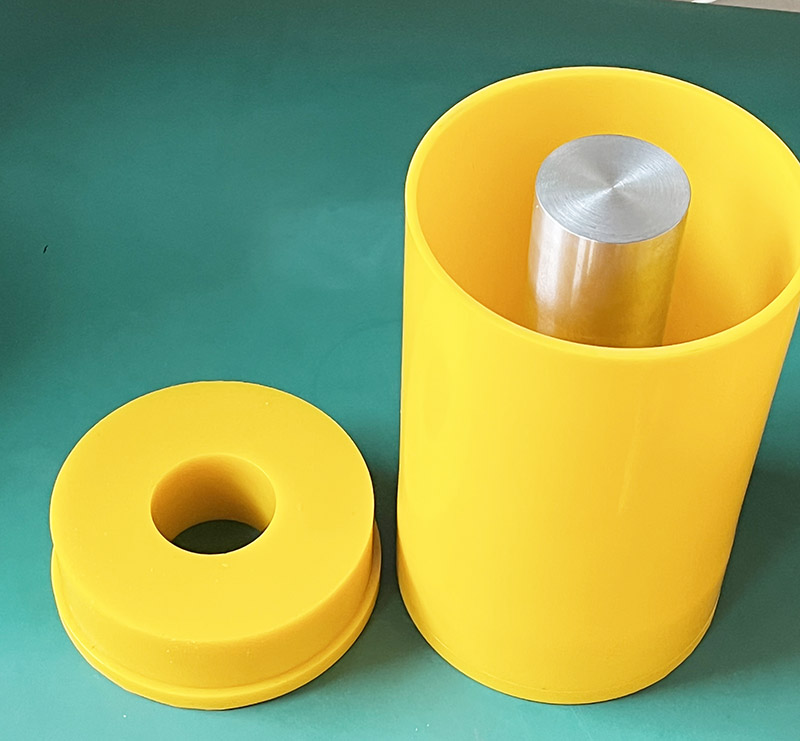
Isostatic Pressing Bags for Powder Metallurgy
Categories: Powder metallurgy bag mold
Application: Isostatic Pressing Bags for Powder Metallurgy
InquiryMain description:
Isostatic Pressing Bags for Powder Metallurgy
Isostatic Pressing Bags for Powder Metallurgy
Isostatic Pressing Bags for Powder Metallurgy
The method of achieving densification by transmitting pressure through liquid or gas to uniformly press the powder in all directions is called isostatic pressing, or isostatic pressing for short. Isostatic pressing can be divided into cold isostatic pressing and hot isostatic pressing.
(1) Cold isostatic pressing: Usually, the powder is sealed in a soft sheath, and then placed in a liquid medium in a high-pressure container. By applying pressure to the liquid, the powder is uniformly pressed in all directions to obtain the required pressure. Blank. The liquid medium can be oil, water or glycerin. The sheath material is an elastic-plastic material such as rubber. Metal powder can be directly loaded or molded to fit the sleeve. Because the powder is uniformly pressed in all directions in the sheath, a compact with a relatively uniform density can be obtained, so it is not easy to deform and crack during sintering. The disadvantage is that the dimensional accuracy of the compact is poor, and machining is required. Cold isostatic pressing has been widely used in the forming of hard alloys, refractory metals and other various powder materials.
(2) Hot isostatic pressing: put the metal powder into a sheath that is easy to deform at high temperature, and then place it in a sealable cylinder (a high-pressure container with a heating body on the inner wall), and use a compressor after closing the cylinder Pour in the gas and turn on the electricity to heat. As the temperature increases, the gas pressure in the cylinder increases. Under the action of this isotropic uniform pressure and temperature, the powder becomes a product with a certain shape. The pressurized medium is generally argon. Commonly used sheath materials are metals (mild steel, stainless steel, titanium), glass and ceramics are also available. Due to the simultaneous action of temperature and isostatic pressure, many difficult-to-form materials can reach or approach theoretical density, and have fine grains, uniform structure, isotropy and excellent performance. The hot isostatic pressing method is most suitable for the production of materials and products such as cemented carbide, powder superalloy, powder high-speed steel and metal beryllium; it can also be used for secondary treatment of cast products to eliminate pores and micro-cracks; it can also be used to manufacture different materials Closely bonded multilayer or composite materials and articles. There are about 20 advanced hot isostatic presses with rapid cycle performance in the world, which are mainly used for the preparation of aviation components, medical implants, wear-resistant parts, industrial pneumatic turbines and jet targets.
Jiangsu High Industry focuses on the research and production of isostatic pressing moulds, customizes various dry bag and cold isostatic pressing moulds, adapts to different models of various manufacturers at home and abroad, and deeply understands the needs of various industries. Alloy, graphite and other industries provide high-performance isostatic pressing mold rubber sleeves.
Product overview: Isostatic pressing rubber mold is used for the molding of ceramic materials, tungsten and molybdenum materials, graphite materials, refractory materials, and alloy powders. It can be customized according to drawings, and can be designed according to samples.
Product features: The deformation of the elastic mold under the pressure of the liquid medium is transmitted to the powder in the mold. The friction between the powder and the mold wall is small, the blank is uniformly stressed, and the density distribution is uniform, and the pre-pressed blank is encapsulated. In the elastic rubber mold, it is put into the high-pressure cylinder after sealing, and the green body is compressed and formed by liquid transfer.
Product advantages: The design of the mold cover is reasonable to ensure no water leakage, the blank is well formed, and the service life is long, including the fixture for processing the blank, which can be customized! There is a free amount of open steel molds.
We support all kinds of customization, if you need it, please contact us.
Phone/whatsapp:+86 18234744811
Email:sales@highindustryco.com