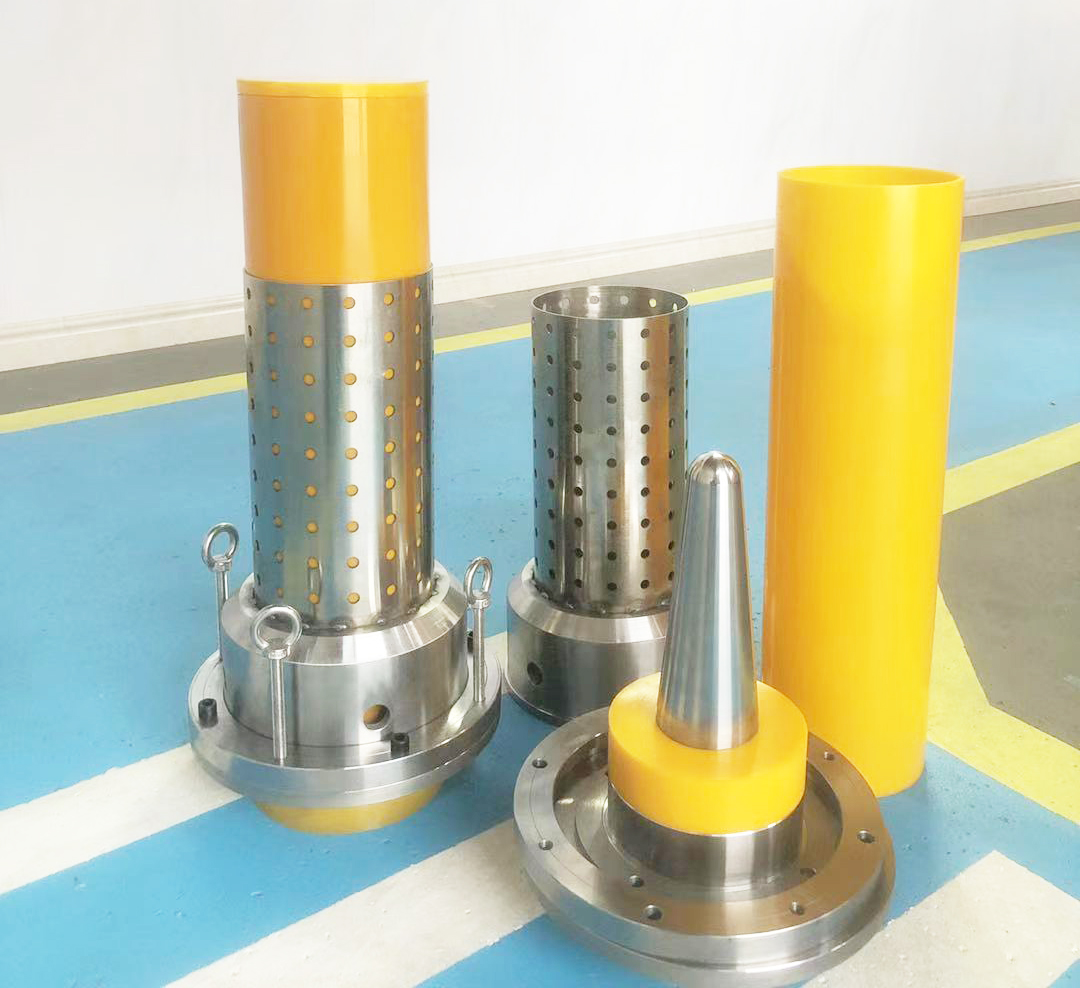
Isostatic Pressing Molds for PTFE
Categories: Cold isostatic pressing mold
Application: Isostatic Pressing Molds for PTFE
InquiryMain description:
Isostatic Pressing Molds for PTFE
Isostatic Pressing Molds for PTFE
Isostatic Pressing Molds for PTFE
Processing method of polytetrafluoroethylene
1. Compression molding
Compression molding is currently the most widely used molding processing method for PTFE. The compression molding process is a method in which certain molding raw materials (powder, pellets, fibrous materials, etc.) are put into a metal mold and formed under a certain temperature and pressure. The polymer processed by compression molding is not limited by its molecular weight, and almost all plastics can be processed by compression molding. The main characteristics of compression molding are: low cost, simple equipment, less investment, and not limited by the molecular weight of the processed plastic; the disadvantages are low production efficiency, high labor intensity, and unstable product quality. The relative molecular weight of PTFE is too high, and its fluidity is extremely poor. When other processing methods are immature, countries around the world mainly use compression molding to process PTFE products.
The specific process of compression molding is divided into: ① pressing-sintering-pressing method; ② sintering-pressing method; ③ rapid heating-pressing method; ④ pressing and sintering simultaneous method.
2. Hydroforming
The hydraulic method, also known as the equalization method and the equal pressure method, is to add PTFE resin evenly between the rubber bag and the mold wall, and then inject liquid (commonly used water) into the rubber bag, and the rubber bag that generates pressure expands to the mold wall and compacts. A method of making a preform from a resin. This method can be used to manufacture larger sleeves, bottomed storage tanks, hemispherical shells, tower columns, large slabs, etc., and can also be used to manufacture tees, elbows, profiled materials, etc. that are integrally lined with PTFE composite structures. Products with complex shapes. The main advantage of hydroforming is that the equipment and mold structure are simple. An ordinary water pump replaces a high-tonnage press. The product is evenly pressed and has a consistent density. It can manufacture large components with complex shapes and simple lining structures.
3. Push forming
Pushing, also known as paste extrusion molding, mixes 20-30 mesh dispersed resin and organic additives (toluene, petroleum ether, solvent oil, etc., the ratio of resin weight is 1/5) to make a paste, It is pre-pressed into a thick-walled round blank, and then put it into the blank of the pusher, and is pushed and formed by a plunger under heating. After drying, it is sintered at a temperature of 360~380C, and after cooling, products such as tough push tubes and rods can be obtained. Pushing products are limited to rods with a diameter of less than 16mm and pipes with a wall thickness of less than 3mm.
A samples of the isostatic pressing molds
We support all kinds of customization, if you need it, please contact us.
Phone/whatsapp:+86 18234744811
Email:sales@highindustryco.com