Isostatic pressing of ceramics
The isostatic pressing method, also known as hydrostatic pressing, is a molding method that utilizes the incompressibility of liquid media and the uniform transmission of pressure. That is to say, the pressure on the sample in the high-pressure container is the same as that in the still water at the same depth, so it is called hydrostatic pressure or static pressure, and the forming process obtained according to this principle is called hydrostatic pressure. molding or isostatic pressing. Generally, the isostatic pressing of ceramic materials can be divided into wet bag isostatic pressing and dry bag isostatic pressing.
Wet bag isostatic pressing is to put the powder into the forming mold (i.e., the bag) first, and then place it in a high-pressure cylinder for pressing after sealing. During pressing, the sheath is completely immersed in the liquid and is in direct contact with the pressure transmission medium. Wet bag isostatic pressing has strong applicability, especially suitable for experimental research and small batch production, and can simultaneously press two or more different shapes of parts in one high-pressure cylinder and produce large and complex shaped parts. The production process Short and cheap.
Isostatic pressing of dry bag method is to put the powder into the forming rubber mold and put them into the pressurized rubber mold together, or send the powder through the feeding hopper from above to the pressurized rubber mold to form the rubber mold. It is not in contact with the liquid medium, so it is called the dry bag method. This method can realize continuous operation, open the upper cover, charge from the hopper, then cover the upper cover, and pressurize and form. When the blank is released, the upper cover is opened, and the blank is ejected from the top through the top rod at the bottom. The dry bag method has a high degree of automation and a short operation cycle, and is suitable for mass production. However, because the pressurized rubber mold is not easy to be replaced frequently, the size and shape of the formed product are limited.
Compared with the dry pressing method, the biggest feature of the isostatic pressing method is that the powder material is in a state of three-dimensional compressive stress, so the performance and quality of the formed parts are significantly improved.
The advantages of isostatic pressing are specifically shown in the following points:
1. Dry pressing has only one or two pressure surfaces, while isostatic pressing is multi-axial pressure, that is, multi-directional pressure and multi-surface pressure, which is conducive to compacting the powder to a considerable density. At the same time, the linear displacement of the powder particles is small, and the friction work consumed in the movement of the powder particles is relatively small, which improves the pressing efficiency.
2. Compared with other compression moldings with approximately the same pressure strength, isostatic pressing can obtain higher green density, and it is uniform and dense in all directions, and does not have a large change due to different shape thickness.
3. Due to the little difference in the pressure direction of isostatic pressing, the friction between the powder particles and between the particles and the model is significantly reduced, so the phenomenon of stress in the green body rarely occurs.
4. The green body formed by isostatic pressing has high strength, the internal structure of the green body is uniform, and there is no particle orientation arrangement.
5. The water content of the powder used in isostatic pressing is very low (generally 1%-3%), and it is unnecessary or seldom to use binders and lubricants. This is beneficial for reducing drying shrinkage and firing shrinkage.
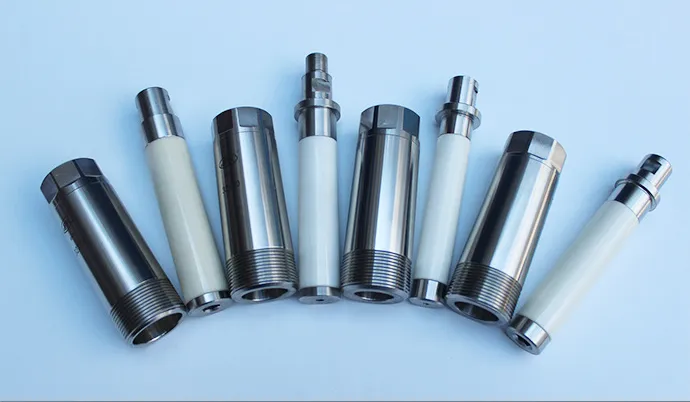
Jiangsu High Industry on the research and development and production of high-performance polyurethane isostatic pressing molds. Through in-depth cooperation with many isostatic pressing equipment manufacturers and in-depth study of the industry, the developed isostatic pressing polyurethane mold series products have the characteristics of long service life, high precision, small deformation, easy demoulding, etc., and are widely used in ceramics, etc. Static pressing mould, cemented carbide isostatic pressing mould, rare earth permanent magnet material isostatic pressing mould, graphite isostatic pressing mould, etc.
