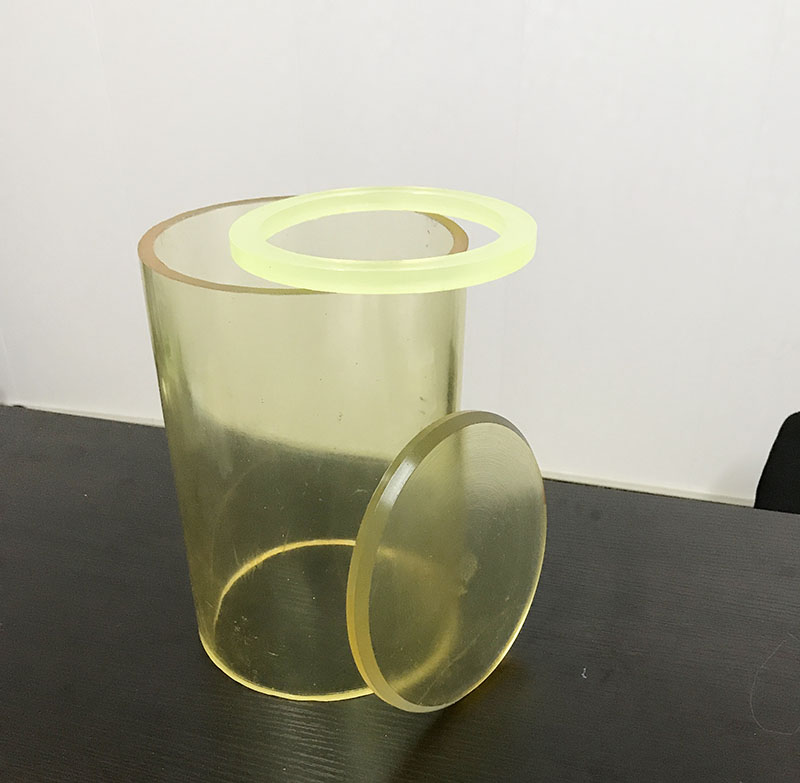
Cold Isostatic Pressing and Hot Isostatic Pressing
Categories: CIP bags, CIP mold
Application: Cold Isostatic Pressing and Cold Isostatic Pressing Ceramic
InquiryMain description:
Cold Isostatic Pressing and Cold Isostatic Pressing Ceramic
Cold Isostatic Pressing and Cold Isostatic Pressing Ceramic
Cold Isostatic Pressing and Hot Isostatic Pressing
The principle of isostatic processing: Use a high-pressure pump to press the pressure-transmitting fluid medium into a closed container, and the workpiece in the container is formed under the static pressure of the high-pressure fluid medium to become a dense body or bonded together. The isostatic pressing process can make the workpiece obtain uniform compressive stress in all directions. According to the processing temperature, it can be divided into cold isostatic pressing and hot isostatic pressing.
Cold isostatic pressing is divided into dry bag molding and wet bag molding according to different powder loading methods. The fundamental difference between the two is: the formed rubber bag pressed by the dry bag mold is not soaked in the liquid medium, after the pressing is completed, the briquette and the formed mold bag are taken out, while the pressurized rubber bag remains in the container for the next filling; The mold bag pressed by the bag mold has a long service life and high production efficiency, and is suitable for single-piece continuous production. Wet bag molding is a commonly used pressing process. After loading, the mold bag is placed in a container and soaked in a liquid medium. After pressing, the mold bag and blank are taken out at the same time. This process can simultaneously press pressed parts of various shapes, but it takes a long time to demould.
Processing is performed using hydrostatic pressure generated by a high temperature gas (argon or helium). In 1955, the Shane Research Institute of the United States first successfully developed it, and it was applied in industry in the early 1960s, which solved the problem of diffusion bonding of nuclear fuel elements. Early hot isostatic pressing is also called "gas-pressure bonding" (gas-pressure bonding), "gas-pressure consolidation" (gas-pressure consolidation). From the mid-1960s to the early 1970s, due to the emergence and application of gas atomization and centrifugal atomization to produce high-performance powder technology, the hot isostatic pressing process has been greatly developed and has become a method of industrial production. The hot isostatic pressing process is pressurized and formed at high temperature, so the obtained product has less pores, the density is similar to that of the smelted processed material, and the grain is fine and the isotropic property is uniform.
Therefore: as an advanced forming technology, isostatic pressing technology has obvious advantages compared with traditional forming technology, mainly in:
First: The product formed by isostatic pressing has high density and uniform distribution, no bubbles inside the product, and low microporosity between the grains of the finished product. Its mechanical and electrical properties are better than other forming methods.
Second: The isostatic pressed product has almost no internal stress, and the compact can be sintered directly into the kiln without warping or cracking.
Third: It is easy to make products with a large aspect ratio (the ratio of length to diameter), while other methods are half the effort or impossible to achieve.
Fourth: Make large-scale products and products with complex shapes with high melting point and high hardness materials.
Fifth: The green body formed by isostatic pressing has a lower firing temperature than the green body obtained by other forming methods and will not pollute the high-purity green compact material.
Jiangsu High Industry on the research and development and production of high-performance polyurethane isostatic pressing molds. Through in-depth cooperation with many isostatic pressing equipment manufacturers and in-depth study of the industry, the developed isostatic pressing polyurethane mold series products have the characteristics of long service life, high precision, small deformation, easy demoulding, etc., and are widely used in ceramics, etc. Static pressing mould, cemented carbide isostatic pressing mould, rare earth permanent magnet material isostatic pressing mould, graphite isostatic pressing mould, etc.
We support all kinds of customization, if you need it, please contact us.
Phone/whatsapp:+86 18234744811
Email:sales@highindustryco.com