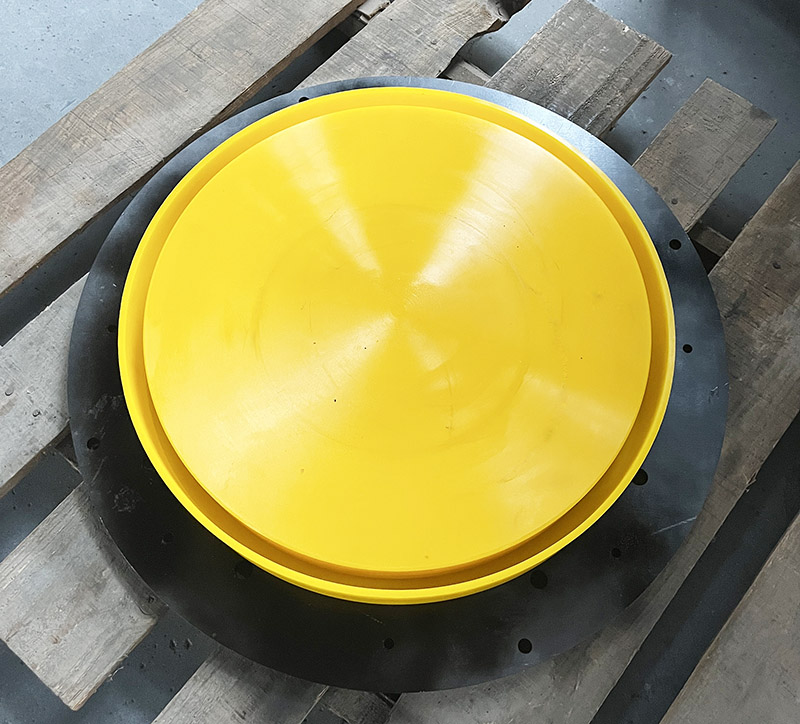
The Advantages of Isostatic Pressing Technology
Categories: Isopressing mold
Application: The Advantages of Isostatic Pressing Technology
InquiryMain description:
The Advantages of Isostatic Pressing Technology
The Advantages of Isostatic Pressing Technology
The Advantages of Isostatic Pressing Technology
Isostatic pressing technology is a new powder forming and consolidation technology developed according to PASCAL's principle. PASCAL's principle is also known as the static pressure transfer principle. Its main content is that the pressure applied to a closed liquid can be transferred from the liquid to all directions with a constant amount. That is to say, in a closed container, the pressure applied to a stationary liquid will be transmitted to all points at the same time. Isostatic pressure technology was developed by Westinghouse light bulb Company in 1913. Since then, the technology has developed rapidly and has been widely used in casting, atomic energy, plastics, graphite, ceramics, permanent magnets, biological drug preparation, food preservation and military industry.
According to the sample forming and consolidation temperature classification, isostatic pressing technology can be divided into cold isostatic pressing, warm isostatic pressing and hot isostatic pressing. Cold isostatic pressing technology refers to the isostatic pressing molding technology at room temperature. It usually uses rubber and plastic as envelope mold materials, takes liquid as pressure medium, and the working pressure range is 100~ 630MPa. It is mainly used for powder forming. Its purpose is to provide prefabricated products for the next sintering, calcining or hot isostatic pressing processes. Temperature isostatic pressing technology generally refers to the pressing temperature is not more than 500℃ isostatic pressing technology, with special liquid or gas as the pressure medium, the working pressure range is about 300MPa, mainly used at room temperature conditions can not be compacting powder materials (such as graphite, polyamide, rubber, etc.) pressing, so that it can be formed at a higher temperature, get solid body. Hot isostatic pressing technology is a process technology that makes materials undergo isostatic pressing and solidification under high temperature conditions. Generally, inert gases such as argon and ammonia are used as pressure transfer medium. Metal or glass is usually used as the coating mold material, with the working temperature range of 1000~2200℃ and the working pressure range of 100~200MPa. It is not only used for the forming and sintering of powder, but also for the diffusion bonding of the workpiece, the elimination of casting defects, the production of complex shape parts, etc.
As a new type of powder forming and consolidation process, isostatic pressure technology has the following characteristics:
1. High compact density. The density of samples formed by isostatic pressing is generally 5 ~ 15% higher than that of unidirectional and bidirectional molding. The relative density of samples prepared by hot isostatic pressing can reach 99.8 ~ 99.09%.
2. The compact density is uniform. In the process of molding, whether one-way or two-way pressing, due to the existence of friction resistance between powder and steel die, as well as the decline of forming pressure in the process of transfer, it will cause uneven distribution of compact density. This density difference can often reach more than 10% when pressing complex shape products. In isostatic pressing, the force on all sides of the powder is equal, the force contraction of the mold and the powder is roughly the same, the relative motion is small, the pressure is only slightly decreased, the density difference of each part of the prepared sample is less than 1%, so the density distribution can be considered to be uniform.
3. It can prepare samples with large length-diameter ratio and complex shape. Because in the forming process, the force of the blank body everywhere is the same, the density distribution is uniform, so it can make the length-diameter ratio is large, the shape of the complex sample.
4. Isostatic pressing molding process, generally do not need to add lubricant in powder, which not only reduces the pollution of products, but also simplifies the manufacturing process.
5. The products formed by isostatic pressing have excellent anisotropic physical properties and lower sintering temperature than the samples obtained by other forming methods.
Jiangsu High Industry focuses on the research and production of isostatic pressing moulds, customizes various dry bag and cold isostatic pressing moulds, adapts to different models of various manufacturers at home and abroad, and deeply understands the needs of various industries. Alloy, graphite and other industries provide high-performance isostatic pressing mold rubber sleeves.
We support all kinds of customization, if you need it, please contact us.
Phone/whatsapp:+86 18234744811
Email:sales@highindustryco.com