Cold isostatic pressing
A special powder forming method in which the powder or powder compact is subjected to uniform and equal pressure in all directions at room temperature. According to whether the elastic mold is fixed on the pressure vessel, it is divided into two types: wet bag type and dry bag type. Unless otherwise specified, cold isostatic pressing generally refers to wet bag cold isostatic pressing.
The typical operation process of wet bag cold isostatic pressing is as follows: put powder in the elastic mold, plug it with a rubber stopper and seal after vibrating; put the sealed elastic mold into the pressure container; seal the container, start the high-pressure oil pump to Final pressure is reached in the vessel. According to Pascal's principle, the powder is subjected to equal pressure in all directions to form. The advantages of the cold isostatic pressing method are: (1) It can press parts with complex shapes that cannot be pressed by molding. For example, aircraft hydraulic titanium joint, ball valve titanium ball used in sea water, Ti-6AI-4V lens holder, etc. As a result, the machining allowance can be greatly reduced and expensive metals can be saved. (2) Pipe fittings, threads or section-by-section reducing rods with a large length-to-diameter ratio can be pressed. Commonly used to suppress stainless steel and titanium filters. (3) Since the powder is uniformly compressed in all directions, a compact with high density, uniform distribution and high strength can be obtained. In the process of pressing hard-to-press powders, high-quality green compacts can be obtained at lower pressures without the addition of forming additives, which can