COLD ISOSTATIC PRESSING (CIP) is a materials processing technique in which high pressure is applied to metal powder in a sealed elastomer container shaped for the application.
The powder is converted from a loose aggregate into a partially dense compact that has sufficient green strength to permit careful handling and transfer to the following process operation.
ISOSTATIC PRESSING
The metal powder is compacted uniformly in all directions so that the compact becomes an accurate scale down of the mould uniform density a homogeneous microstructure. For this purpose the powder is sealed in a flexible envelope and the assembly (mould-powder) is immersed in a fluid which is pressurized. There are virtually no residual stresses in the compacted material, because there is no die wall friction.
Benefits of Isostatic Pressing
To get uniform density and compaction.
To make intricate shapes.
To get objects with great dimensional tolerance.
To get homogeneous structure.
Cold Isostaic Process ----- two methods are used :
(a) free mould or "wet bag" process is suited for
1.batch scale production;
2. the mold is filled and sealed outside the pressure vessel.
3. After the mold is introduced in to the pressure vessel, it is completely immersed in the pressure medium, usually water containing lubricating and corrosion-preventive additives;
4. complex parts;
5. research and prototype work;
(b) fixed mould or "dry bag" process, the characteristics
1. envelope is permanently fixed into the pressure vessel,
2. After the elastomeric mold is filled with powder, pressure is applied by introducing pressurized oil between the fixed mold and the vessel wall,
3. only one compact at a time is used,
4. more simple shapes are made and
5. more suited for mass production and faster production rates.
