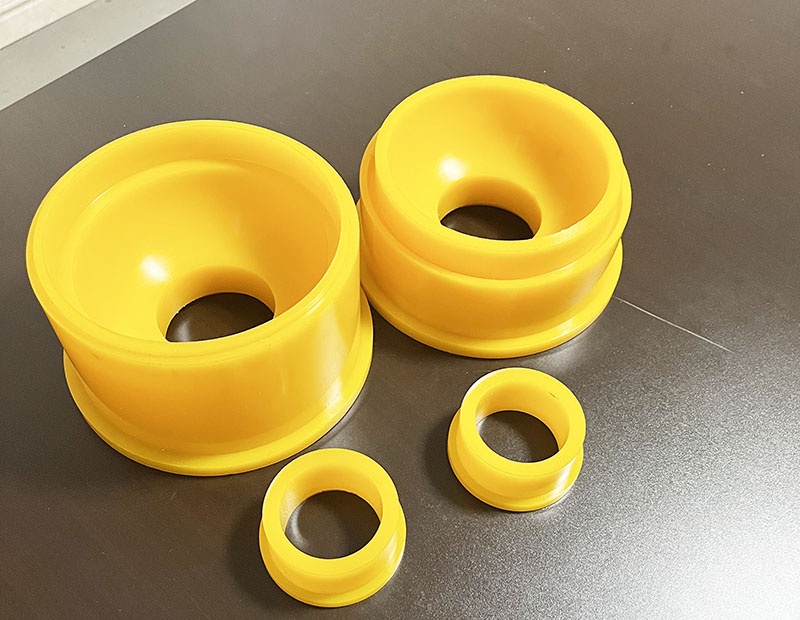
Isostatic Pressing Technology
Isostatic pressing is a new forming method developed in recent decades. It has been used in actual production since the 1930s. After the 1950s, due to the higher and higher requirements for molding quality and the development of high-voltage equipment and high-voltage component technology, isostatic pressing technology has developed rapidly. It is widely used in ceramics, powder metallurgy, plastics and other industries. In the ceramic industry, clay ceramics, electric porcelain, electronic ceramics, refractory ceramics, and special ceramics are all formed by isostatic pressing. The introduction of the isostatic pressing method in the molding of Jun porcelain works of art is to solve the production problems of fine Jun porcelain handicrafts, and it is only used in individual Jun porcelain research laboratories.
Isostatic pressing is similar to dry pressing, which uses pressure to press dry powder into a mold. However, the pressure of isostatic pressing is not limited to one or two pressure-bearing surfaces like dry pressing, but applies uniform pressure on all surfaces of the model. Obviously, this molding method is superior to the dry pressing molding method, which can eliminate some difficult weaknesses in the dry pressing molding method and improve the molding quality of the product. Therefore, it can be said that isostatic pressing is also a kind of dry pressing, which is a new development of general dry pressing.
Isostatic pressing utilizes the property that liquid or gas can transmit pressure uniformly in all directions to achieve uniform compression molding. The molding process can be described as follows: put the powder into an elastic mold, seal it, and then put the mold together with the powder in a high-pressure container filled with liquid or gas. After sealing, use a pump to pressurize the liquid or gas, and through the characteristics of the liquid or gas that can transmit the pressure evenly, the elastic mold will receive uniform pressure and transmit it to the powder, so that the powder is pressed into a compacted object similar to the model. But the size is smaller than the model. After the pressure is completed, the pressure is slowly reduced, and the green body can be taken out of the mold.
Isostatic pressing can be divided into two types according to the different molds used: one is wet bag isostatic pressing, and the other is dry bag isostatic pressing. Its advantages are: higher green density can be obtained. Since the directional difference of isostatic pressure is not as large as that of other compression molding, the phenomenon of stress in the green body rarely occurs during isostatic pressing. Therefore, the green body has high strength, uniform internal structure, and does not cause regular arrangement of particles like extrusion molding. In addition, the isostatic pressing method can realize high-temperature isostatic pressing, combining molding and firing into one process.
Jiangsu High Industry on the research and development and production of high-performance polyurethane isostatic pressing molds. Through in-depth cooperation with many isostatic pressing equipment manufacturers and in-depth study of the industry, the developed isostatic pressing polyurethane mold series products have the characteristics of long service life, high precision, small deformation, easy demoulding, etc., and are widely used in ceramics, etc. Static pressing mould, cemented carbide isostatic pressing mould, rare earth permanent magnet material isostatic pressing mould, graphite isostatic pressing mould, etc.
We support all kinds of customization, if you need it, please contact us.
Phone/whatsapp:+86 18234744811
Email:sales@highindustryco.com