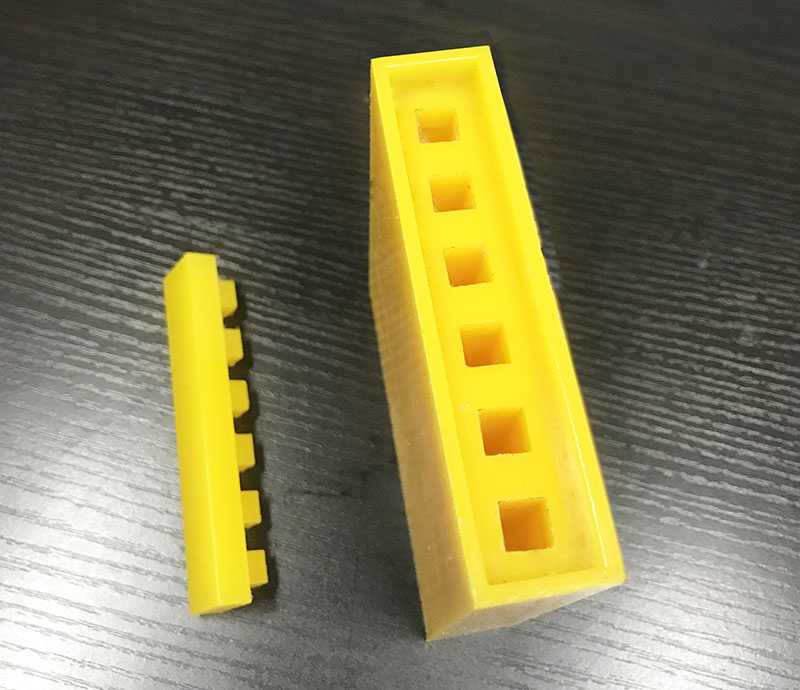
Ceramic Isostatic Pressing Bags
Categories: Isopressing mold
Application: Ceramic Isostatic Pressing Bags
InquiryMain description:
Ceramic Isostatic Pressing Bags
Ceramic Isostatic Pressing Bags
Ceramic Isostatic Pressing Bags
Isostatic pressing of ceramics
Isostatic pressing is usually referred to as cold isostatic pressing. It is a method of applying uniform static pressure to materials by using fluid as a transfer medium. That is to use the incompressibility of the liquid medium to evenly transfer the pressure, from all directions for pressure, product forming method. According to its forming process, it can be divided into two forms: wet bag type and dry bag type. At present, the wet bag method is mainly used in large quantities.
1. Wet bag isostatic pressure
Wet bag isostatic pressing technology is to put granulated ceramic powder or pre-formed billet into the deformable rubber envelope, and then apply uniform pressure through the liquid, when the pressing process is over, and then the rubber envelope with billet body out of the container, this is a discontinuous forming method.
The cost of this technology is relatively low, can form moderately complex parts, and the pressure can be up to 500MPa, suitable for small-scale production, but in a certain period of time the number of molding products is small, the size and shape of the billet is not accurately controlled, the production efficiency is not high, can not be continuous large-scale production.
2. Dry bag isostatic pressure
Dry bag isostatic pressing is the process of filling a batch of ceramic powder into a flexible preformed die and then applying isostatic pressing. Since the die is fixed to the device, when the pressing is complete, the molded product is pushed out, as shown in the diagram.
Dry bag isostatic pressing has short molding cycle and long service life, which is especially convenient for large-scale continuous chemical industry production. The mold material used is polyurethane synthetic rubber or silicone rubber. Compared with wet bag type isostatic pressing, dry bag type isostatic pressure is lower, generally within 200MPa. The most familiar ceramic spark plug is currently formed by dry bag type isostatic pressing, pressing time is usually only 1~2S.
Advantages of isostatic pressing:
· The pressure is transmitted from all directions, and the compact density is evenly distributed and the compact strength is high.
· The blank has high density, less uniform defects, and lower burning shrinkage than normal dry;
· Can be pressed with concave, slender and other complex shape parts;
· Low friction loss, low forming pressure;
· Mould cost is low.
· The disadvantages of isostatic pressing: the size and shape of the billet is not easy to control accurately, the productivity is low, and it is not easy to realize automation;
Application:
Wet isostatic pressing technology is used for large thin-walled, high precision and high performance alumina ceramic radome and large thick wall, complex shape, and 97% alumina ceramic high frequency terminal insulation porcelain sleeve with parachute edge.
95% alumina ceramic vacuum switch arc extinguishing chamber "shell" series products, alumina and zirconia ceramic plungers, as well as large size zirconia ceramic cylinder liner for oil drilling using isostatic pressure technology.
Dry bag isostatic pressure technique is widely used in transparent alumina ceramic tube and alumina spark plug for high pressure sodium lamp.
Jiangsu High Industry focuses on the research and production of isostatic pressing moulds, customizes various dry bag and cold isostatic pressing moulds, adapts to different models of various manufacturers at home and abroad, and deeply understands the needs of various industries. Alloy, graphite and other industries provide high-performance isostatic pressing mold rubber sleeves.
We support all kinds of customization, if you need it, please contact us.
Phone/whatsapp:+86 18234744811
Email:sales@highindustryco.com