Isostatic Pressing
A feature of conventional pressing is that pressure is applied uniaxially. This imposes limitations on part geometry because metallic powders do not readily flow in directions perpendicular to the applied pressure. Uniaxial pressing also leads to density variations in the compact after pressing. In isostatic pressing, the pressure is applied from all directions.
against the powders that are contained in a flexible mold; hydraulic pressure is used to achieve compaction. Isostatic pressing takes two alternative forms:
(1) cold isostatic pressing
(2) hot isostatic pressing.
Cold isostatic pressing (CIP)
involves compaction performed at room temperature.
The mold, made of rubber or other elastomer material, is oversized to compensate for shrinkage. Water or oil is used to provide the hydrostatic pressure against the mold inside the chamber. The picture illustrates the processing sequence in cold isostatic pressing. Advantages of CIP include more uniform density, less expensive tooling, and greater applicability to shorter production runs. Good dimensional accuracy is difficult to achieve in isostatic pressing because of the flexible mold. Consequently, subsequent finish shaping operations are often required to obtain the required dimensions, either before or after sintering.
Hot isostatic pressing(HIP)
Hot isostatic pressing is carried out at high temperatures and pressures, using a gas such as argon or helium as the compression medium. The mold in which the powders are contained is made of sheet metal to withstand the high temperatures. HIP accomplishes pressing and sintering in one step. Despite this apparent advantage, it is a relatively expensive process and its applications seem to be concentrated in the aerospace industry. PM parts made by HIP are characterized by high density (porosity near zero), thorough interparticle bonding, and good mechanical strength.
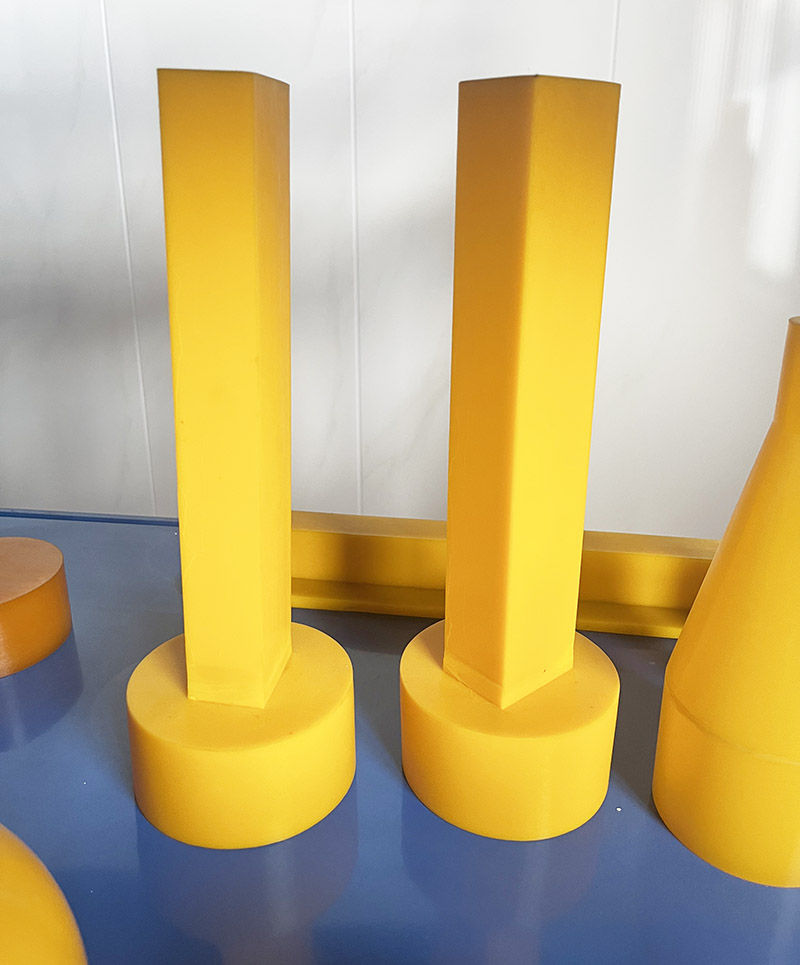
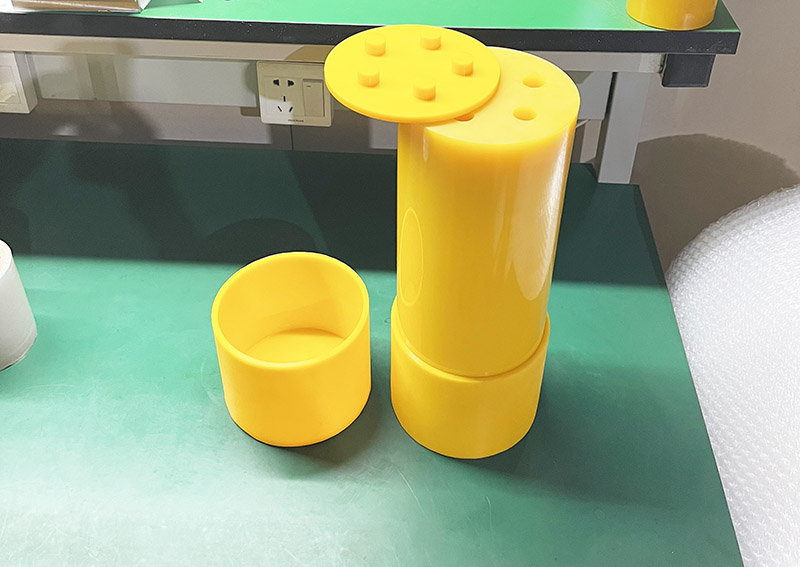
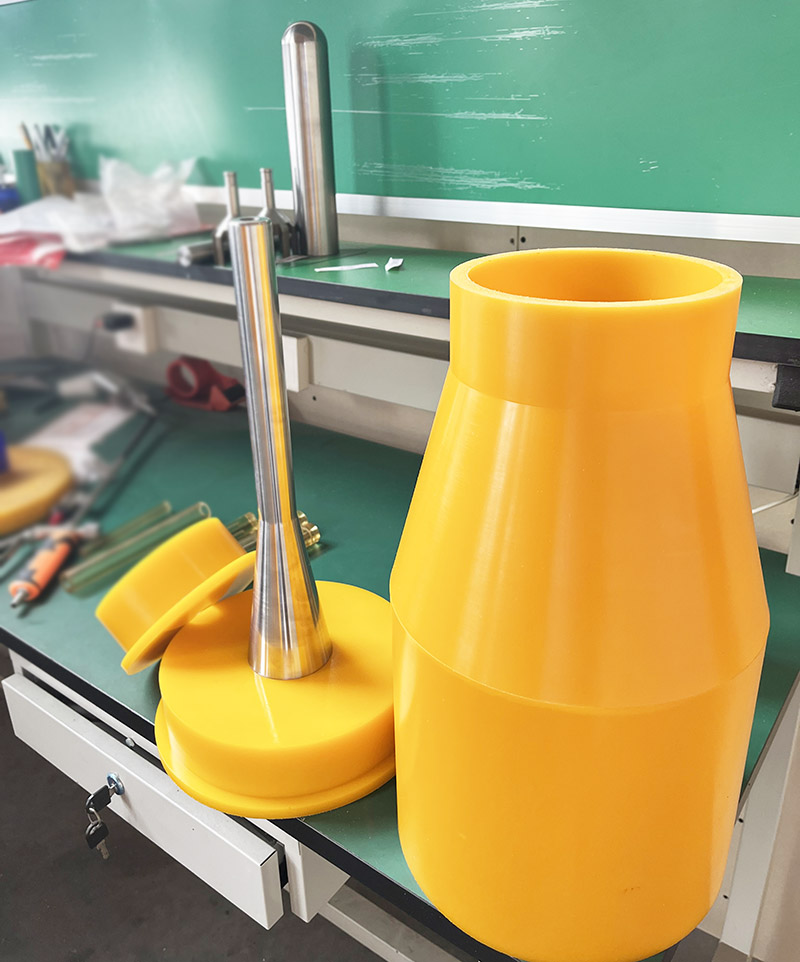
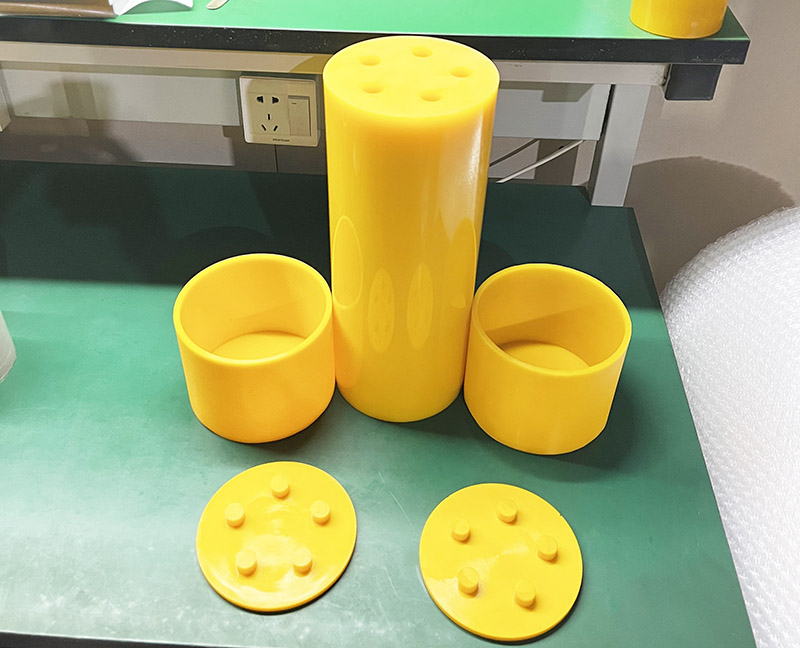