Isostatic pressing
Isostatic pressing can tackle all four limitations in that very large components can be formed, the only limit on achievable aspect ratio arises from the dimensions of the vessel containing the pressing fluid, true three-dimensional geometrical complexity can be achieved and full-density compaction can be delivered. All this is, however, at the expense of significant increases in forming cycle time and some limitations in dimensional tolerance control, compared with die pressing.
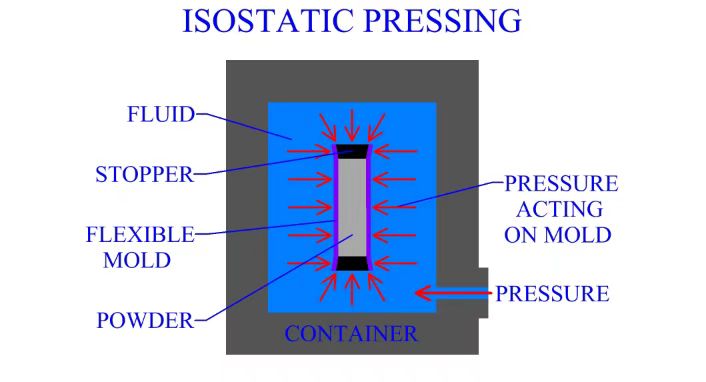
In isostatic pressing, the powder is compacted with a hydrostatic pressure in all directions. The process can be carried out cold or hot.
Cold isostatic pressing (CIP)
In cold isostatic pressing, the powder is contained in a flexible mould, commonly of polyurethane, which is immersed in liquid, usually water, in a pressure vessel, which is pumped to high pressure.
Hot isostatic pressing (HIP)
