Types, Advantages and Applications of the Cold Isostatic Pressing
The cold isostatic pressing (CIP) is based on the effect that a pressure applied to a liquid spreads evenly in all directions (so-called Pascal's principle). Inside the liquid, this leads to a homogeneous pressure distribution, which can be used for shaping ceramic and metallic powders if the powder is encapsulated in an elastic die. Elastic polymers (elastomers) such as polyurethane (PU), polyvinyl chloride (PVC), synthetic or natural rubber have proven successful as materials for the elastic die.
Wet bag process: In the wet bag process, the die is a self-supporting, elastic hollow mold that is filled with the powder outside the cold isostatic press. Optionally, a metallic mandrel can be integrated into the hollow mold for the production of pipes. After filling, the die is closed with an elastic cover plate. In order to protect the interior of the die against the ingress of liquid, the die can also be enveloped with an elastic foil, which is then evacuated and sealed in a liquid-tight manner. The wet bag process is often used in research and development due to its great flexibility with regard to the system parameters (including pressures up to approx. 400 MPa), the component geometries and the number of components per cycle. It is also used in industry for the production of large-volume components (e.g. filter candles) and semi-finished products (e.g. for manufacturing of ceramic insulators) with dimensions up to the meter range. Disadvantages of the wet bag process are the limited dimensional accuracy due to the elastic die and the comparatively long cycle times of several minutes.
Dry bag process: In dry bag pressing, the elastic die is firmly fixed to the recipient. Correspondingly, the mold filling takes place inside the cold isostatic press. The main advantages compared to wet bag pressing are the possibility of full automation, fast cycle times in the range of 10 s - 100 s depending on the component size (increase in cycle time with component size) and better dimensional accuracy. However, it should be noted that in the area of fixing the elastic die to the recipient there are restrictions with regard to the homogeneity of the pressure distribution, which, however, are less relevant for simpler geometries such as plates, cylinders or tubes. Dry die pressing is preferred in industrial production. The best-known application example are spark plug insulators, which are manufactured in a fully automated manner in quantities of millions.
Advantages: The main advantage of cold isostatic pressing is the elimination of friction-related variation in density, such as occurring in the case of uniaxial pressing in rigid molds. Therefore, higher green densities, higher green strengths and more homogeneous structures can be achieved with cold isostatic pressing. For example, press-related textures in the structure can be avoided to a large extent. Furthermore, components with a height / diameter ratio greater than 3: 1 (usually specified as limit for uniaxial pressing) can be produced relatively easily. Because there is no wall friction, it is possible to omit dispense with lubricants during pressing and the required proportion of other pressing additives can be significantly reduced. Furthermore, ceramic feedstocks can be compacted that contain abrasive solid particles that would lead to high tool wear in the case of uniaxial pressing.
Applications of cold isostatic pressing
Cold isostatic pressing is widely used in industry as well as in research and development. One advantage is the great flexibility of the method and the comparatively low costs for the die production. Cold isostatic pressing can be used universally for the compression of oxides, nitrides, borides, graphite, hard metals and other composite materials, as well as for metallic powders. The starting powder should have good compressibility, since the use of high proportions of binder is rather unusual with this method. In general, this method is used to manufacture semi-finished products as well as structural and functional components with moderate geometrical complexity. Specific application examples are spark plug insulators made of alumina, cap insulators, components for lambda sensors, semi-finished products for ceramic insulators and semi-finished products for ceramic balls. Metallic filter cartridges with a length of up to 1.8 m and a diameter of up to 300 mm are also manufactured using this process.
