Isostatic Pressing Ceramic Technology
Cold isostatic pressing is a very important ceramic forming technology. It is a method of compressing powder by transferring isotropic pressure through a fluid medium at room temperature. Compared with conventional molding technology, isostatic pressing has higher molding blank density, and its blank density is 5% to 15% higher than that of ordinary molding; and the blank density is uniform, so it is suitable for cylindrical, cylindrical and other long diameters. In addition, isostatic pressing products have excellent performance, so isostatic pressing technology has important applications in the preparation of special ceramics and other fields, and has been successfully applied to some large and complex ceramic products such as ceramic radomes, vacuum arc extinguishing In the production of chamber ceramic tube shell, thermocouple protection ceramic sleeve, alumina or zirconia ceramic tube for oil drilling, transparent ceramic tube for high pressure sodium lamp, high pressure ceramic insulating tube, spark plug and carbon graphite products, etc.
Isostatic pressing is divided into two processes: dry and wet. The wet process powder is put into a plastic bag, placed in a liquid medium, and in direct contact with the liquid. Since the shape and size of the plastic wrap can be arbitrarily changed according to the shape of the product, products of different shapes can be produced, and the dry method is mainly suitable for small-scale production of a single product, so the wet method is more widely used than dry isostatic pressing. In the isostatic pressing process, the properties of the powder, the filling density of the powder in the mold, and the structure of the mold have a great influence on the performance of the formed blank, and the structural design of the isostatic