In hot isostatic pressing, the pressuring medium is a gas, normally argon. The powder is contained in a metallic can, which is subjected to the hydrostatic pressure in the pressure vessel. Full density is achievable by HIP and the process is used for superalloys, high speed steels, titanium etc. where integrity of the materials is a prime consideration.
A significant contributor to HIP costs arises from the canning process. So, there is significant interest in “canless HIP” processing. If the powder can be consolidated to a density above about 92% by a preliminary forming process (e.g. die pressing or CIP), surface connected porosity can be eliminated, gas penetration into the part can be avoided during the subsequent HIP process and full densification can be achieved.
Some Isostatic Pressing bags we made:
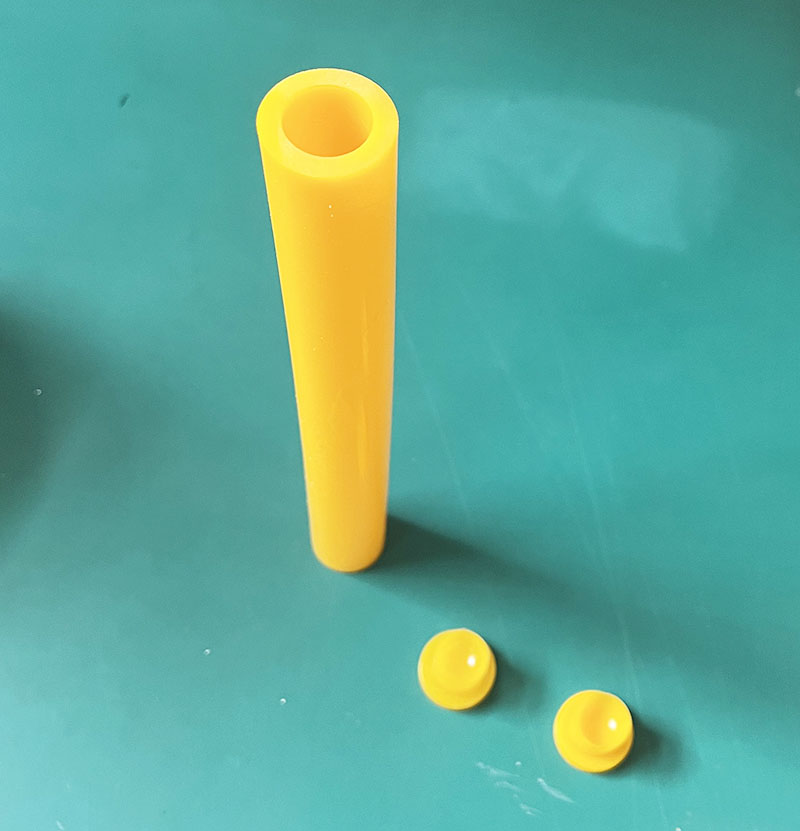
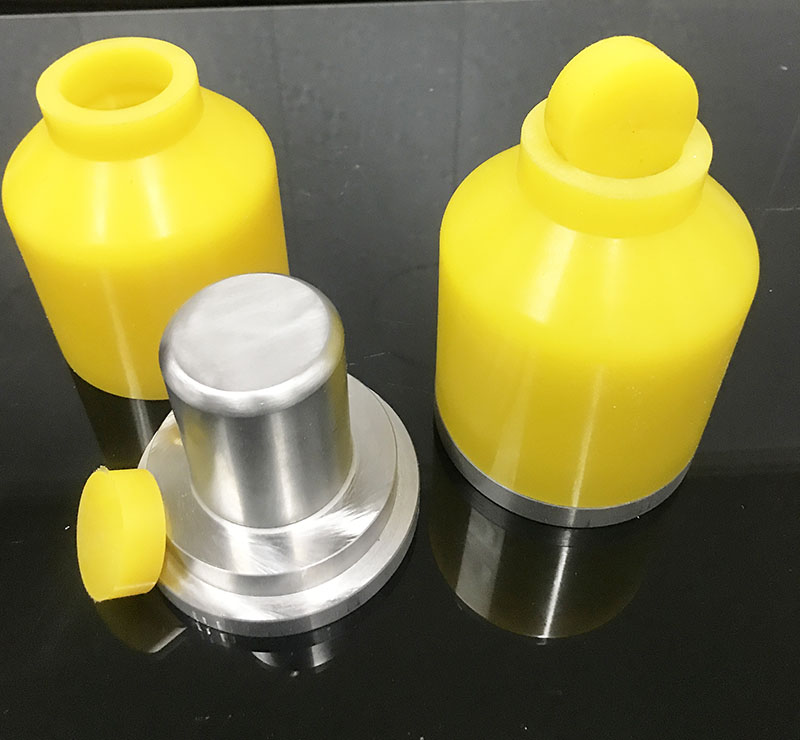
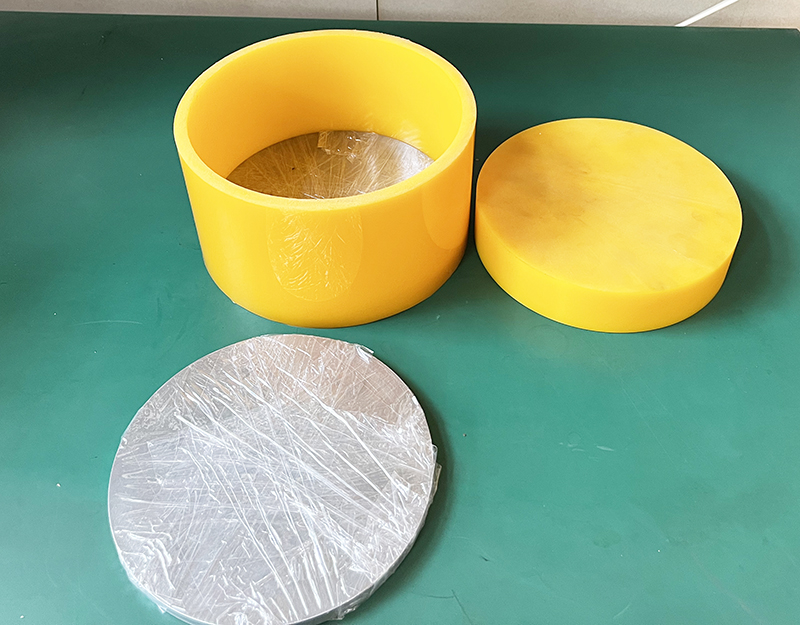
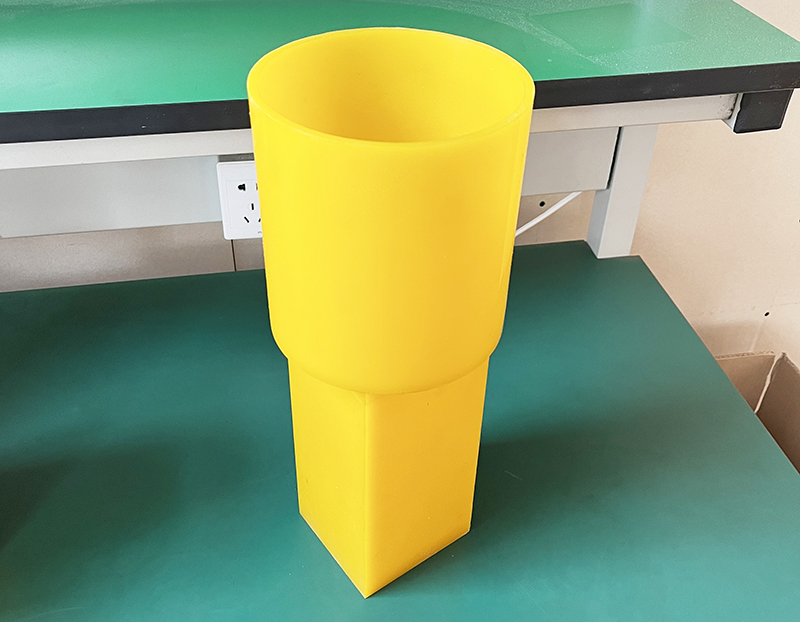
We support all kinds of customization, if you need it, please contact us.
Phone/whatsapp:+86 18234744811
Email:sales@highindustryco.com