Definition, Molding method and Application of ITO Sputtering Target
Definition of ITO Sputtering Target
The full name of ITO is indium tin oxide, a composition of indium, tin, and oxygen with different proportions. The substance of ITO and ITO sputtering target is the same, the latter of which is actually a black-gray ceramic semiconductor formed by mixing indium oxide and tin oxide powder in a certain ratio.
Vacuum hot pressing
Vacuum hot pressing densifies the ITO powder by utilizing thermal energy and mechanical energy, and it can produce a high-density ITO ceramic target with a density of 91% to 96%. This method can easily obtain an ITO target that is close to the expected density and whose porosity is close to zero. However, limited by the equipment and the mold size, vacuum hot pressing is less advantageous in preparing a large-sized sputtering target.
Hot isostatic pressing
Hot isostatic pressing (HIP) prepares ITO sputtering target by sintering under pressure or pressing at high temperatures. Similarly with vacuum hot pressing, HIP can obtain a product with high density (almost a theoretical density) and excellent physical and mechanical properties in the heated and pressurized state. But it is also limited by the pressure of the equipment and the size of the cylinder.
Room temperature sintering
Room temperature sintering prepares a high-density target preform by slurry casting or pre-pressing first and then sinters it under a certain atmosphere and temperature to obtain the ITO target. Its biggest advantage over others is the ability to produce large size sputtering targets. But the purity of the target made by this method is lower, compared to other sintering methods.
Cold isostatic pressing
Cold isostatic pressing (CIP) uses rubber or plastic as a mold covering material at a normal temperature and uses a liquid as a pressure medium to transfer ultra-high pressure. CIP can also prepare ITO sputtering targets of a larger size. And it is cheap, which is suitable for mass production. But CIP requires the materials sintered at a high temperature of 1500~1600 °C in a 0.1~0.9 MPa pure oxygen environment, which has a higher risk.
Application of ITO Sputtering Target
ITO sputtering target, along with its derivatives such as ITO film and ITO glass, has many applications in various industries. ITO target is often used to make transparent conductive coatings for displays such as liquid crystal displays (LCD), flat panel displays, plasma displays, and touch panels. ITO thin film is used in organic light-emitting diodes, solar cells, and antistatic coatings. Apart from the electronics industry, ITO target is also used for various optical coatings, most notably infrared-reflecting coatings and sodium vapor lamp glasses for automotive.

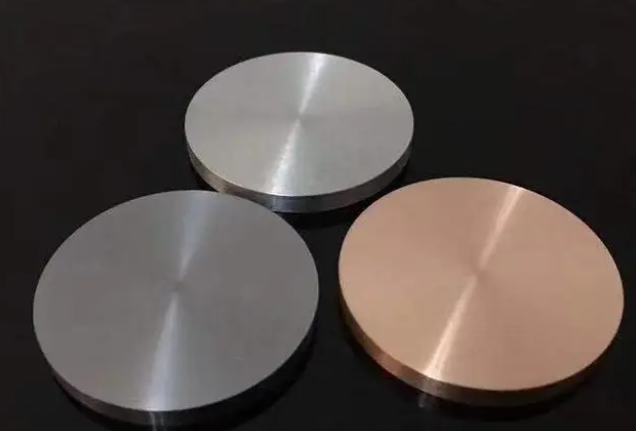
Compare to traditional rubber cold isostatic pressing bags, the polyurethane CIP bags have significant advantages. As a new polymer material, polyurethane products feature smooth surface, wearing-resistant, anti-fatigue, low deformation rate. The surface of pressed products with polyurethane bags is much smoother than that pressed with rubber bags, thus it possesses better looks and less postprocessing is required. It’s an ideal tool for powder material forming by press process, which can help a company reduce cost and increase efficiency.
Durability and deformation rate are factors that users care most. A long working life of pressing bag can reduce cost and increase production efficiency, while low deformation rate of the bag will enhance precision and yield of products. By close cooperation with material suppliers and great mass of manufacturers of carbide, ceramics and graphite products, we accumulated a lot of experience in this industry and become a well-know supplier of CIP bags.