pressing mold is very important. In the specific implementation of the isostatic pressing process, it is further divided into direct isostatic pressing and molding-isostatic pressing combined forming process, while the direct isostatic pressing process is further divided into internal pressure method and external pressure method according to the different pressing directions. pressure method. The design of the forming mold and the cover corresponding to these different methods also have their own characteristics.

Isostatic Pressing Bags, Cold Isostatic Pressing bags, CIP bags
Compare to traditional rubber cold isostatic pressing bags, the polyurethane CIP bags have significant advantages. As a new polymer material, polyurethane products feature smooth surface, wearing-resistant, anti-fatigue, low deformation rate. The surface of pressed products with polyurethane bags is much smoother than that pressed with rubber bags, thus it possesses better looks and less postprocessing is required. It’s an ideal tool for powder material forming by press process, which can help a company reduce cost and increase efficiency.
Durability and deformation rate are factors that users care most. A long working life of pressing bag can reduce cost and increase production efficiency, while low deformation rate of the bag will enhance precision and yield of products. By close cooperation with material suppliers and great mass of manufacturers of carbide, ceramics and graphite products, we accumulated a lot of experience in this industry and become a well-know supplier of CIP bags.
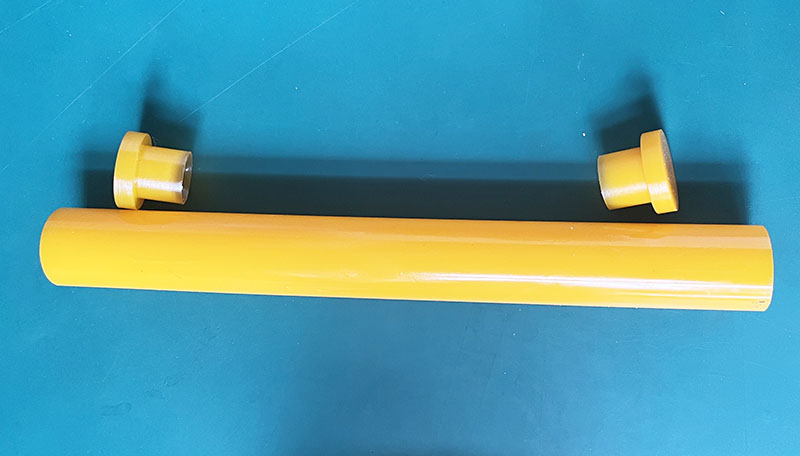
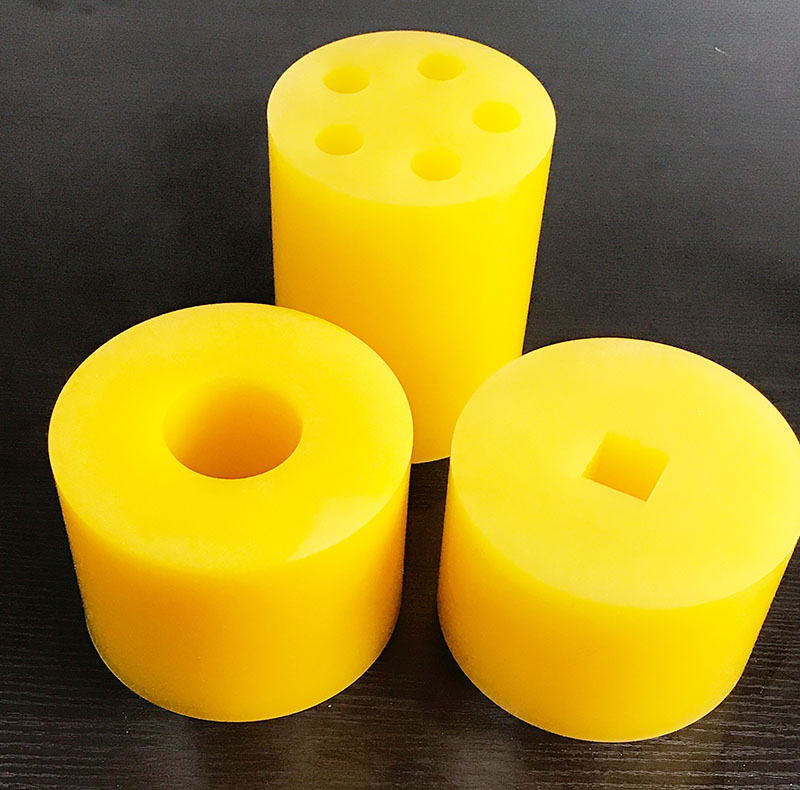
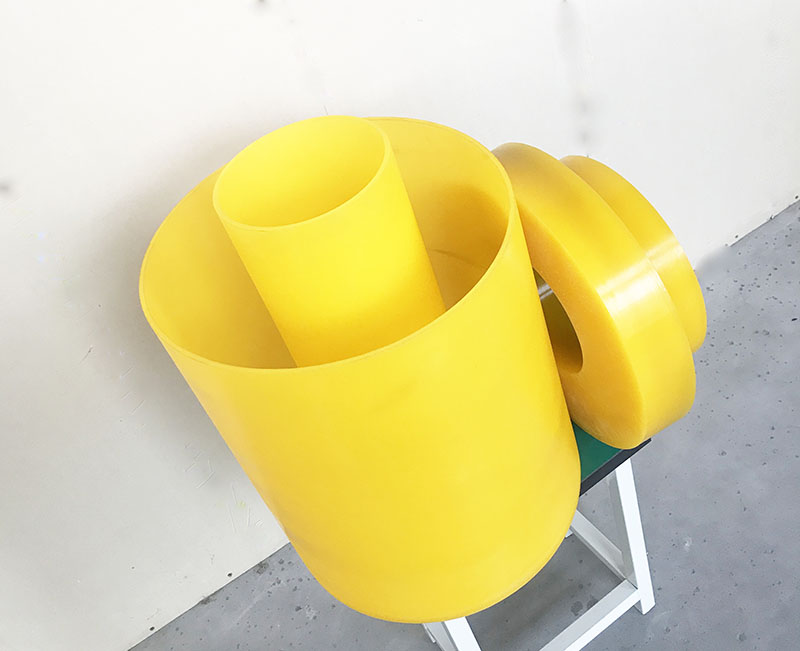
We support all kinds of customization, if you need it, please contact us.
Phone/whatsapp:+86 18234744811
Email:sales@highindustryco.com