be used as a pre-process for subsequent thermal densification processes (hot rolling, hot extrusion, etc.). (4) It can press laminated parts with different properties, parts with inserts, etc. The disadvantages are: it is difficult to precisely control the size of the green compact, the surface roughness of the green compact is high, and the productivity is lower than that of automatic molding.
In dry bag cold isostatic pressing, the elastic mold (also called dry bag) is permanently fixed in the container. The pressing process is: put the powder into the dry bag; use the upper punch of the press to close the pressure vessel; pump the liquid medium to pressurize the dry bag; after the pressing, the upper punch leaves the container; take out the compact. Because the elastic mold is not taken out of the container during the forming process, the operator is not in contact with the liquid medium, so it is called "dry bag". The main advantages of this method are simple operation, easy automation, high productivity, a single press can reach 500-3800 pieces/h, good labor conditions, and no need for expensive large-scale high-pressure vessels and high-pressure pumps. The main disadvantage is that it is not suitable for the manufacture of large and particularly complex parts. Generally used in the manufacture of balls, tubes, filters, small grinding wheels and spark plugs.
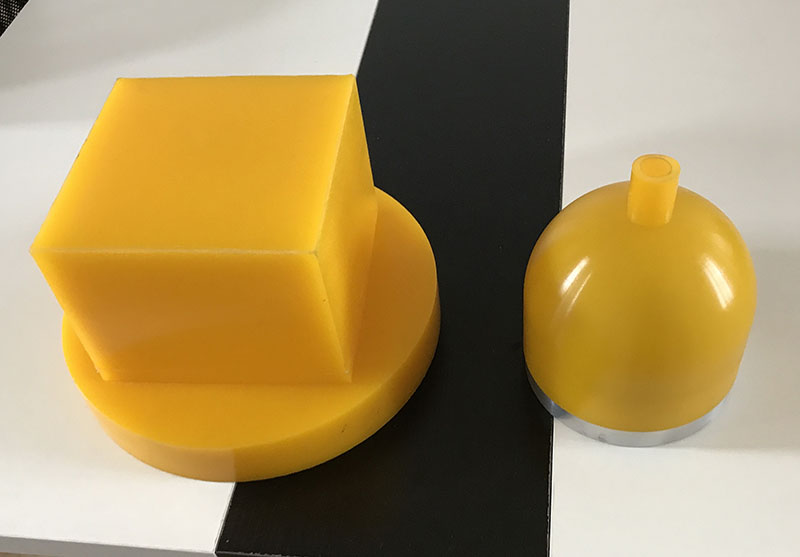
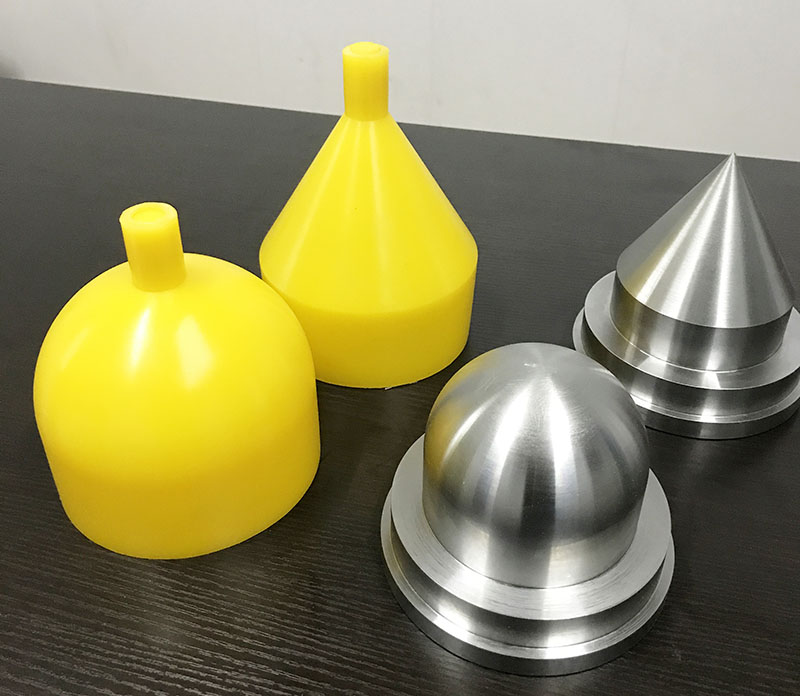
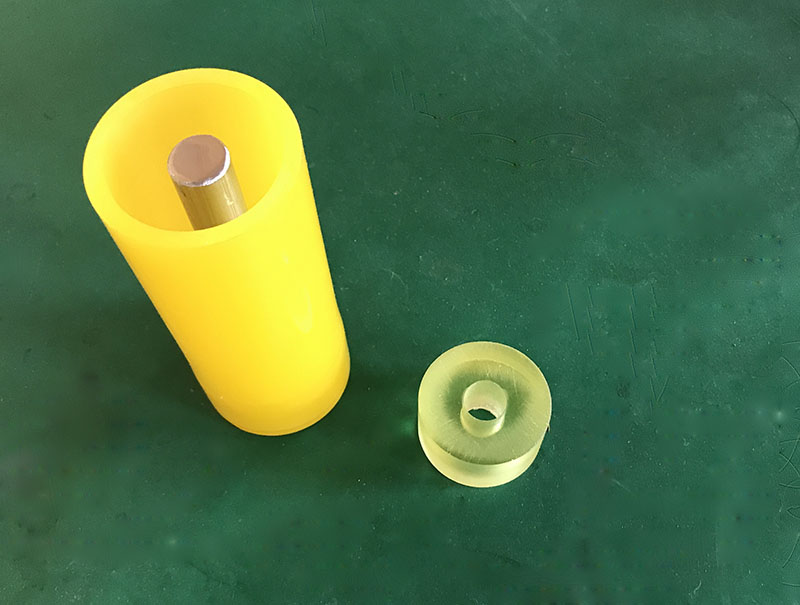
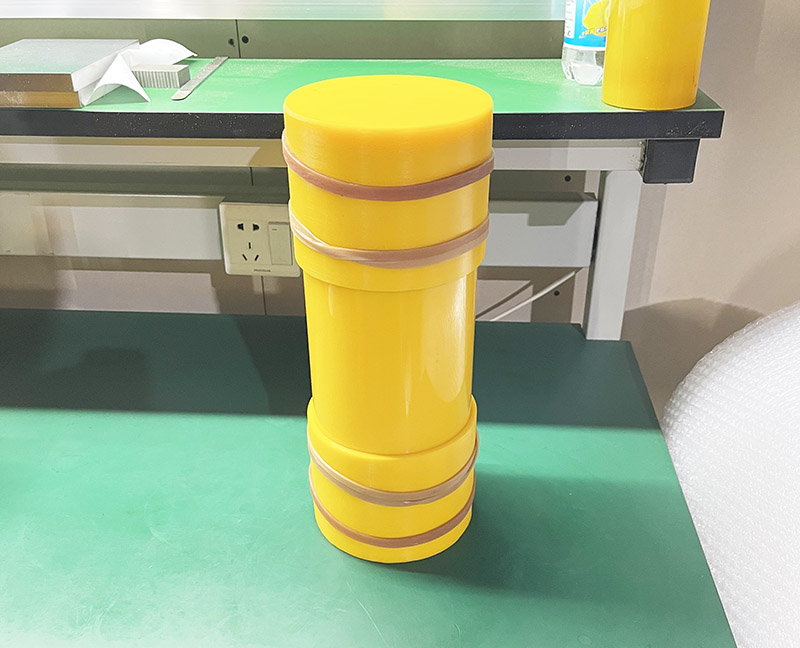
We support all kinds of customization, if you need it, please contact us.
Phone/whatsapp:+86 18234744811
Email:sales@highindustryco.com