The Types and Characteristics of Isostatic Pressing
Isostatic technology works on the principle of Pascal's law: "The pressure of a medium (liquid or gas) in a closed container can be transferred equally in all different directions." Isostatic pressure technology is more than 70 years away from the origin of the beginning of the application in the powder forming of metallurgical powder; in the last 20 years, isostatic pressure technology has been widely used in high pressure electromagnetic vials, casting ceramics, atomic energy, tool making, plastics, biological drug preparation, ultra-high pressure food sterilization and graphite, ceramics, permanent magnets, food preservation, high-performance materials, military industry and other fields.
Characteristics of isostatic pressure technology types are as follows.
Cold isostatic pressing (Cold isostatic pressing, CIP for short)
At room temperature, it generally uses rubber or plastic as the material for the shell shape and liquid as the pressure medium. It is used in the molding of powder materials to prepare raw materials for further sintering, forging or hot isostatic pressing. The general working pressure is 100~630 MPa.
Hot Isostatic Pressing (HIP for short)
HIP is a process skill that enables the use of inferior isostatic pressed materials at high temperatures and high pressures. It is not only used for curing powders. Together with the completion of the traditional processes of powder metallurgy, casting and sintering, it is also used for the dispersed bonding of parts, the elimination of casting flaws and the production of parts with complex shapes. In hot isostatic pressing, inert gases such as argon and ammonia are generally used as pressure transfer media, and the covering material is generally metal or glass. The operating temperature is generally 1000 to 2200°C, and the working pressure is generally 100 to 200 MPa.
