Isostatic Pressing and Isostatic Graphite
Isostatic pressing is the name used by Jackson (1967) when a powder is compacted by applying pressure simultaneously and equally in all directions in a tightly sealed flexible mould. The origin of the isostatic pressing technique appears to be an apparatus described by Madden (1912). The pressure can be transmitted by liquids, gases, rubbers, plastics and glasses with oil or water being used most frequently.
Van Buren & Hirsch (1960) showed that a given powder, processed under the same conditions, will possess better mechanical properties when isostatically pressed as opposed to die-pressed. They found the greatest improvement in properties in the ductility of the sintered part. They observed greater uniformity of density of parts prepared by isotatic pressing which resulted in a more uniform shrinkage during sintering. They also showed that hard powders could be isostatically pressed with reasonable ease but these same powders were difficult if not impossible to press by die-pressing.
Isostatic pressing is the powder compaction method involving applying pressure from multiple directions through a liquid or gaseous medium surrounding the compacted part.
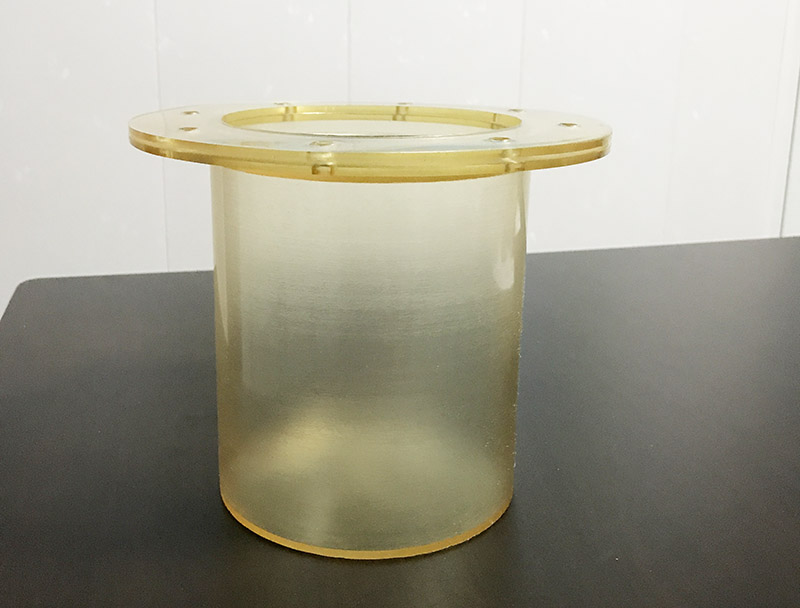
Properties of isostatic graphite
high strength
excellent resistance to thermal shock
high temperature and oxidation resistance
low electrical resistance
good corrosion resistance
precise machining
low content of impurities
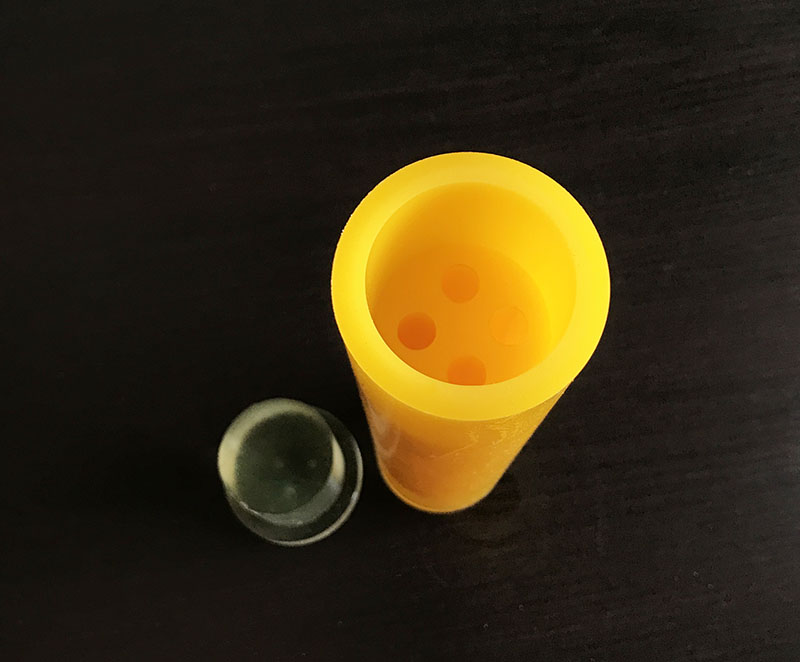