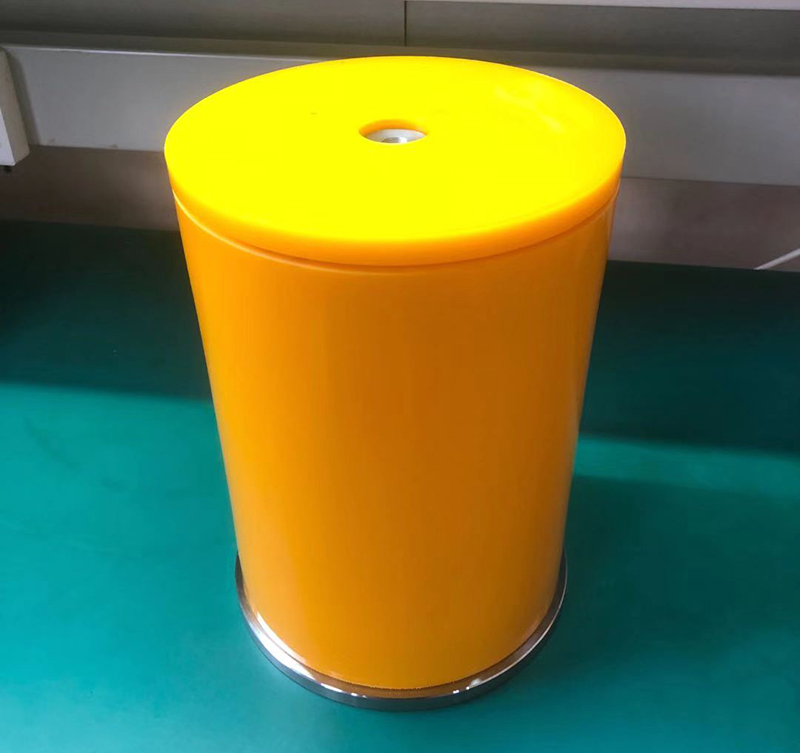
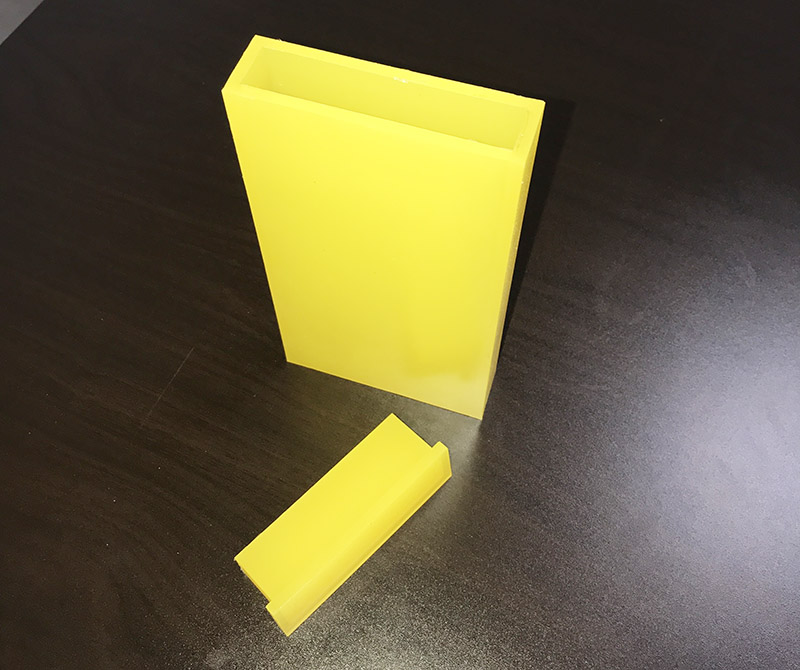