As a molding process, compared with conventional molding skills, isostatic pressing skills have the following characteristics.
1. The density of isostatically molded products is very high, generally 5 to 15 times higher than that of unidirectional and bidirectional molding products. The relative density of hot isostatic pressed products can reach 998% to 99.09%.
2. The density of the briquettes is uniform. In compression molding, the density distribution of the raw briquettes is not uniform, whether it is one-way or two-way constraint. When restraining products with complex shapes, this density variation can generally reach more than 10%. This is due to the frictional resistance between the powder and the steel mold. The isostatic fluid transfer pressure is the same in all directions. The compacting of shell and powder is basically the same. There is no relative motion between the powder, and the frictional resistance between the powder is very small, and the pressure drops slightly. The density drop gradient is generally only less than 1%. Thus, it can be regarded as a null value. The stacking density is homogeneous.
3. Because the density is uniform. As a result, the height to width ratio of the production can be unconstrained, which is conducive to the manufacture of rod, tube, thin and long products.
4. Isostatic pressing process generally does not require the addition of lubricants to the powder, which not only reduces product contamination, but also simplifies the manufacturing process.
5. Isostatic pressing products have very good performance, short production cycle and a wide range of use. The disadvantage of the isostatic pressing process is that the power of the process is relatively cheap and expensive equipment
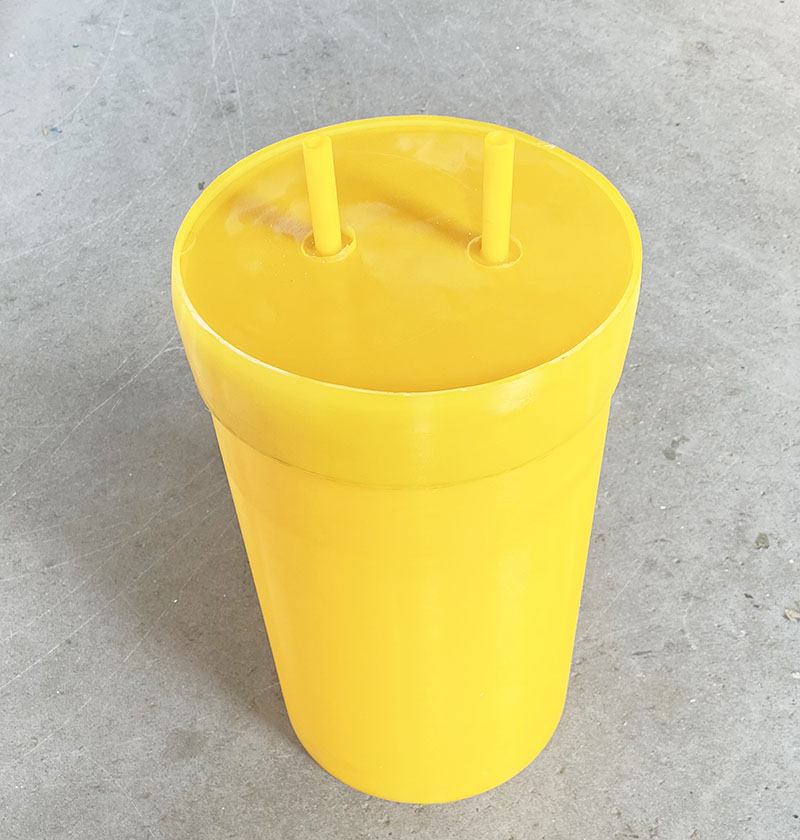
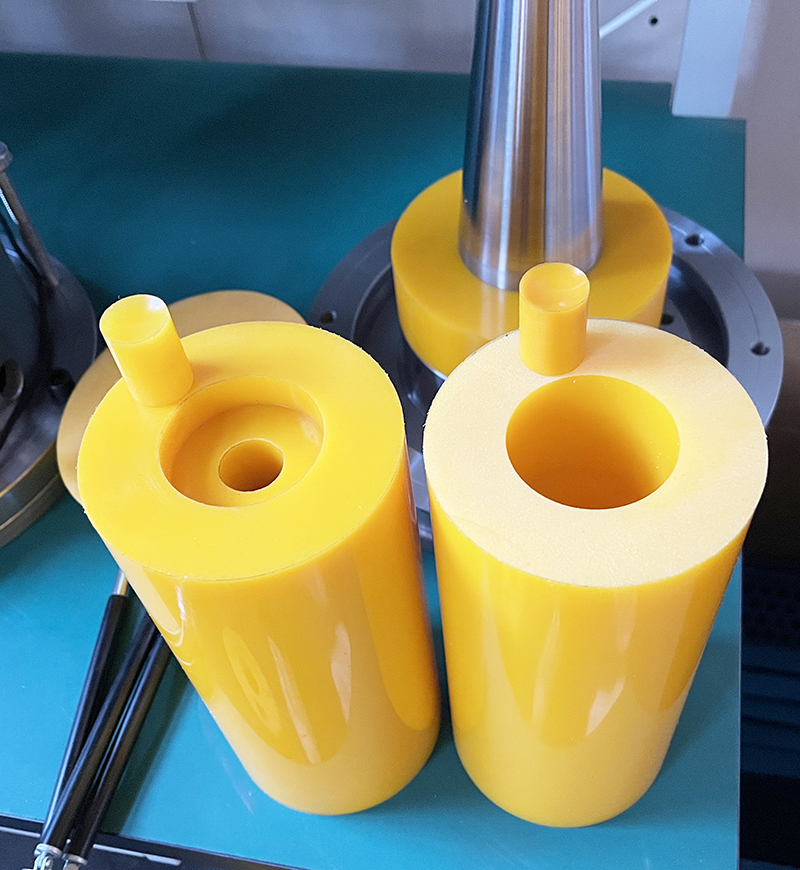
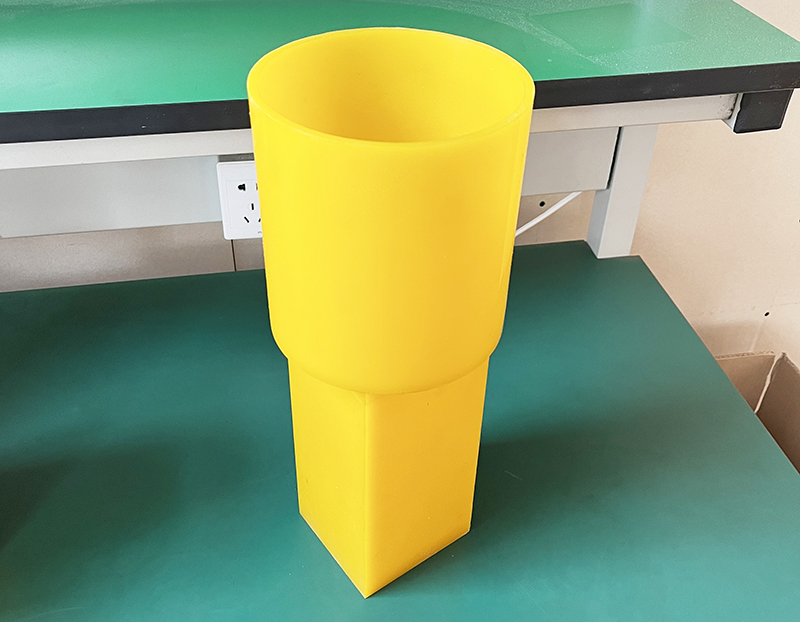
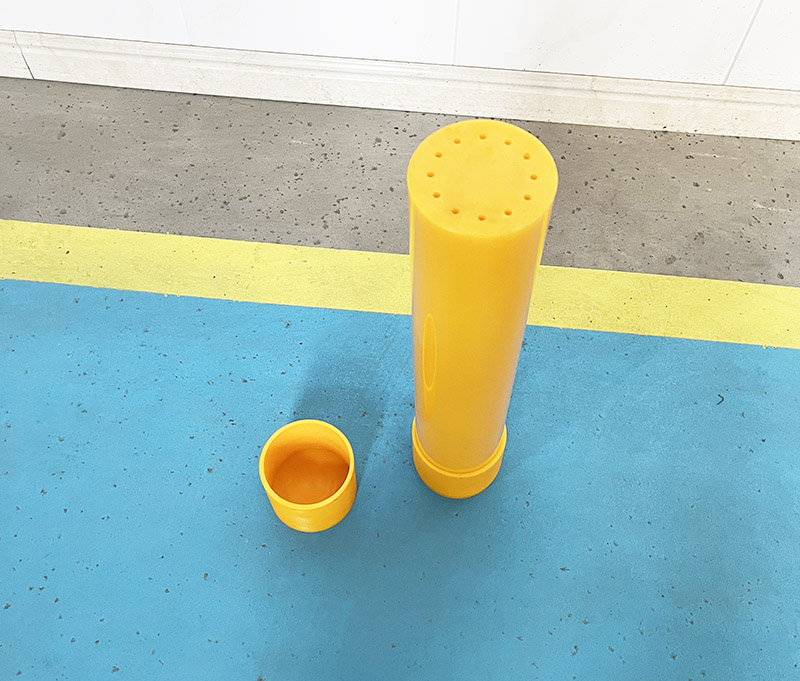