Isostatic Pressing Process
The isostatic pressing process was pioneered in the mid-1950s and has steadily grown from a research curiosity to a viable production tool. Many industries apply this technique for consolidation of powders or defect healing of castings. The process is used for a range of materials, including ceramics, metals, composites, plastics, and carbon.
Isostatic pressing applies a uniform, equal force over the entire product, regardless of shape or size. It thus offers unique benefits for ceramic and refractory applications. The ability to form product shapes to precise tolerances (reducing costly machining) has been a major driving force for its commercial development.
There are three basic types of isostatic pressing. Cold isostatic pressing (CIP) is applied to consolidate ceramic or refractory powders loaded into elastomeric bags. Warm isostatic pressing (WIP) differs from CIP only in that shapes are pressed at warm temperature to about 100°C. Hot isostatic pressing (HIP) involves both temperature and pressure applied simultaneously to obtain fully dense parts (to 100% theoretical density), and is used mainly for engineered ceramics requiring optimum properties for high-performance applications.
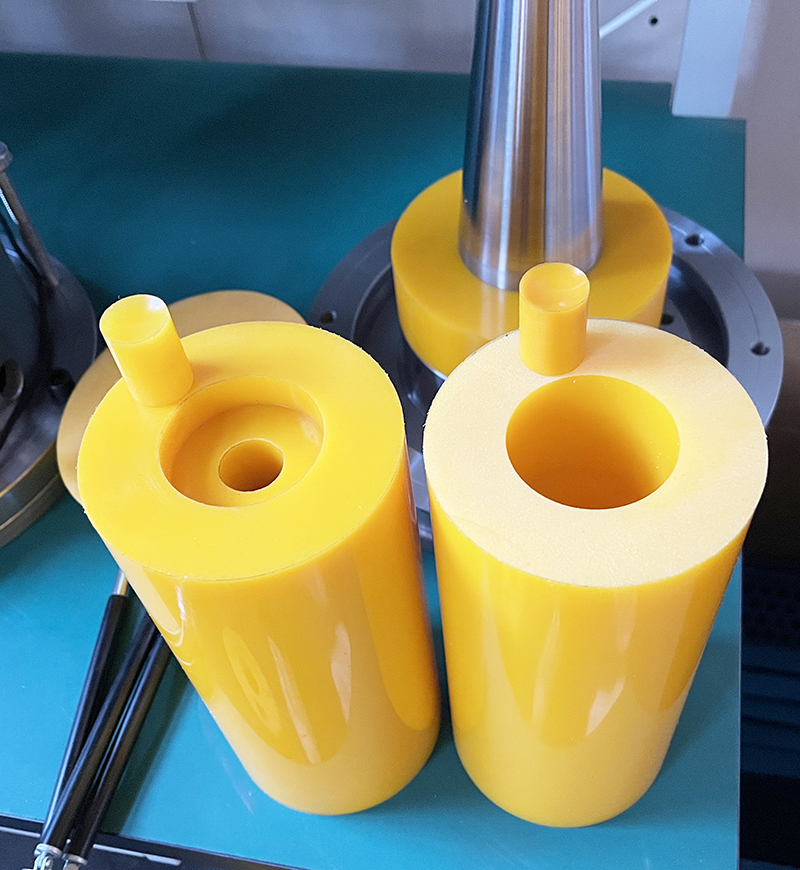
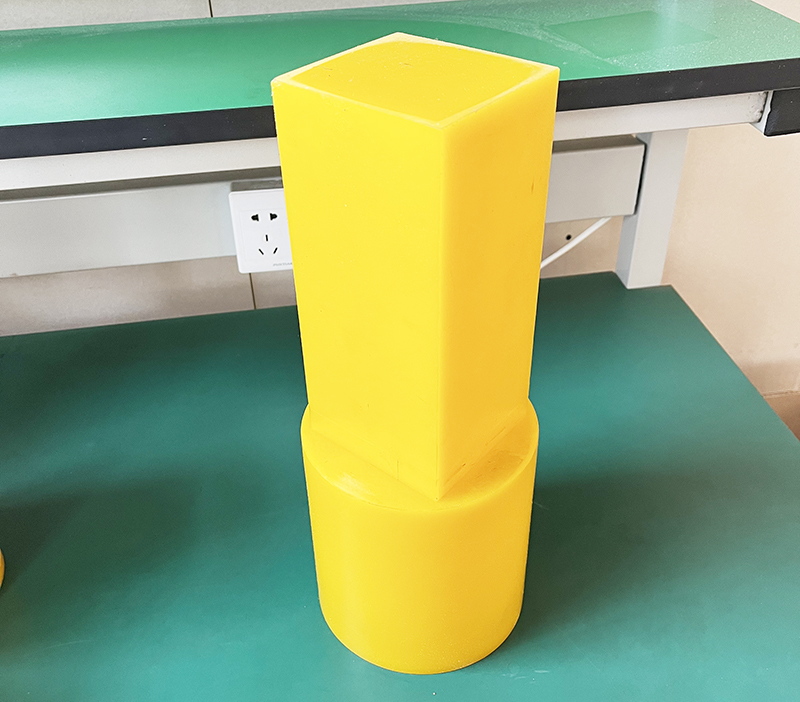
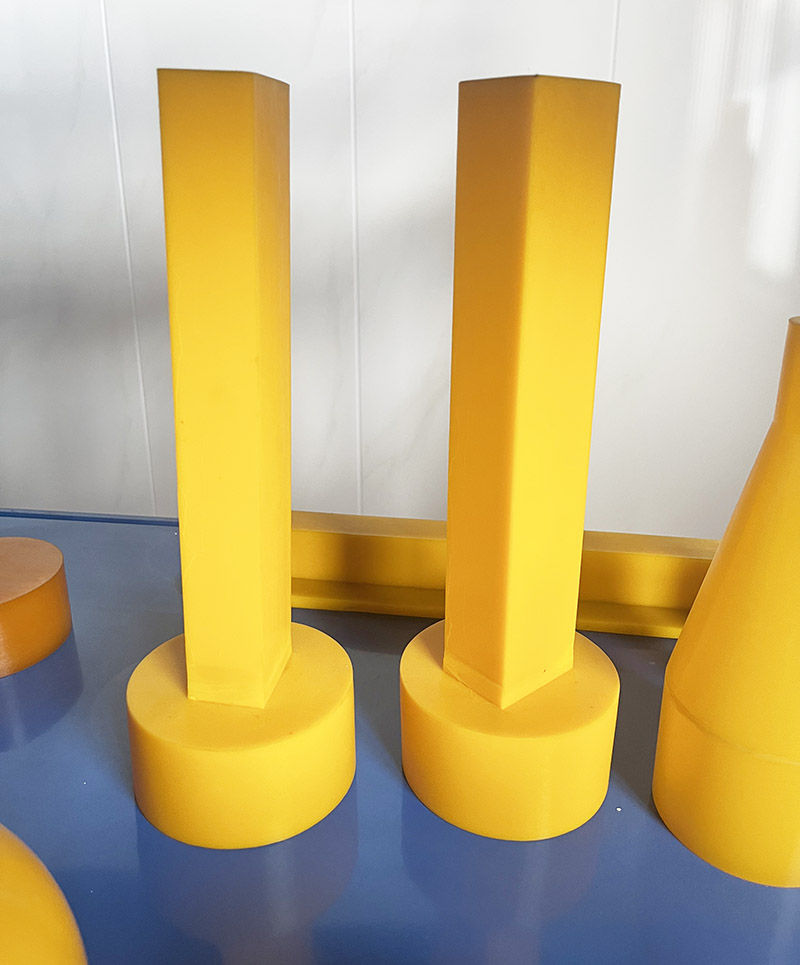
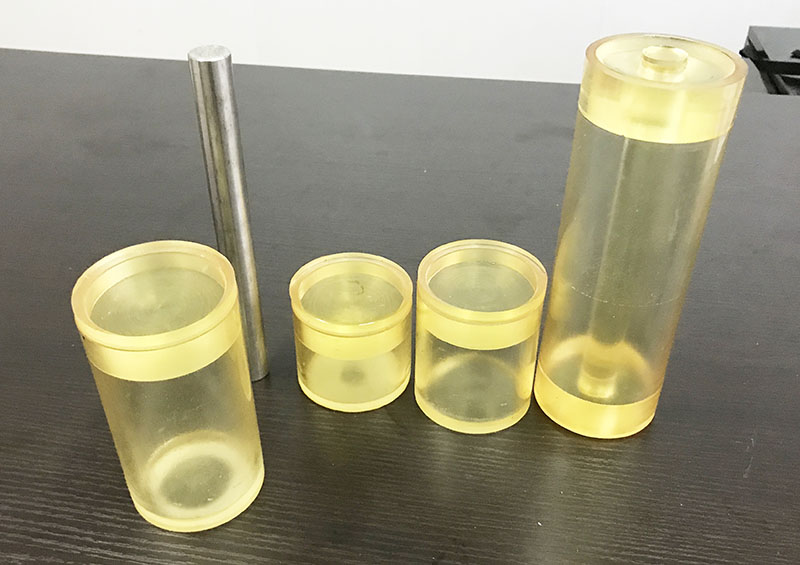