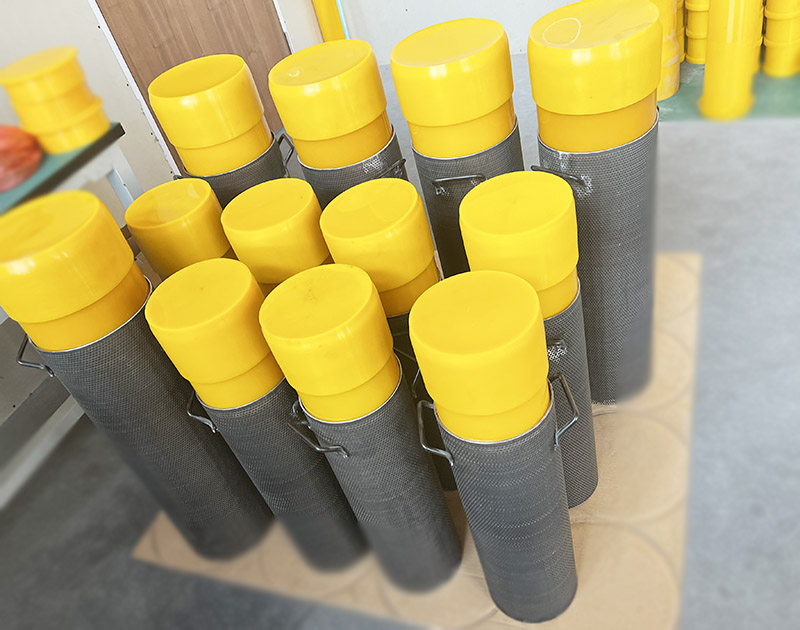
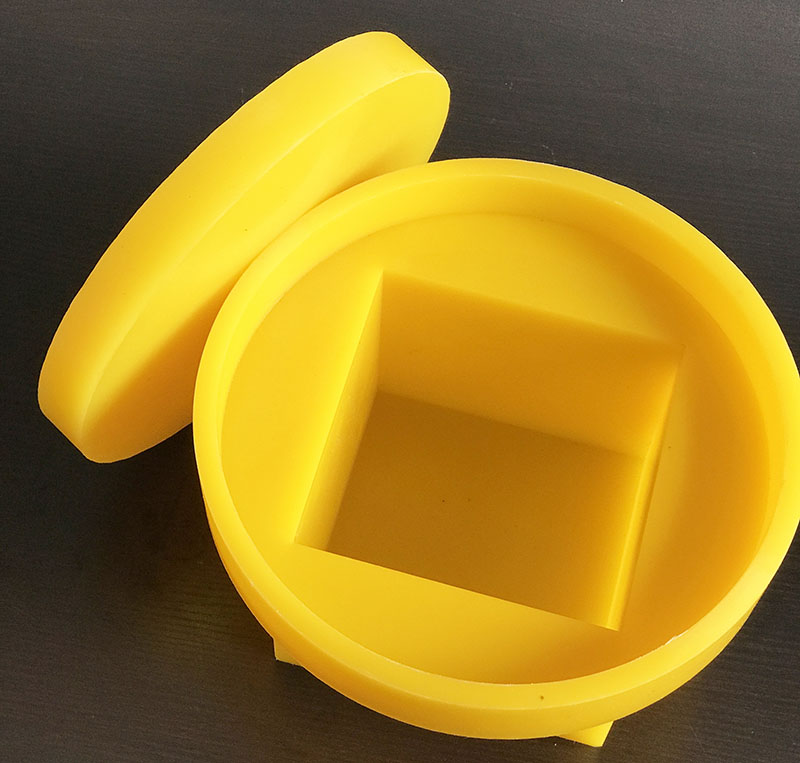
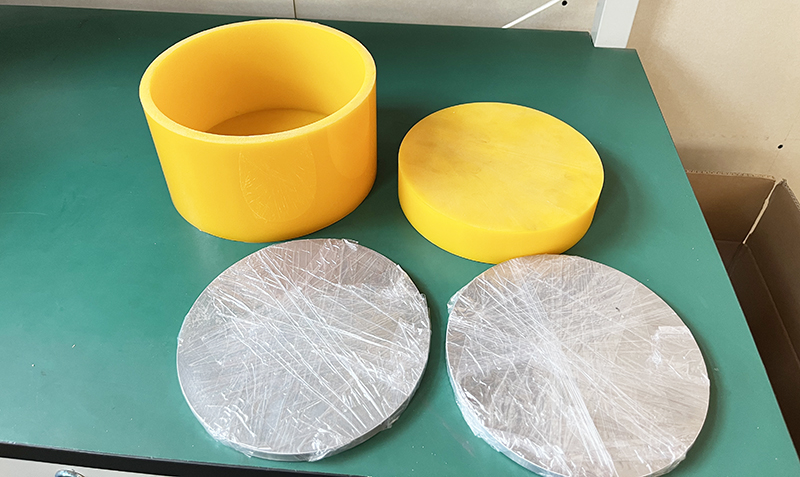
We support all kinds of customization, if you need it, please contact us.
Phone/whatsapp:+86 18234744811
Email:sales@highindustryco.com