The isostatic pressing process is the alternative compaction of the metal powders inside special molds to obtain more uniform densities and more complex geometries with a better flow of the metal.
Isostatic pressing is applied with flexible lateral molds, which are shaped with the application of lateral hydraulic pressures. With the application of pressurized fluid from the lateral sections of a rubber mold. Rubber mold will take the required shape with the pressure and the same pressure will compact the metal powder.
Types Of The Isostatic Pressing Processes
There are two types of isostatic pressing processes; cold isostatic pressing(CIP) and hot isostatic pressing(HIP).
CIP
Advantages And Disadvantages Of The Cold Isostatic Pressing
The most important advantage of the cold isostatic pressing is the cheap tooling. And because of this, cold isostatic pressing processes are more suitable for low production.
The Uniform density of the obtained product is another important aspect of the cold isostatic pressing process.
Dimensional accuracy is the biggest problem for the cold isostatic pressing processes. Because of the flexible molds, tolerances are problematic issues. So, additional machining or other processes must be applied to parts that are produced with the cold isostatic pressing.
HIP
Advantages And Disadvantages Of The Hot Isostatic Pressing Processes
The most important advantage of the hot isostatic pressing process is the both compacting and sintering operations are done in one step, because of the application of pressure.
But the main disadvantage of the hot isostatic pressing process is the expensive tooling. Because of this, these processes are applied only to special applications such as aerospace applications.
The produced parts with the hot isostatic pressing process are generally good in mechanical strength because of the low porosity.
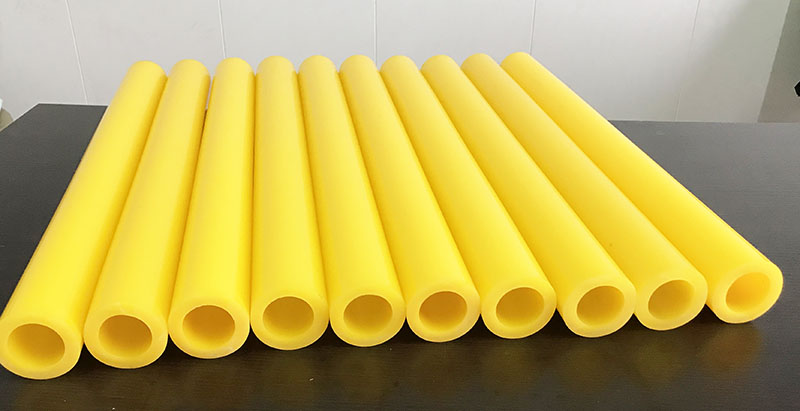
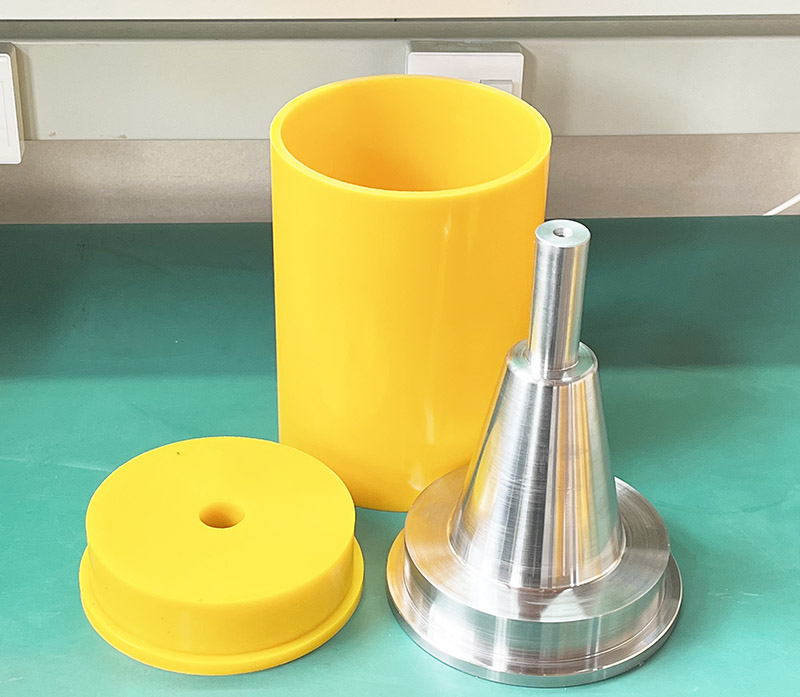

We support all kinds of customization, if you need it, please contact us.
Phone/whatsapp:+86 18234744811
Email:sales@highindustryco.com