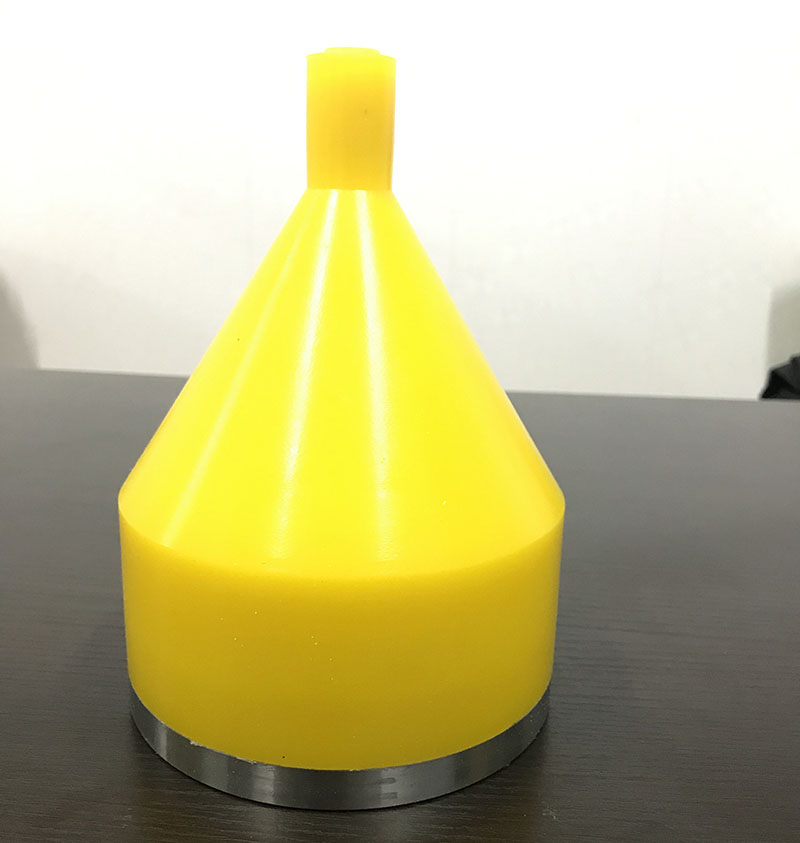
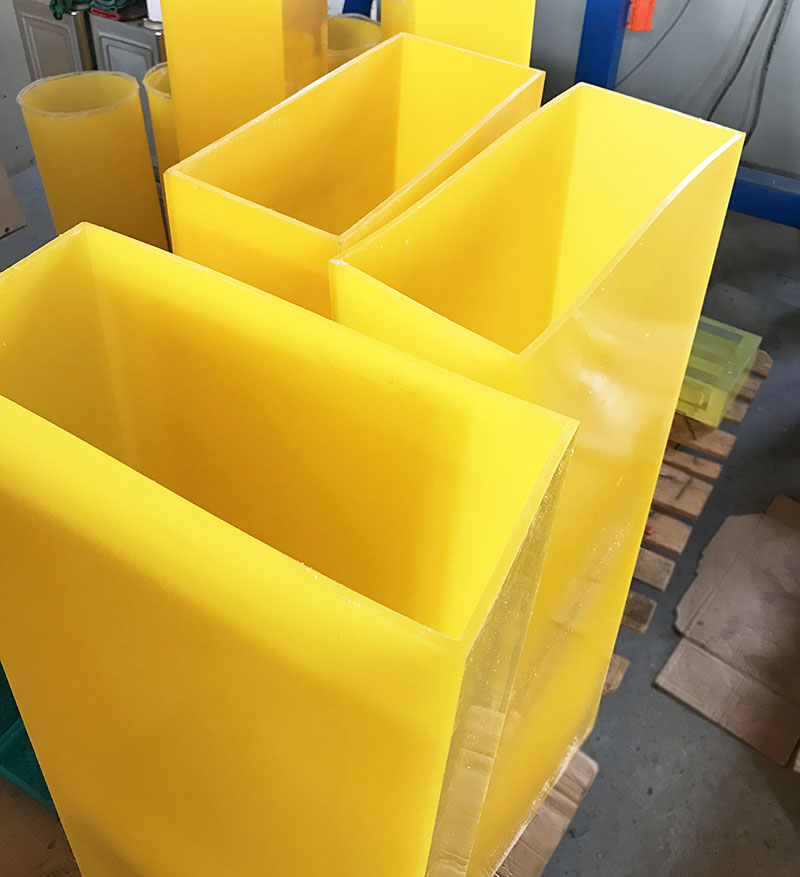
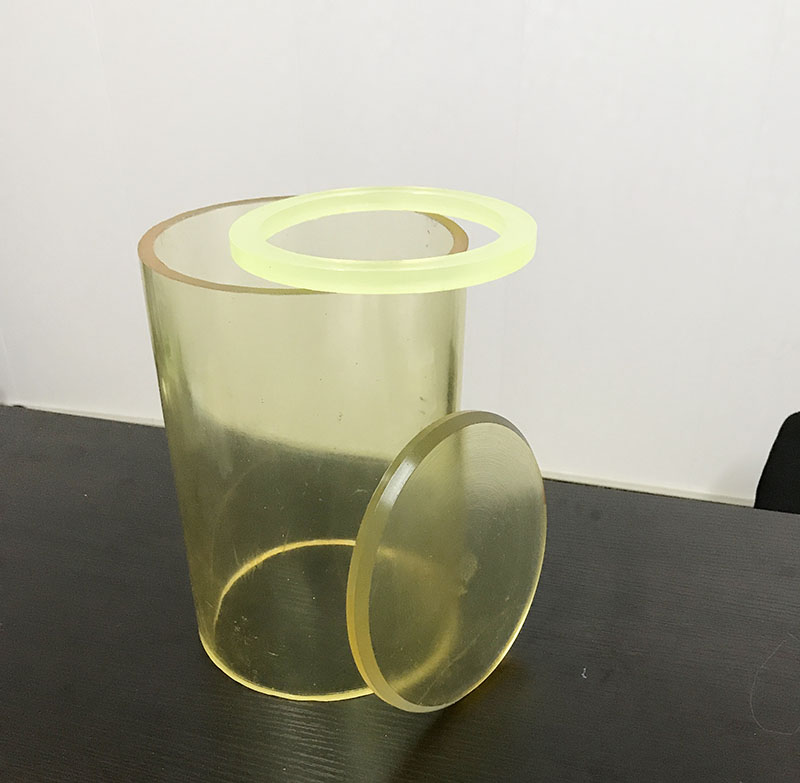
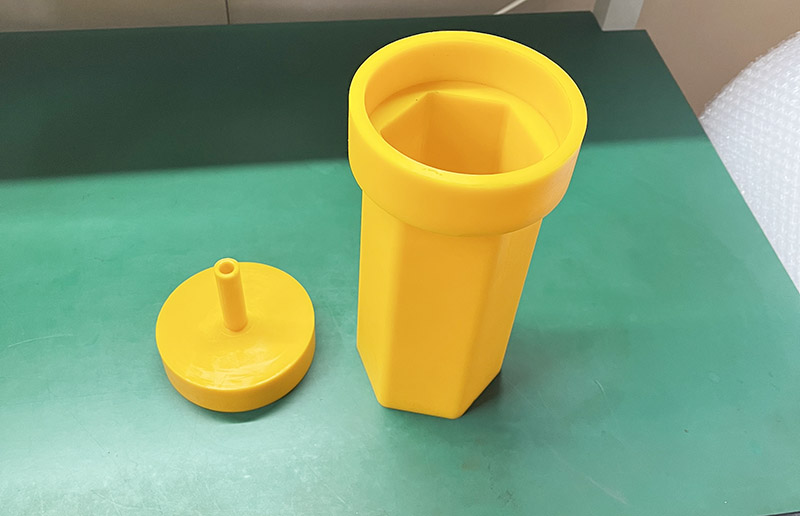
We support all kinds of customization, if you need it, please contact us.
Phone/whatsapp:+86 18234744811
Email:sales@highindustryco.com
Polyurethane Products Pu Products Rubber Mold Plastic Mold