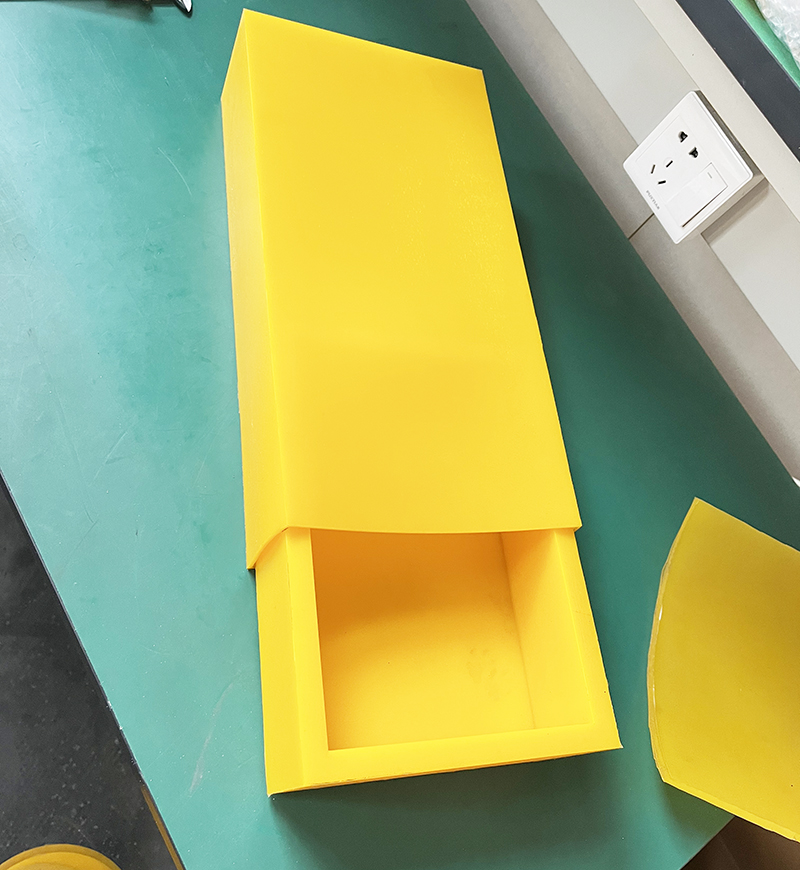
Isostatic Pressing Molds for Powder Metallurgy
Categories: Industry news
Application: Isostatic Pressing Molds for Powder Metallurgy
InquiryMain description:
Isostatic Pressing Molds for Powder Metallurgy
Isostatic Pressing Molds for Powder Metallurgy
Isostatic Pressing Molds for Powder Metallurgy
Powder Metallurgy Isostatic Pressing
One of the basic processes in powder metallurgy production, the purpose is to make loose powder into semi-finished or finished products with predetermined geometry, size, density and strength. Compression molding (steel mold) forming is the most widely used forming method in powder metallurgy production. In the second half of the 18th century and the first half of the 19th century, Spain, Russia and the United Kingdom used similar powder metallurgy processes to manufacture platinum products. At that time, Russia Sobolevsky (П.Г.Соболевсκий) used a steel mold and a screw press. W.H.Wollaston (W.H.Wollaston) in the United Kingdom used a higher-pressure tie-rod press and higher-purity platinum powder to produce dense platinum with almost no residual pores. Later, the molding method was gradually improved and used to manufacture various shapes of copper-based oil-impregnated bearings and other products. Since the 1930s, in the industrial production process of powder metallurgy parts, press equipment, mold design and other aspects have been continuously improved, the molding method has been greatly developed, and mechanization and automation have reached a higher level. In order to expand the size and shape range of products, especially to increase the density of products, thermoforming methods such as isostatic pressing, hot extrusion and hot forging have appeared since the 1950s. These methods facilitate the production of fully dense, high-performance powder metal materials.
The method of achieving densification by transmitting pressure through liquid or gas to uniformly press the powder in all directions is called isostatic pressing, or isostatic pressing for short (see isostatic pressing processing).
Cold Isostatic Pressing
Usually, the powder is sealed in a soft bag, and then placed in a liquid medium in a high-pressure container, and the powder is uniformly pressed in all directions by applying pressure to the liquid, so as to obtain the required compact. The liquid medium can be oil, water or glycerin. The sheath material is an elastic-plastic material such as rubber. Metal powder can be directly loaded or molded to fit the sleeve. Because the powder is uniformly pressed in all directions in the sheath, a compact with a relatively uniform density can be obtained, so it is not easy to deform and crack during sintering. The disadvantage is that the dimensional accuracy of the compact is poor, and machining is required. Cold isostatic pressing has been widely used in the forming of cemented carbide, refractory metals and various other powder materials.
Samples of the Isostatic Pressing Molds We Made
We support all kinds of customization, if you need it, please contact us.
Phone/whatsapp:+86 18234744811
Email:sales@highindustryco.com