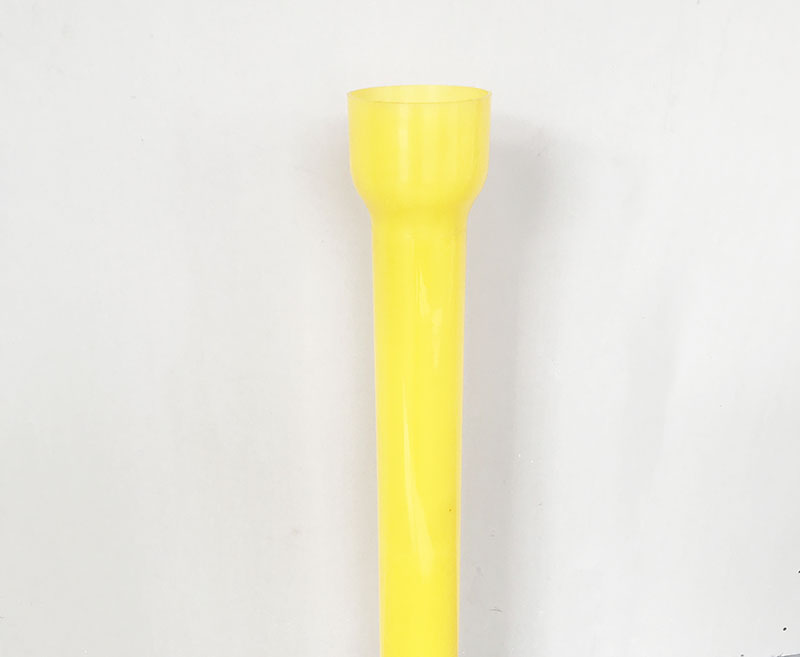
Cerramic Molding- Isostatic Pressing Molding
Categories: Dry bag DIP forming mold
Application: Cerramic Molding- Isostatic Pressing Molding
InquiryMain description:
Cerramic Molding- Isostatic Pressing Molding
Cerramic Molding- Isostatic Pressing Molding
Cerramic Molding- Isostatic Pressing Molding
Cold isostatic pressing uses a liquid medium, such as water or oil or a glycol mixture, to apply pressure to the powder. The powder is placed in a fixed-shape mold that prevents liquid from penetrating the powder. For metals, cold isostatic pressing can achieve about 100% of theoretical density, while more difficult-to-compress ceramic powders can achieve about 95% of theoretical density.
The extremely high pressure makes the voids in the powder smaller or even disappear. Under high pressure, the metal powder is deformed due to its ductility, and the ceramic powder may be slightly broken, and the density is increased, finally forming a "green body" that can be handled, processed and sintered. "Component. The typical pressure range is 100-600MPa, and the temperature is usually room temperature. If a higher temperature is required, the heat exchanger can raise the temperature to about 93°C. However, since the temperature of water will increase when it is compressed, it will increase by about 4°C for every increase of 100MPa, so the risk of boiling at higher temperatures will increase accordingly.
Cold isostatic pressing uses a liquid medium, such as water or oil or a glycol mixture, to apply pressure to the powder. The powder is placed in a fixed-shape mold that prevents liquid from penetrating the powder. For metals, cold isostatic pressing can achieve about 100% of theoretical density, while more difficult-to-compress ceramic powders can achieve about 95% of theoretical density.
The extremely high pressure makes the voids in the powder smaller or even disappear. Under high pressure, the metal powder is deformed due to its ductility, and the ceramic powder may be slightly broken, and the density is increased, finally forming a "green body" that can be handled, processed and sintered. "Component. The typical pressure range is 100-600MPa, and the temperature is usually room temperature. If a higher temperature is required, the heat exchanger can raise the temperature to about 93°C. However, since the temperature of water will increase when it is compressed, it will increase by about 4°C for every increase of 100MPa, so the risk of boiling at higher temperatures will increase accordingly.
