PTFE Isostatic Pressing Molds
Polytetrafluoroethylene (PTFE) mainly adopts forming, hydraulic, pushing, extrusion, spraying, bonding, welding and winding molding technology. The first five mainly use PTFE resin direct processing, after three kinds of PTFE plastic sheet or thin strip, in addition, there are rolling method, hot forming method and other forming methods, now a brief introduction of various forming methods.
1. Molding method
Most molding is done with suspended resin. Disperse resins are used when making sheets less than 1.5mm thick. Its technological process: Resin - sifting (suspended resin is mashed, loosened, and sifted through a 20-mesh sieve) - press (PTFE powder loaded into the mold under 20-235Mpa pressure, Compaction molding by press) -sintering (sintering in the sintering furnace at 370℃-380℃ temperature) -molded finished products (in the mold or free state cooling and shaping into the required plate, rod, tube, washer and packing products, etc.).
2. Hydraulic method
Hydraulic method, also known as the isobaric method or rubber bag method, is a special method of making PTFE products, is to apply hydraulic pressure to rubber bag rubber bag will expand PTFE resin to the mold, so that the compacting after burning products. The basic operation process is as follows: put the rubber bag in the outer mold - connect the water pump, fill with tap water to make the rubber bag expand into a cylindrical shape - resin evenly added between the bag and the outer mold - close the mold - continue to fill with water and gradually increase the water pressure, up to 12-13Mpa, maintain the pressure for 30min, then release the water - decompression, mold removal, sintering, cooling is the appearance of clean preproduct.
3. Push and press
Push and press, also known as paste extrusion molding. 20-30 mesh sifted disperse resin and organic liquid (toluene, petroleum ether, solvent oil, etc.) were prepared into a 1:5 paste mixture, prepressed into thick wall cylindrical billet, put into the press cylinder, heating. Extrusion molding with plunger, after drying and sintering at 360-380℃, after cooling to get strong extrusion tube, rod and other products.
4. Squeeze method
Extrusion molding can be divided into two kinds of screw extrusion and plunger extrusion, the pre-sintered resin after grinding and sifting is added to the barrel, through the rotation of the screw or the reciprocating push of the plunger. The raw materials are transferred to the extruder by side compaction, and are continuously extruded, sintered and cooled at 360-400℃ to form various pipe and rod products.
5. Spraying
There are two kinds of spraying process: PTFE emulsion coating and PTFE resin powder plasma coating.
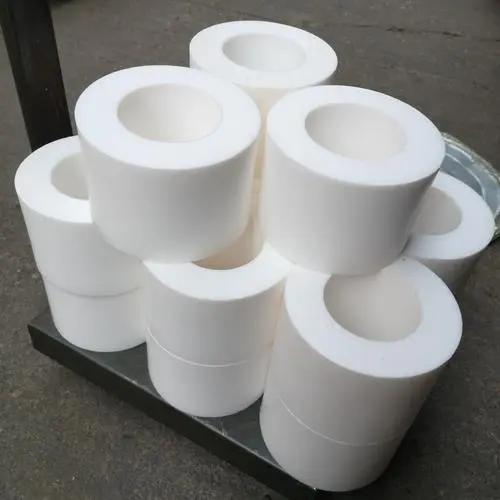
Jiangsu High Industry on the research and development and production of high-performance polyurethane isostatic pressing molds. Through in-depth cooperation with many isostatic pressing equipment manufacturers and in-depth study of the industry, the developed isostatic pressing polyurethane mold series products have the characteristics of long service life, high precision, small deformation, easy demoulding, etc., and are widely used in ceramics, etc. Static pressing mould, cemented carbide isostatic pressing mould, rare earth permanent magnet material isostatic pressing mould, graphite isostatic pressing mould, etc.
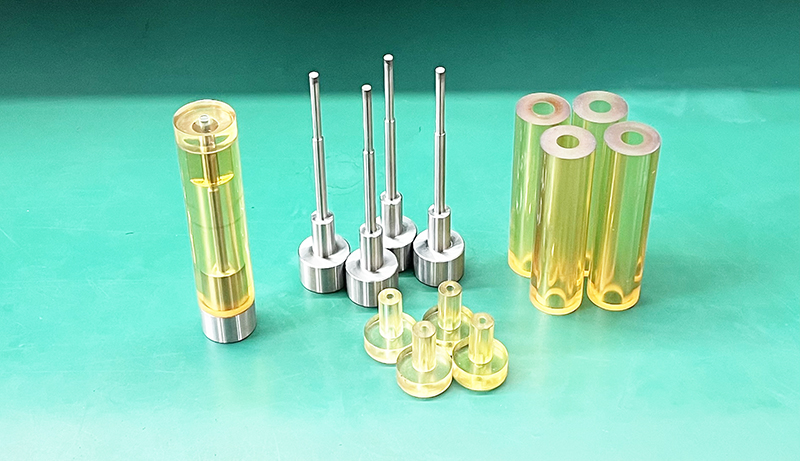
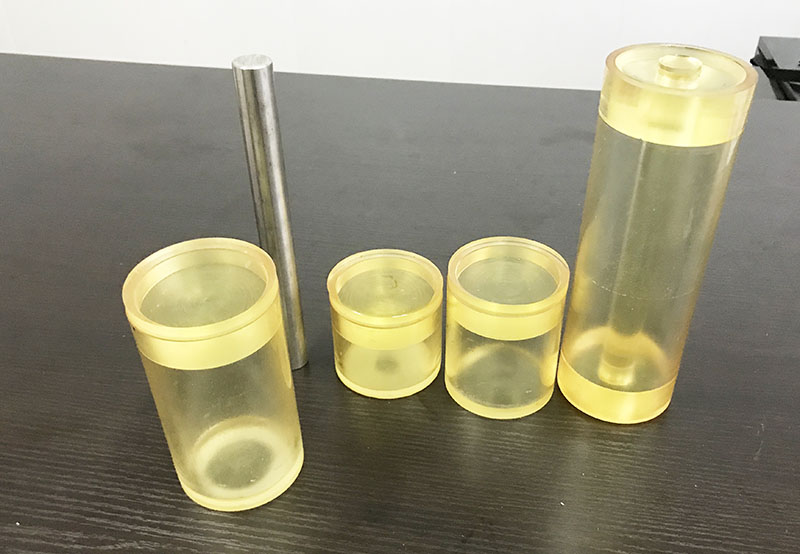
We support all kinds of customization, if you need it, please contact us.
Phone/whatsapp:+86 18234744811
Email:sales@highindustryco.com
Polyurethane Products Pu Products Rubber Mold Plastic Mold