Cold Isostatic Pressing of Ceramic
Cold isostatic pressing (CIP) is a manufacturing process for the consolidation of metal and ceramic powders. For metals, around 100% theoretical density can be achieved, while ceramic powders that are more difficult to compress can reach about 95% of theoretical density. The CIP uses a liquid media, such as water or an oil or glycol-mixed water, to apply pressure to the powder. The powder is contained in a mold that does not change shape, but preserves the shape from the mold. The mold also protects against liquid penetrating into the powder.
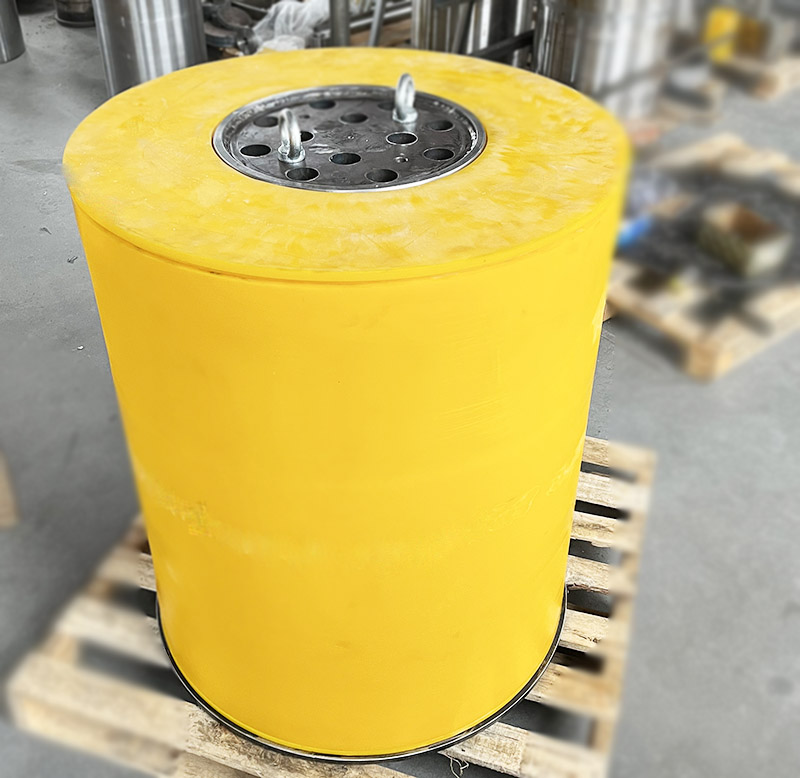
The very high pressure enables the voids in the powder to be smaller or eliminated, through high compaction forces that will make metal powder deform due to its ductility and ceramic powders to likely crumble somewhat so that density increases and the end-product is a “green” part that can be handled, machined and sintered. Typical pressures range from 100-600 MPa, and the temperature is usually at room temperature. If an application requires elevated temperatures, a heat exchanger can bring up the temperature to about 93°C. The risk of boiling increases at higher temperatures due to the temperature increase when water is compressed, about 4°C per 100 MPa.