Common applications for cold isostatic pressing include the consolidation of ceramic powders, graphite, refractories, electrical insulators, and the compression of advanced ceramics. Materials include silicon nitride, silicon carbide, boron nitride, boron carbide, titanium boride, spinel, etc. The technology is expanding into new application areas such as the pressing of sputtering targets, the coating of valve components in engines to reduce cylinder wear, telecommunications, electronics, aerospace and the automotive sector.
Cold isostatic pressing technology has the following advantages: improve the degree of consolidation of the product, increase the mechanical properties of the product, relatively centralized data in the production process, can control production more safely, very low corrosion, high efficiency and low cost. The decompression process in the cold isostatic pressing process also determines the quality of the "green" compact. As the metal or ceramic powder is compacted, gas is trapped between the particles, and the pressure increases during processing as externally applied pressure increases. Metal compacts are very strong and ductile and will naturally release entrapped air after the cold isostatic pressing process.
However, since ceramic "green" compacts are more brittle, if the pressure is released too quickly and in an uncontrolled manner, the ceramic compact is likely to rupture where air cannot escape. The way to avoid this is to release the applied pressure in a controlled manner by fine-tuning the pressure relief system, which is especially important at lower pressures where trapped air can affect the internal stresses when the applied pressure is equal to the internal gas pressure.
At present, cold isostatic pressing technology is widely used in various fields such as daily-use ceramics, architectural ceramics, and special ceramics. Such as discs, dishes, alumina grinding balls, alumina chemical filler balls, refractory bricks, ceramic sticks, spark plugs, high-frequency porcelain sleeves, composite ceramics, etc.
The so-called isostatic pressing usually refers to cold isostatic pressing, which is a method of using fluid (water, oil) as a transmission medium to obtain uniform static pressure on the material. That is, the incompressibility of the liquid medium is used to uniformly transmit the pressure, and the pressure is applied from all directions to obtain the molding method of the product. According to the different molding process, it can be divided into two forms: wet bag type and dry bag type. At present, the wet bag method is mainly used in large quantities.
Wet bag isostatic pressing
Wet bag isostatic pressing technology is to put granulated ceramic powder or preformed green body into a deformable rubber sheath, and then apply uniform pressure in all directions through the liquid. When the pressing process is over, put the green body The rubber sheath is taken out from the container, which is a discontinuous molding method.
The cost of this technology is relatively low, and it can form medium-complexity parts, and the pressure can reach 500MPa. It is suitable for small-scale production, but the number of formed products is small within a certain period of time, and the size and shape of the green compact cannot be precisely controlled. , the production efficiency is not high, and large-scale production cannot be carried out continuously.
Dry bag isostatic pressing
Dry bag isostatic pressing is to fill ceramic powder in batches into flexible preforming molds, and then apply isostatic pressing. Since the mold is fixed on the equipment, when the pressing is completed, the molded products are ejected, as shown in the schematic diagram.
Dry bag isostatic pressing has a short cycle time and long service life of the mold, which is especially convenient for large-scale continuous industrial production. The mold materials used are polyurethane synthetic rubber or silicone rubber. Compared with wet bag isostatic pressing, the pressure of dry bag isostatic pressing is lower, generally within 200MPa. The most familiar ceramic spark plug is currently formed by dry bag isostatic pressing, and the pressing time is usually only 1~2s.
Advantages of isostatic pressing:
(1) The pressure is transmitted from all directions, the density of the compact is evenly distributed, and the strength of the compact is high;
(2) The density of the green body is high, the uniform defect is less, and the firing shrinkage is lower than that of ordinary dry pressing;
(3) Capable of pressing parts with concave, slender and other complex shapes;
(4) Small friction loss and low molding pressure;
(5) The mold cost is low.
We support all kinds of customization, if you need it, please contact us.
Phone/whatsapp:+86 18234744811
Email:sales@highindustryco.com
Polyurethane Products Pu Products Rubber Mold Plastic Mold