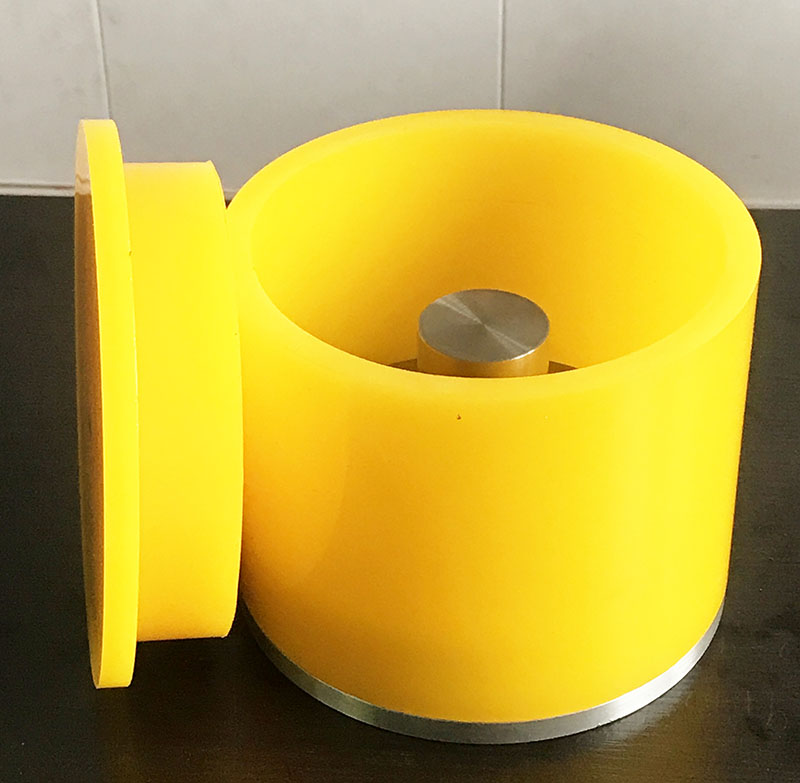
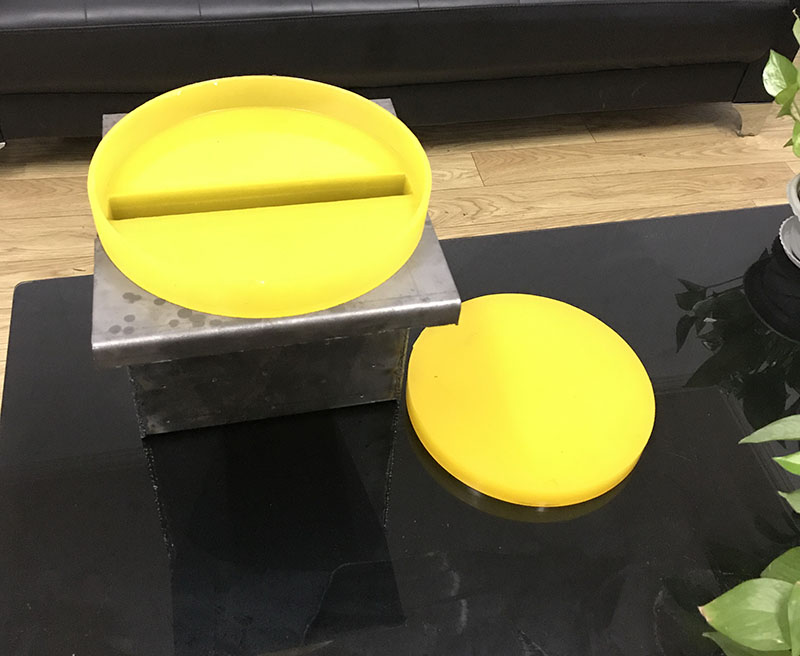
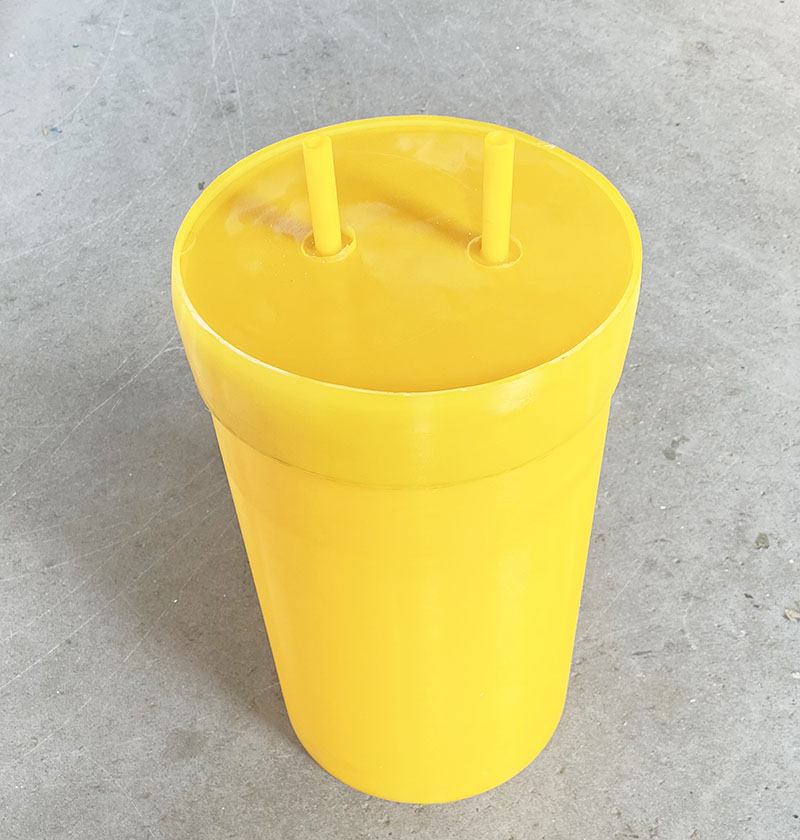