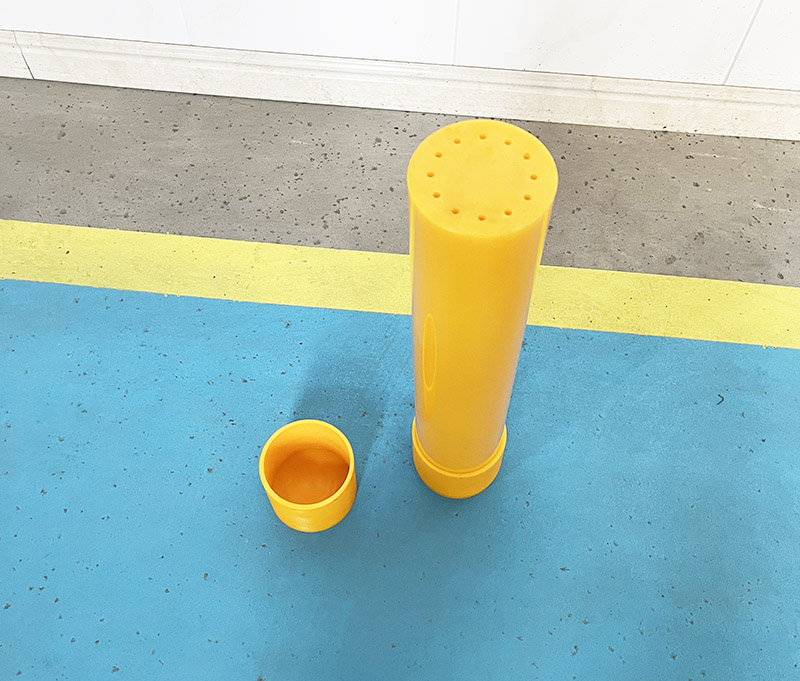
We support all kinds of customization, if you need it, please contact us.
Phone/whatsapp:+86 18234744811
Email:sales@highindustryco.com
Polyurethane Products Pu Products Rubber Mold Plastic Mold