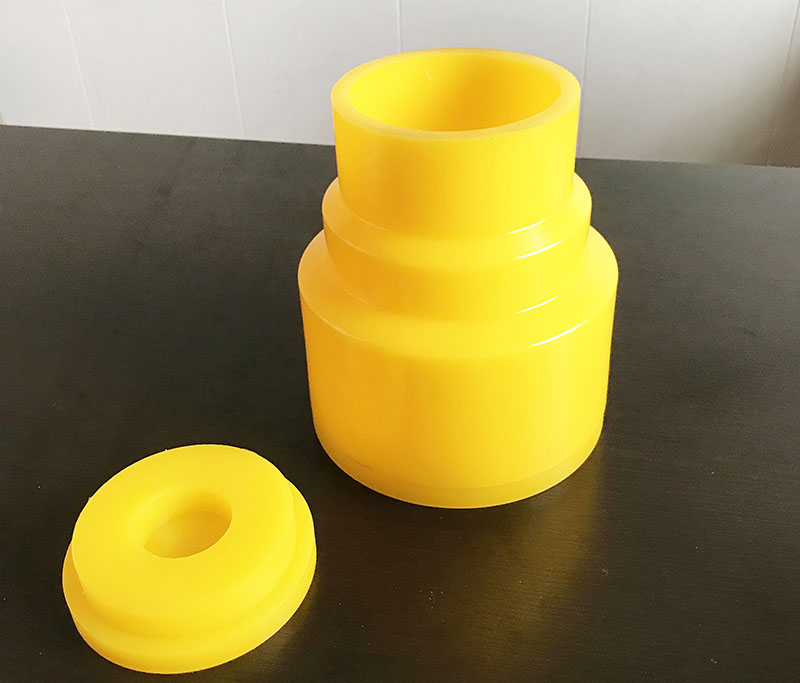
Cold Isostatic Pressed Carbide
Categories: Polyurethane CIP bag mold
Application: Cold Isostatic Pressed Carbide
InquiryMain description:
Cold Isostatic Pressed Carbide
Cold Isostatic Pressed Carbide
Cold Isostatic Pressed Carbide
Cemented carbide rods are widely used in metal processing, electronics industry, wood processing, aerospace industry and medicine because of their special wear resistance, high hardness, excellent fracture toughness and compressive strength. Ideal pre-material for printed circuit board micro drills, milling cutters, reamers, step cutters, long rod cutters, taps and dot matrix printer pins, etc. With the development of science and technology, the demand for cemented carbide rods is increasing, and the forming technology has developed from traditional processes such as cold isostatic pressing and molding to more modern and economical extrusion forming processes, and the quality is getting better and better. There are more and more varieties.
CIP Process for Cemented Carbide Rod Forming
1.Pressure cutting method
The ground and sieved carbide powder is pressed into a block, and then subjected to cold isostatic pressing before subsequent processing. In this process, as long as a small amount of plasticizers, such as paraffin, polyethylene glycol and so on. If the pressure of cold isostatic pressing is high enough (400MPa), no binder can even be added. The bar formed by this method has a very rough surface and must be ground and turned before the finished product.
2. Wet bag method
The mold is evenly pressed in the high-pressure liquid (about 200MPa), and the size of the test piece is limited by the mold cavity, which is not suitable for mass production and is mainly used for large-diameter bars.
3. Dry bag method
It uses different fluids as the pressure transmission medium, the mold is semi-fixed, and the addition and removal of blanks are all operated in a dry state. High degree of automation, short operation cycle, suitable for batch molding. The length of the rod formed by this method is longer than that of the mechanical molding method (up to 400mm), and a small amount (1% to 1.5%) of paraffin or polyvinyl alcohol is used for molding.
In addition, the dry bag method can produce rods with cooling channels. Process a spiral groove on the outer surface of the blank, put elastic fibers in the spiral groove, put it into the mold body, fill the gap between the blank and the mold body with powder, and then apply pressure to the dry bag mold body to The blank and the granules are pressed against each other, and the elastic fibers in the groove are deformed violently. During the subsequent dewaxing and sintering process, the forming agent evaporates from the powder, blank and elastic fiber, so that a rod with cooling channels is produced. Due to the manufacturing method and the softness of the blank, the position accuracy of the manufactured cooling channels is not high.
Jiangsu High Industry focuses on the research and production of isostatic pressing moulds, customizes various dry bag and cold isostatic pressing moulds, adapts to different models of various manufacturers at home and abroad, and deeply understands the needs of various industries. Alloy, graphite and other industries provide high-performance isostatic pressing mold rubber sleeves.
We support all kinds of customization, if you need it, please contact us.
Phone/whatsapp:+86 18234744811
Email:sales@highindustryco.com