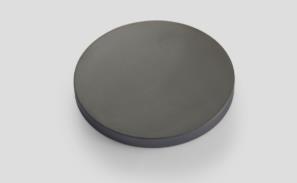
Forming method of ITO target
Categories: Cold isostatic pressing bags
Application: Forming method of ITO target
InquiryMain description:
Forming method of ITO target
Forming method of ITO target
Forming method of ITO target
1. Spraying method
The spraying method is to use high-pressure gas (N2, H2, mixed gas or air) to carry powder particles through a scaling tube to generate a supersonic two-phase flow, hit the substrate in a solid state, and deposit on the surface of the bound backing plate through large plastic flow deformation. A coating is formed, and the coating is thickened layer by layer to obtain a ceramic target. In recent years, plasma spraying, arc spraying, supersonic flame spraying, cold spraying and other spraying forming technologies have been derived from the basic spraying method. breakthrough.
2. Cold isostatic pressing
The cold isostatic pressing method is to put the pre-formed green body into a rubber casing and immerse it in a high-pressure liquid to make it withstand isotropic pressure, so as to strengthen the density of the green body. Cold isostatic pressing is only to obtain a green body with the highest possible density, which makes the sintering and densification of the green body easier.
Cold isostatic pressing can suppress large-sized targets, and is currently the preferred molding method for most companies. Studies have shown that cold isostatic pressing can produce high-quality green bodies that meet the needs of ceramic targets. However, when cold isostatic pressing is used to form super-sized green bodies, it will lead to expensive equipment investment due to the limitation of the size of the chamber. Moreover, when the green body is thin and the size is large, there is a deformation problem. At the same time, when pressing the green body of different sizes, it is necessary to prepare pre-pressing molds of different specifications, and the cost of the mold is relatively high.
3. Hot isostatic pressing
The hot isostatic pressing method is to put the powder or pre-pressed green body into the package, then vacuum and weld the package, and put it into a high-pressure container, so that the powder is sintered, formed and sintered under high temperature and equal pressure. simultaneously. In the development of ITO targets, it was difficult to obtain high-density and large-sized materials with the hot isostatic pressing technology adopted in the early days. The disadvantages of low oxygen loss rate, high oxygen loss rate, expensive equipment and high cost of this method make the hot isostatic pressing method no longer have a competitive advantage in the preparation of ITO ceramic targets, and subsequent research and industrialization are gradually diluted by the industry. , but it is still more suitable for ceramic targets that require oxygen deficiency.
4. Wet forming
Wet molding is to prepare the oxide powder into slurry, and then realize the green body of fixed shape through self-solidification, water absorption or filter press, etc., and obtain high-density green body after drying. Wet forming can not only realize the function of cold isostatic pressing, but also make up for the deficiency of cold isostatic pressing. Wet molding of ceramic targets includes grouting, colloidal molding, and direct solidification molding.
Compare to traditional rubber cold isostatic pressing bags, the polyurethane CIP bags have significant advantages. As a new polymer material, polyurethane products feature smooth surface, wearing-resistant, anti-fatigue, low deformation rate. The surface of pressed products with polyurethane bags is much smoother than that pressed with rubber bags, thus it possesses better looks and less postprocessing is required. It’s an ideal tool for powder material forming by press process, which can help a company reduce cost and increase efficiency.
Durability and deformation rate are factors that users care most. A long working life of pressing bag can reduce cost and increase production efficiency, while low deformation rate of the bag will enhance precision and yield of products. By close cooperation with material suppliers and great mass of manufacturers of carbide, ceramics and graphite products, we accumulated a lot of experience in this industry and become a well-know supplier of CIP bags.