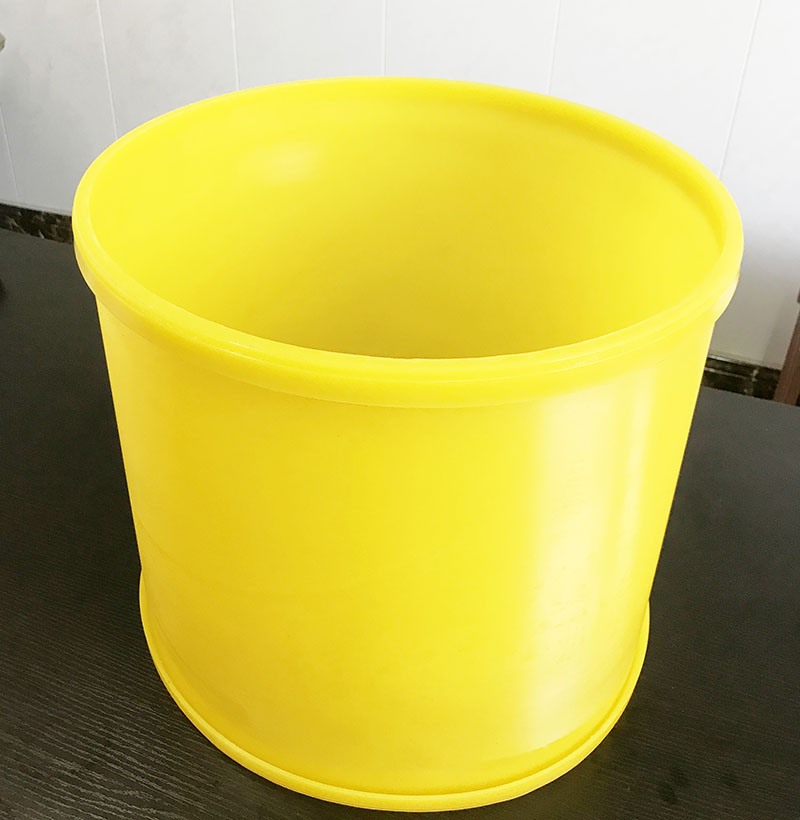
CIP Toolings for Powder Molding
Categories: Cold isostatic pressing mold
Application: CIP Toolings for Powder Molding
InquiryMain description:
CIP Toolings for Powder Molding
CIP Toolings for Powder Molding
CIP Toolings for Powder Molding
The cold isostatic pressing process (CIP) has been successfully used by manufacturers around the world for more than several decades, after which a metal or ceramic powder is made into a semi-finished product, which is then subjected to other processing such as machining or sintering.
The conventional use pressure of CIP ranges from 1,035 to 4,138 bar (15,000 to 60,000 psi), and the temperature can reach 93 degrees Celsius, which can achieve a theoretical density of 95% for ceramic materials.
Reliable processes for high performance materials
CIP is commonly used in the bonding of ceramic powders, graphite pressing, refractories and electrical insulation materials, and in the field of fine ceramics in the dental and medical industries.
This technology is also used in some new industry applications, such as the pressing of sputtering targets, the coating of valve bodies to reduce engine cylinder head wear, the communications industry, the electronics industry, the aerospace industry, and the automotive industry.
Jiangsu High Industry focuses on the research and production of isostatic pressing moulds, customizes various dry bag and cold isostatic pressing moulds, adapts to different models of various manufacturers at home and abroad, and deeply understands the needs of various industries. Alloy, graphite and other industries provide high-performance isostatic pressing mold rubber sleeves.
Product overview: Isostatic pressing rubber mold is used for the molding of ceramic materials, tungsten and molybdenum materials, graphite materials, refractory materials, and alloy powders. It can be customized according to drawings, and can be designed according to samples.
Product features: The deformation of the elastic mold under the pressure of the liquid medium is transmitted to the powder in the mold. The friction between the powder and the mold wall is small, the blank is uniformly stressed, and the density distribution is uniform, and the pre-pressed blank is encapsulated. In the elastic rubber mold, it is put into the high-pressure cylinder after sealing, and the green body is compressed and formed by liquid transfer.
Product advantages: The design of the mold cover is reasonable to ensure no water leakage, the blank is well formed, and the service life is long, including the fixture for processing the blank, which can be customized! There is a free amount of open steel molds.
We support all kinds of customization, if you need it, please contact us.
Phone/whatsapp:+86 18234744811
Email:sales@highindustryco.com