Applications of Cold Isostatic Compaction:
1.Titanium e.g. hydraulic aircraft fittings using Ti powder and Al-V master alloy powder;
2. High-speed tool steels (e.g. cutting tools);
3. Compacts with interior threads;
4. Long hollow cylindrical filters (stainless steel and titanium powder);
5. Large shapes from tungsten powder such as rocket nozzle;
6. Tungsten and molybdenum blooms or slabs for further forging and/or rolling;
Tooling for Isostatic Compacting :
1.Cold isostatic pressing tooling is composed of two parts—the elastomeric mold, or bag, and a mandrel.
2. Elastomeric molds are made of a variety of materials; some are flexible, while others are fairly rigid.
3. An outside fixture to hold the loaded form is required if the mold is exceptionally flexible.
4. A number of factors must be considered in the selection of a mold material.
5. Primarily, the mold material must not interact with either the powder or the pressure medium.
Compare to traditional rubber cold isostatic pressing bags, the polyurethane CIP bags have significant advantages. As a new polymer material, polyurethane products feature smooth surface, wearing-resistant, anti-fatigue, low deformation rate. The surface of pressed products with polyurethane bags is much smoother than that pressed with rubber bags, thus it possesses better looks and less postprocessing is required. It’s an ideal tool for powder material forming by press process, which can help a company reduce cost and increase efficiency.
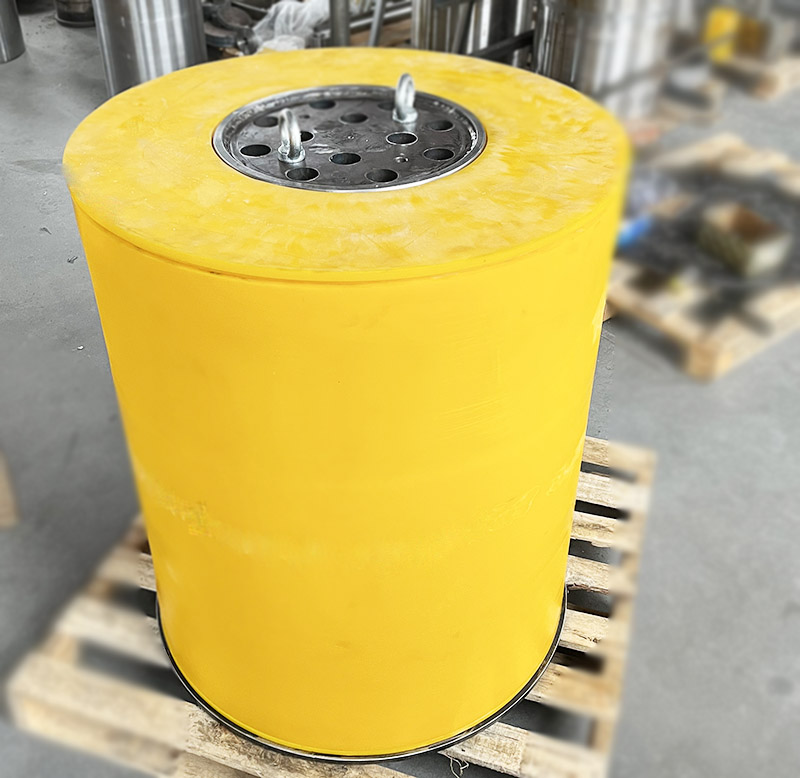
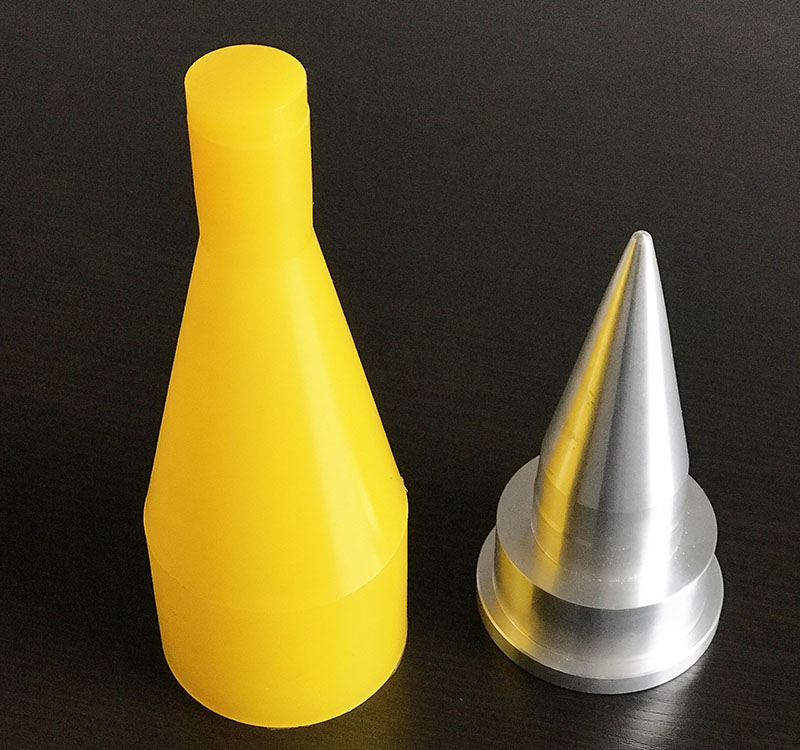
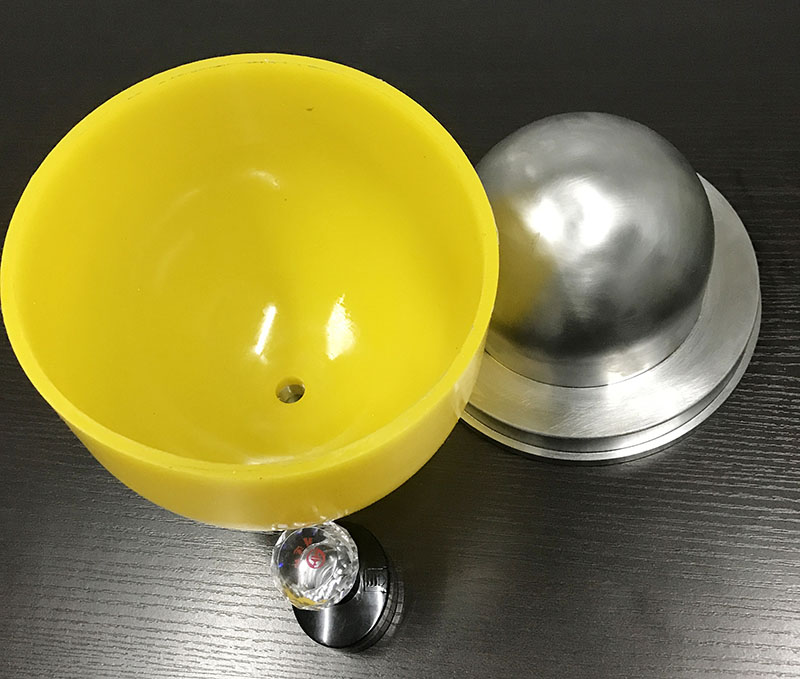
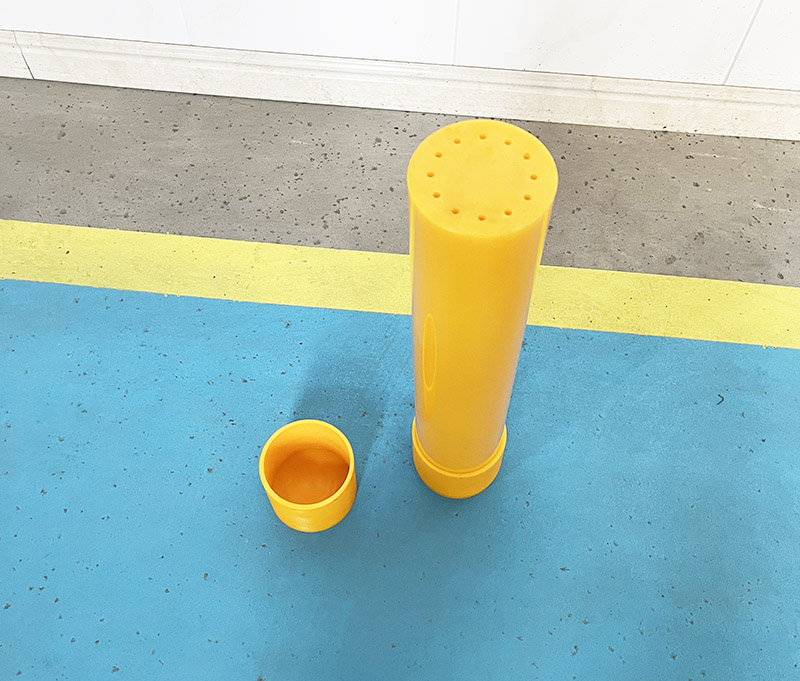
We support all kinds of customization, if you need it, please contact us.
Phone/whatsapp:+86 18234744811
Email:sales@highindustryco.com