Isostatic Pressing
Isostatic pressing is a method in which the powder in a closed mold is uniformly pressed and formed in all directions at the same time. It uses liquid or gas as a pressure transmission medium to make the pressure uniformly transmitted to all directions of the green body, thereby obtaining a uniform density.
Isostatic pressing requires pretreatment of the powder, improving the fluidity of the powder through the granulation process, adding binders and lubricants to reduce the internal friction of the powder, increasing the bonding strength, and meeting the requirements of the molding process.
The isostatic pressing process has the characteristics of uniform product structure, high density, small sintering shrinkage, low mold cost and high production efficiency. It is mainly used for forming large-size pipes, rods, and blocks, and it is also used for cold isostatic pressing after wrapping dry-pressed products to further increase the density of the green body.
At present, large-sized aluminum nitride ceramic discs are formed into regular shapes by dry pressing, and then cold isostatic pressing is performed to further improve the density and density distribution of the green body, and reduce warping and dimensional instability caused by uneven density distribution during the sintering process. And so on, improve product quality.
Advantages: The green body has high density, uniform density distribution, and can be formed in a near net size.
Disadvantages: The molding equipment is expensive, and there is a problem of demoulding, which limits large-scale industrial production.
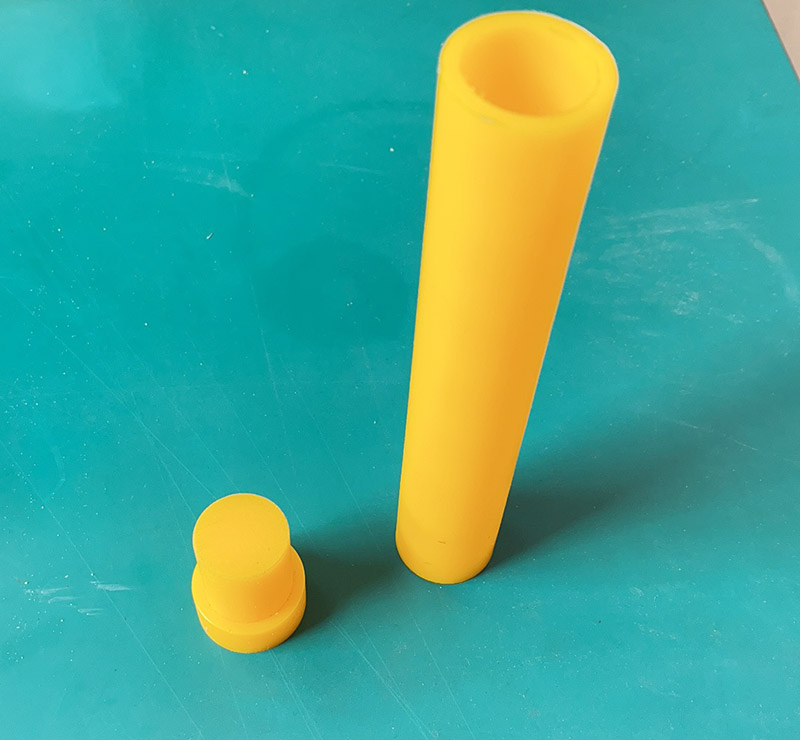
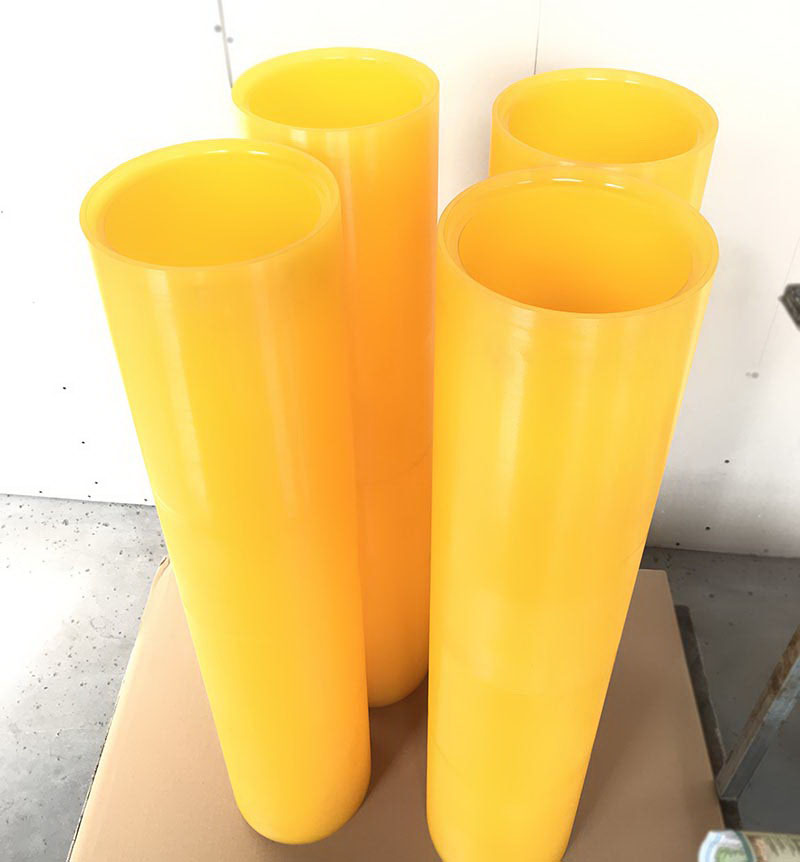
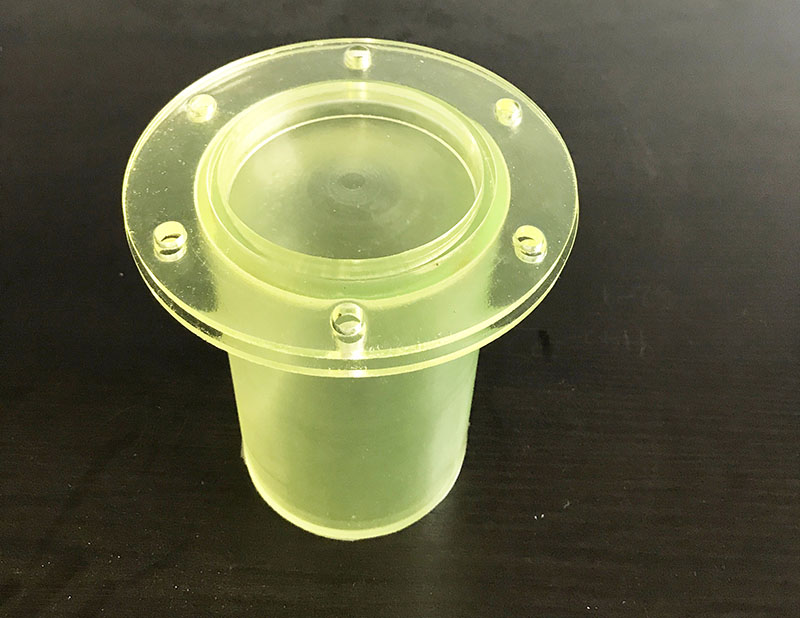
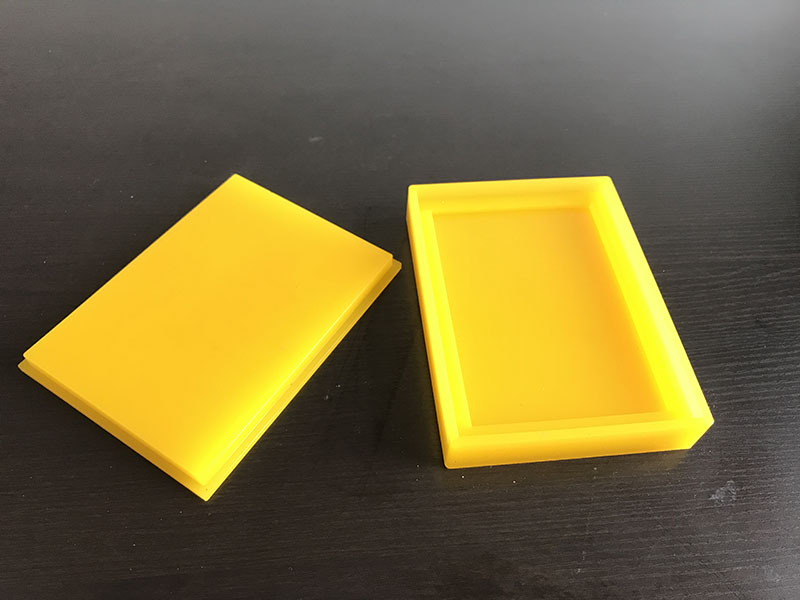
Polyurethane Products Pu Products Rubber Mold Plastic Mold