Wet-bag Isostatic Pressing and Dry-bag Isostatic Pressing
Wet bag isostatic pressing
Wet bag isostatic pressing technology is to put granulated ceramic powder or preformed green body into a deformable rubber sheath, and then apply uniform pressure in all directions through the liquid. When the pressing process is over, put the green body The rubber sheath is taken out from the container, which is a discontinuous molding method.
The cost of this technology is relatively low, and it can form medium-complexity parts, and the pressure can reach 500MPa. It is suitable for small-scale production, but the number of formed products is small within a certain period of time, and the size and shape of the green compact cannot be precisely controlled. , the production efficiency is not high, and large-scale production cannot be carried out continuously.
Dry bag isostatic pressing
Dry bag isostatic pressing has a short cycle time and long service life of the mold, which is especially convenient for large-scale continuous industrial production. The mold materials used are polyurethane synthetic rubber or silicone rubber. Compared with wet bag isostatic pressing, the pressure of dry bag isostatic pressing is lower, generally within 200MPa. The most familiar ceramic spark plug is currently formed by dry bag isostatic pressing, and the pressing time is usually only 1~2s.
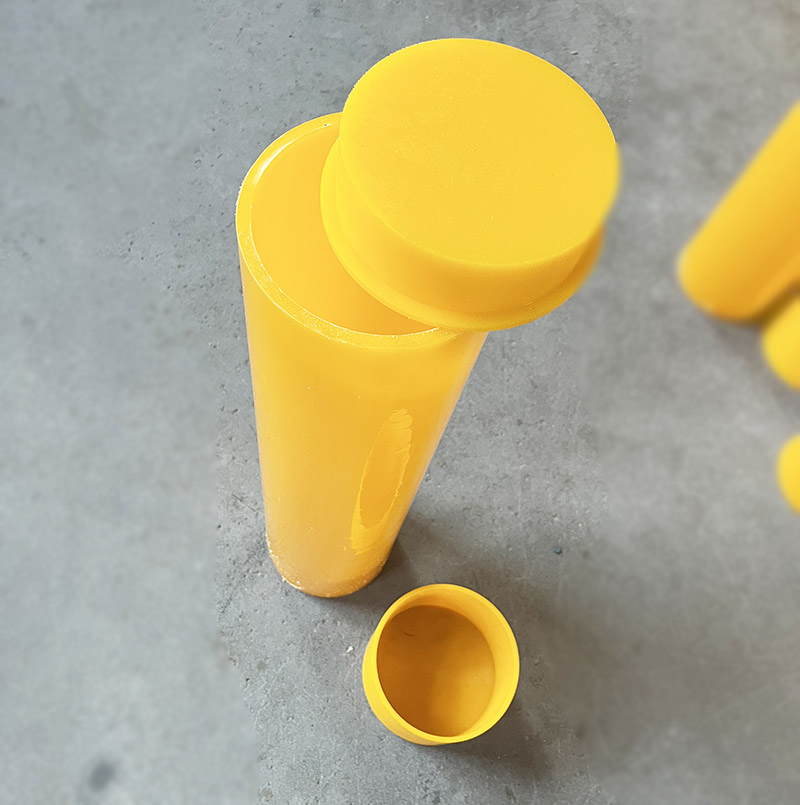
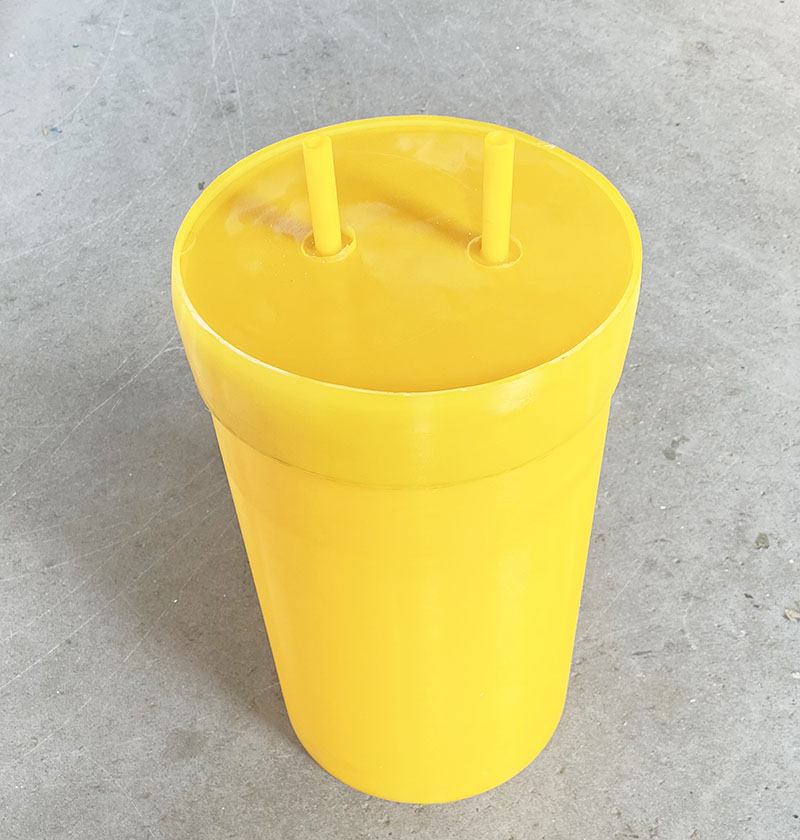
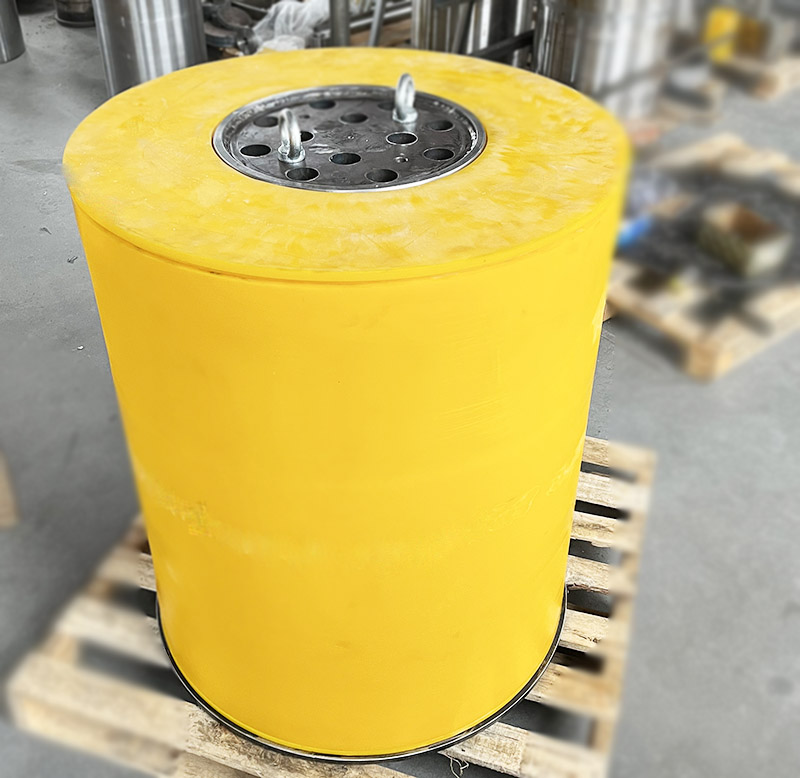