Cold Isostatic Pressing Process
The carbon paste or pressed powder loaded into the mold is directly pressed in a high-pressure container to form a green body, which is called isostatic pressing. To produce fine-grained, homogeneous high-density graphite or isotropic graphite using isostatic pressing. The basic principle of isostatic pressing follows Pascal's law in fluid mechanics. Isostatic pressing is to put the powdery material to be pressed into an elastic mold, close the mold mouth and place it in a dry high-pressure container, and then seal the inlet of the high-pressure container tightly. Use an ultra-high pressure pump to inject a pressurized medium (usually transformer oil) into the high-pressure container to uniformly pressurize the mold, and the pressure in the container can rise to 100-600MPa. Open the high-pressure container under normal pressure, take out the mold, and then take out the formed raw and bad from the mold. The isostatic pressing equipment is mainly composed of two parts: a high-pressure container and a high-pressure pump.
Isostatic pressing refers to cold isostatic pressing, which can be divided into two forms according to the different forming processes: wet bag type and dry bag type. The wet bag isostatic pressing technology is to put the granulated ceramic powder or pre-formed body into a deformable rubber casing, and then apply uniform pressure in all directions through the liquid. The rubber cover is removed from the container, which is a discontinuous molding method. The advantages of this technology are that the cost is relatively low, the flexibility of forming products of different shapes is large, and the pressure can reach 500MPa. This technology can be used in the laboratory and in a certain scale of production, and can form parts of moderate complexity. The disadvantage is that the number of products formed in a certain period of time is small. Dry bag isostatic pressing (drybagisostaticpressing) molding technology is to fill the ceramic powder into a flexible pre-formed mold in batches, and then apply isostatic pressing. Since the mold is fixed in the equipment, the molded product is ejected after pressing. The "dry bag" type has a short molding cycle and a long service life of the mold, which is especially convenient for large-scale continuous industrial production. The mold materials used are polyurethane synthetic rubber or silicone rubber. Compared with wet bag isostatic pressing, the dry hair isostatic pressing pressure is lower, generally within 200 MPa. The most familiar ceramic spark plugs are currently formed by dry bag isostatic pressing, and the pressing time is usually only 1~2 s.
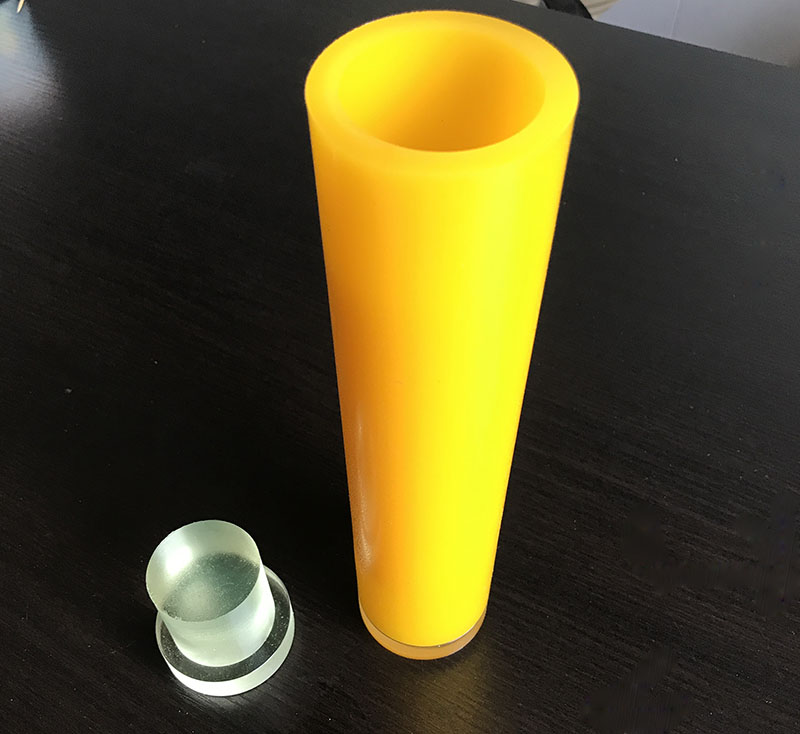
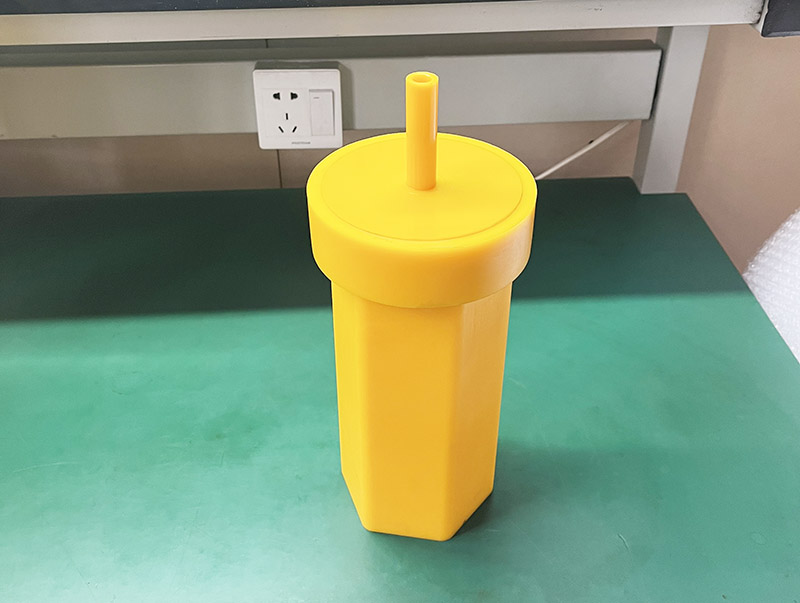
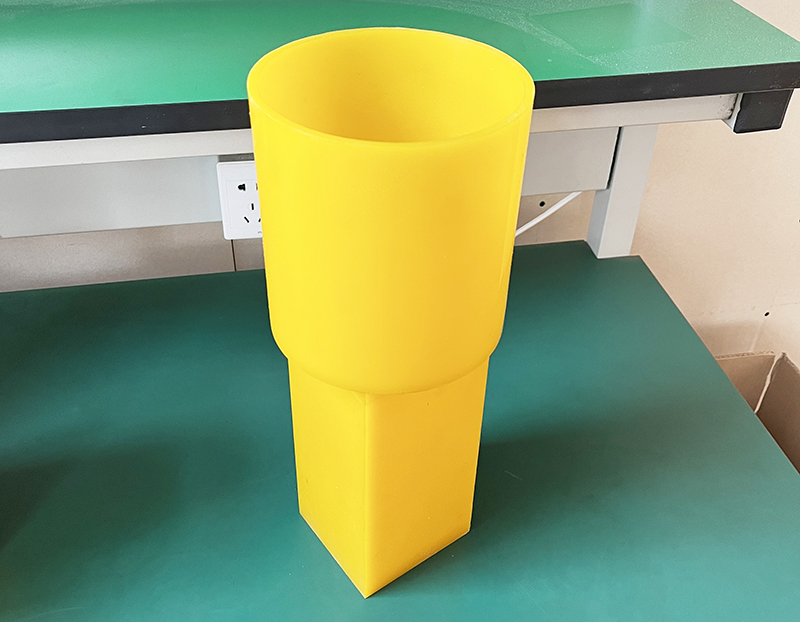
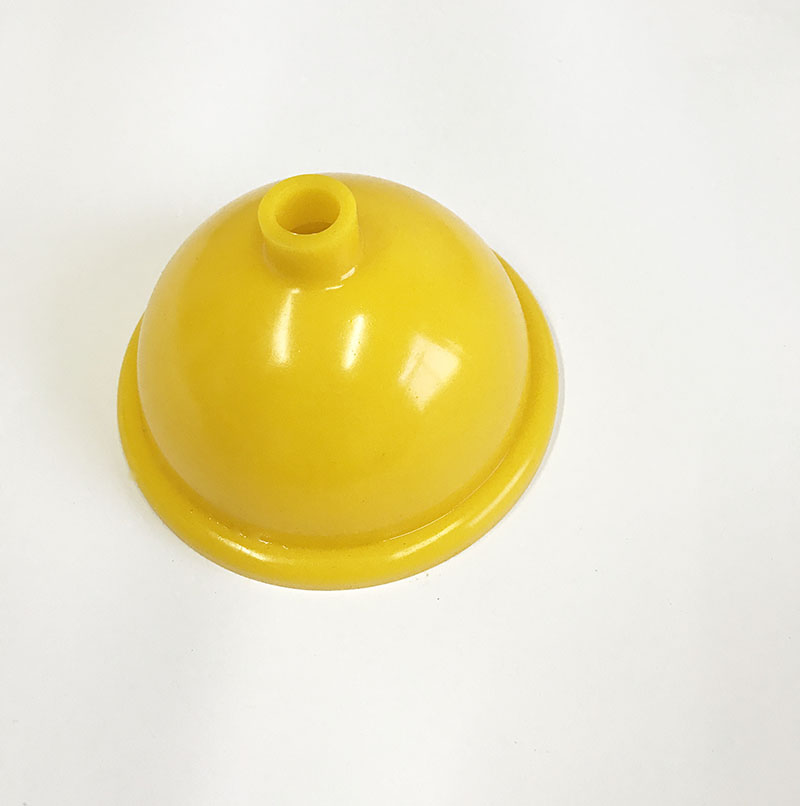