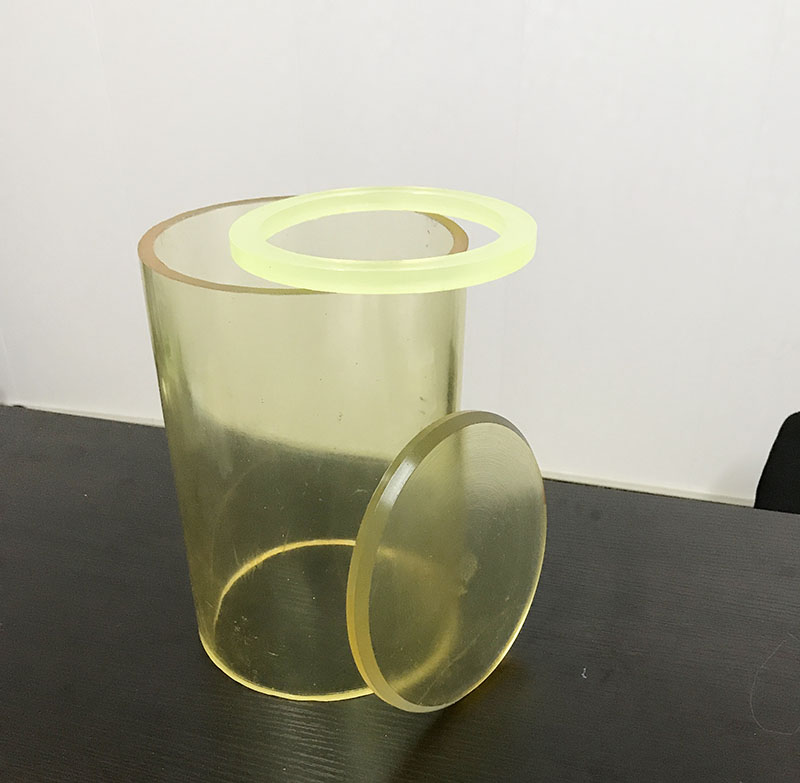
Production Process of Isostatic Pressing Products
Categories: Industry news
Application: Production Process of Isostatic Pressing Products
InquiryMain description:
Production Process of Isostatic Pressing Products
Production Process of Isostatic Pressing Products
Production process of isostatic pressing products:
① Mold making: forming large-scale special refractory products on an isostatic press requires a special rubber (latex) mold. When designing rubber molds, the scaling rate should be considered. Generally, the scaling rate is 30% to 40%. The main factors affecting the scaling rate are the compression ratio caused by the molding pressure; the firing shrinkage of various raw materials and the margin of cold processing of the product.
② Granulated powder: The raw material of granulated powder requires an average particle size of less than 2um and a maximum particle size of less than 10um. Due to the large specific surface area and extremely poor fluidity of this raw material, the filling performance is not good. In order to improve the filling performance of the raw material, the raw material should be sprayed and granulated. Add admixtures to various powders, put them in a high-speed mixer and stir evenly, and then send them into the machine. The granulated material is in the shape of a small sphere, has excellent fluidity, a large filling coefficient, and the particle size of the granulated material is less than 0.3mm.
③ Loading: In order to increase the loading density of large-shaped products, it is necessary to load on the vibrating table, that is, put the rubber sleeve with one end closed in a metal basket with many small holes that can be hoisted, and put them together on the vibrating table. Feed and vibrate from the upper port to achieve the maximum packing density of the granulated material in the rubber sleeve. After the material is filled, the top sealing cover is put on the cover T. If necessary, carry out air extraction treatment at the reserved hole on the top to improve the pressing effect of the green body.
④ Pressurized molding: hoist the metal basket together with the rubber mold filled with the material into the cleaning barrel, and use cleaning oil (same as the medium in the high-pressure container) to clean the powder and material attached to the outer surface of the rubber mold in the basket and the rubber mold. other inclusions. After cleaning, put it in the high-pressure container of the isostatic press for pressurized molding.
Polyurethane Isostatic Pressing Molds
We support all kinds of customization, if you need it, please contact us.
Phone/whatsapp:+86 18234744811
Email:sales@highindustryco.com