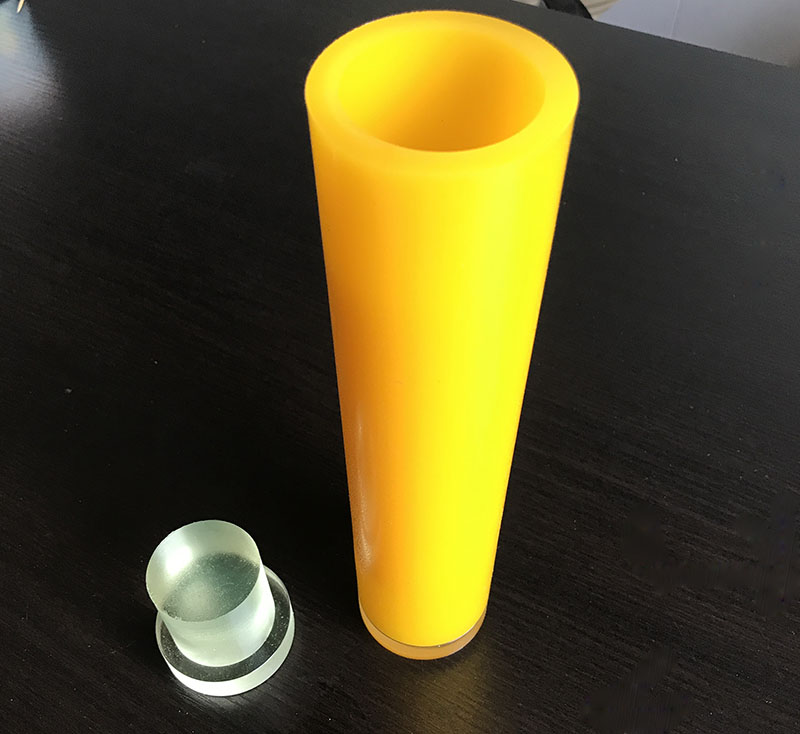
CIP Bags for Powder Metallurgy
Categories: CIP bags, CIP mold
Application: CIP Bags for Powder Metallurgy
InquiryMain description:
CIP Bags for Powder Metallurgy
CIP Bags for Powder Metallurgy
CIP Bags for Powder Metallurgy
Powder metallurgy compacting machine compaction is the process of compacting the powder in the mold or other containers into a compact of predetermined shape and size under the action of external force. The powder is loaded into the female mold, which is pressed by upper and lower punches. During the compression process, as the powder moves and deforms, the larger voids are filled, the oxide film on the surface of the particles is broken, and the contact area between the particles increases, so that the attraction between the atoms is generated and the mechanical wedging between the particles is enhanced. Thus forming a compact with a certain density and strength.
The pressure acts directly on the powder body or the elastic mold sleeve, so that the powder body is evenly pressed in all directions at the same time to obtain a compact with uniform density distribution and high strength. According to its characteristics, it can be divided into two categories: cold isostatic pressing and hot isostatic pressing.
Cold isostatic pressing is isostatic pressing at room temperature, and the liquid is the pressure transmission medium. Put the powder body into the elastic mold, place it in a steel body sealed container, press the liquid into the container with a high-pressure pump, and use the characteristics of the liquid to transmit pressure evenly, so that the powder body in the elastic mold is evenly pressed. Therefore, cold isostatic pressing has high density, uniformity, good mechanical properties, large size and complex shape, and has been used in the production of bars, pipes and large products.
Hot isostatic pressing of powder metallurgy puts the powder compact or the powder body in a special container into the high pressure container of the hot isostatic press, and applies high temperature and high pressure to make these powder bodies be pressed and sintered into dense parts or materials the process of. Isostatic pressing at high temperature can activate the occurrence of diffusion and creep phenomena, promote atomic diffusion and recrystallization of the powder, and plastic deformation at a very slow rate, and the gas is the pressure transmission medium. The powder body is subjected to the combined action of high temperature and high pressure at the same time in the isostatic high-pressure container, which strengthens the pressing and sintering process. The pressing pressure and sintering temperature of the product are lower than cold isostatic pressing, and the product has high density and strength, and Uniform and consistent, fine grains, high mechanical properties, eliminating defects and pores between particles inside the material, and the shape and size are not limited. But the hot isostatic press is expensive and requires a lot of investment. Hot isostatic pressing has been used in the production of powdered high-speed steel, refractory metals, high-temperature alloys and cermets.
Jiangsu High Industry focuses on the research and production of isostatic pressing moulds, customizes various dry bag and cold isostatic pressing moulds, adapts to different models of various manufacturers at home and abroad, and deeply understands the needs of various industries. Alloy, graphite and other industries provide high-performance isostatic pressing mold rubber sleeves.
Product overview: Isostatic pressing rubber mold is used for the molding of ceramic materials, tungsten and molybdenum materials, graphite materials, refractory materials, and alloy powders. It can be customized according to drawings, and can be designed according to samples.
Product features: The deformation of the elastic mold under the pressure of the liquid medium is transmitted to the powder in the mold. The friction between the powder and the mold wall is small, the blank is uniformly stressed, and the density distribution is uniform, and the pre-pressed blank is encapsulated. In the elastic rubber mold, it is put into the high-pressure cylinder after sealing, and the green body is compressed and formed by liquid transfer.
Product advantages: The design of the mold cover is reasonable to ensure no water leakage, the blank is well formed, and the service life is long, including the fixture for processing the blank, which can be customized! There is a free amount of open steel molds.
We support all kinds of customization, if you need it, please contact us.
Phone/whatsapp:+86 18234744811
Email:sales@highindustryco.com