Cold Isostatic Pressing and Hot Isostatic Pressing
Isostatic Pressing
Isostatic pressing is a molding method that takes advantage of the incompressibility and uniform pressure transfer properties of liquid media. The liquid medium can transmit the pressure uniformly, so the compacted body has high density and uniformity. This method has been used in the production of ceramic industry to form oxide ceramics, high-voltage electric ceramics, nitride ceramics and graphite products. Isostatic pressing operating at room temperature is called ambient (cold) isostatic pressing. In recent years, both the ceramic and powder metallurgy industries have adopted HIP operation.
Cold Isostatic Pressing
Through this process, the mold is placed into a pressure chamber and filled with a room-temperature liquid before the press applies the pressure from all sides, condensing the metal powder. As a result, the powder particles mechanically bond to each other, creating a solid green body. Finally, the liquid is removed and the container expands to its original form so that the product can be retrieved.
There are two types of presses used for cold dry bag isostatic pressing — monostatic isostatic presses with single-cavity structures and densomatic isostatic presses with multi-cavity designs.
Hot Isostatic Pressing
High temperature and pressure are applied simultaneously to pre-cast or sintered components. The addition of argon gas to the furnace helps to apply isostatic pressure to the component/s. The pressure and heat help to fill any pores on the surface of the component, thus optimising material properties and density.
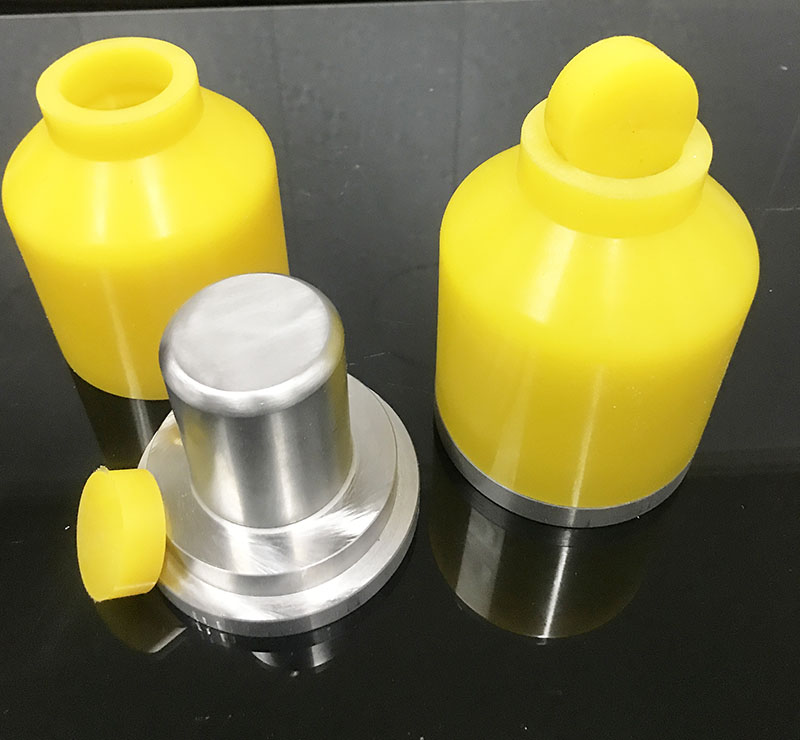
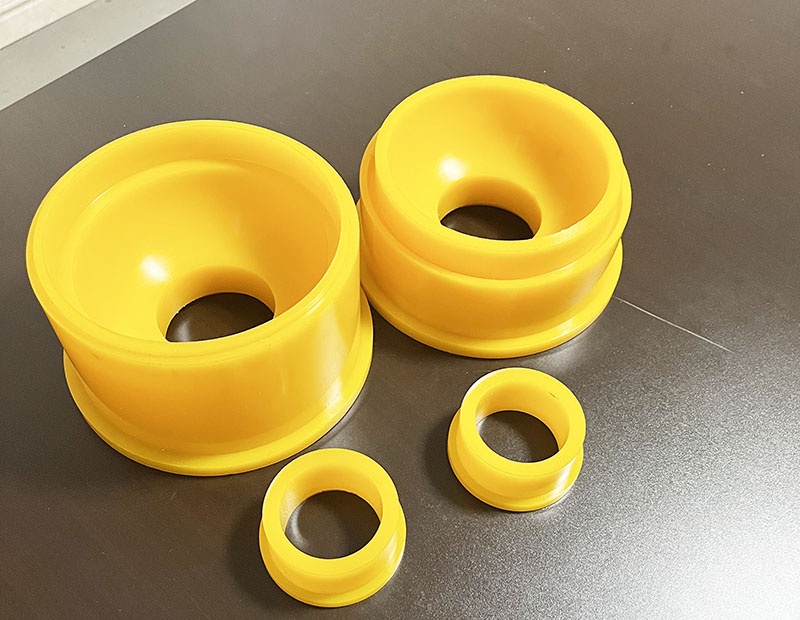
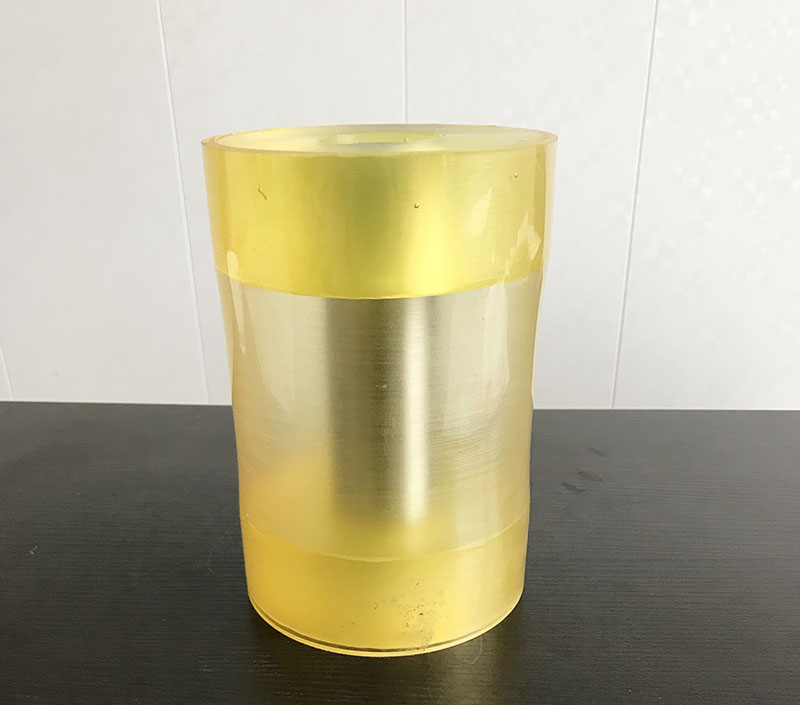
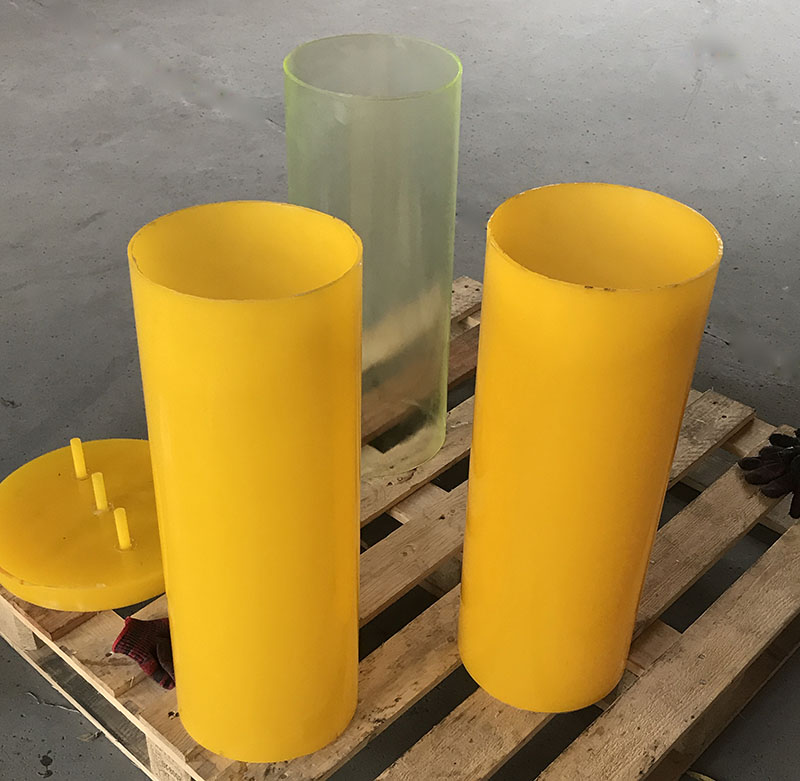