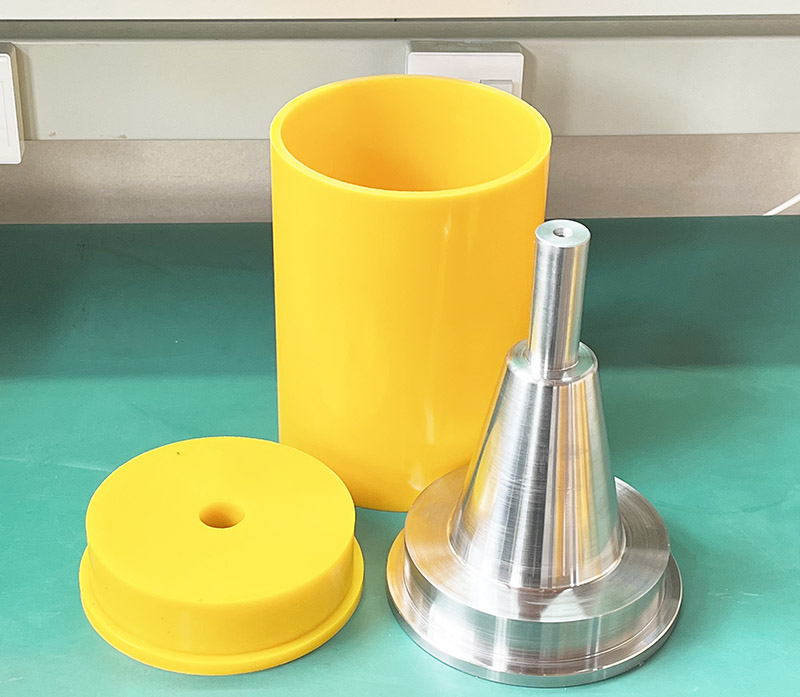
Common applications for CIP include the consolidation of ceramic powders, compression of graphite, refractories and electrical insulators, and other fine or advanced ceramics for dental and medical applications. Material systems include silicon nitrides, silicon carbides, boron nitride, boron carbide, titanium boride, spinels, etc. The technology is expanding into new applications such as the pressing of sputtering targets, coatings of valve parts in an engine to minimize wear of the cylinder heads, telecommunications, electronics, aerospace and automotive. The three main advantages associated with the CIPing of ceramics include:
60-95% of Theoretical Density
·Consolidation of ceramic powders
·“Green parts” for ceramics are ready for next process steps
·Elaborate designs of ceramics by CIM (ceramic injection molding)
Improved Material Properties
·Increased mechanical properties (e.g., powder compacts of alumina and electrical insulators)
·Reduced scatter of data for safest control of production
·Highest properties for minimal corrosion deterioration
Safer and More Efficient Production
·Fastest method for consolidation of ceramic powders to high density
·Lowest cost/kg
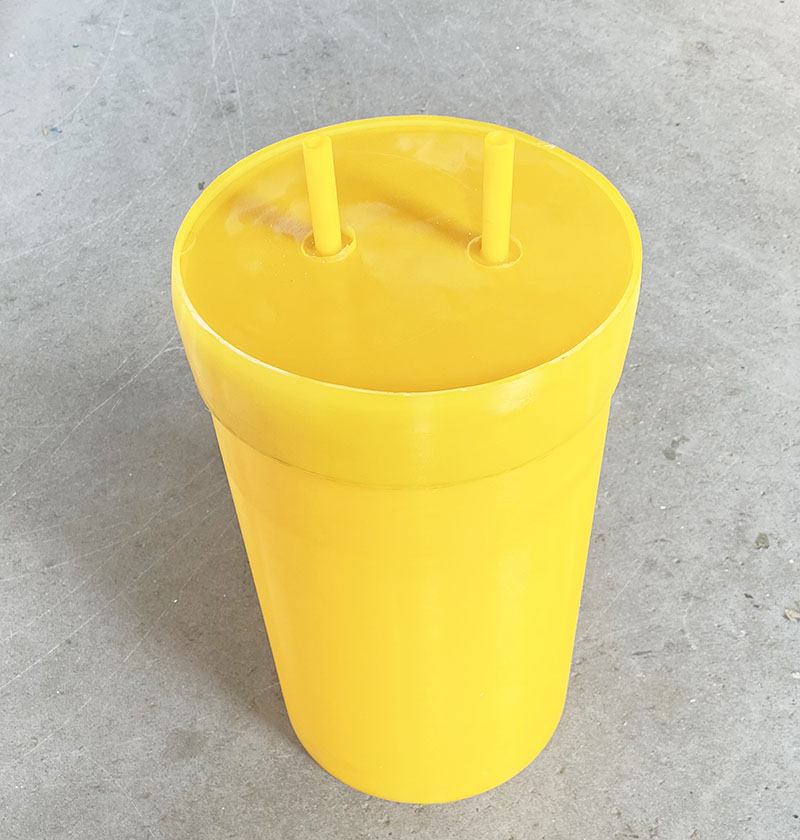
We support all kinds of customization, if you need it, please contact us.
Phone/whatsapp:+86 18234744811
Email:sales@highindustryco.com