Alumina ceramics
Alumina ceramics is a very wear-resistant precision ceramic material, which is widely used in all walks of life. The main molding methods of alumina ceramic products are: dry pressing, isostatic pressing, injection molding and casting. Different product shapes, sizes, complex shapes and precision products require different molding methods. High temperature sintered alumina ceramic products can only be machined using a diamond grinding process. Alumina ceramic material has extremely high hardness and wear resistance, strong corrosion resistance, high temperature resistance, corrosion resistance and biological inertness. In addition, alumina sintered at high temperature can be highly polished and is widely used in many fields.
Alumina ceramic tubes are mainly formed by isostatic pressing. This molding method has good strength and is convenient for handling and direct machining. In addition, the isotropic density of the green body is uniform, the stress in the green body is small, the defects such as cracking and delamination of the green body are reduced, and the deformation of the sintered product is small.
Based on the performance characteristics of alumina ceramics, alumina ceramic tubes are also widely used. Common ones are material conveying pipes, insulating sleeves, processing molds, etc.




Isostatic Pressing bags, Cold Isostatic Pressing, CIP bags, ISO bags
Compare to traditional rubber cold isostatic pressing bags, the polyurethane CIP bags have significant advantages. As a new polymer material, polyurethane products feature smooth surface, wearing-resistant, anti-fatigue, low deformation rate. The surface of pressed products with polyurethane bags is much smoother than that pressed with rubber bags, thus it possesses better looks and less postprocessing is required. It’s an ideal tool for powder material forming by press process, which can help a company reduce cost and increase efficiency.
Durability and deformation rate are factors that users care most. A long working life of pressing bag can reduce cost and increase production efficiency, while low deformation rate of the bag will enhance precision and yield of products. By close cooperation with material suppliers and great mass of manufacturers of carbide, ceramics and graphite products, we accumulated a lot of experience in this industry and become a well-know supplier of CIP bags.
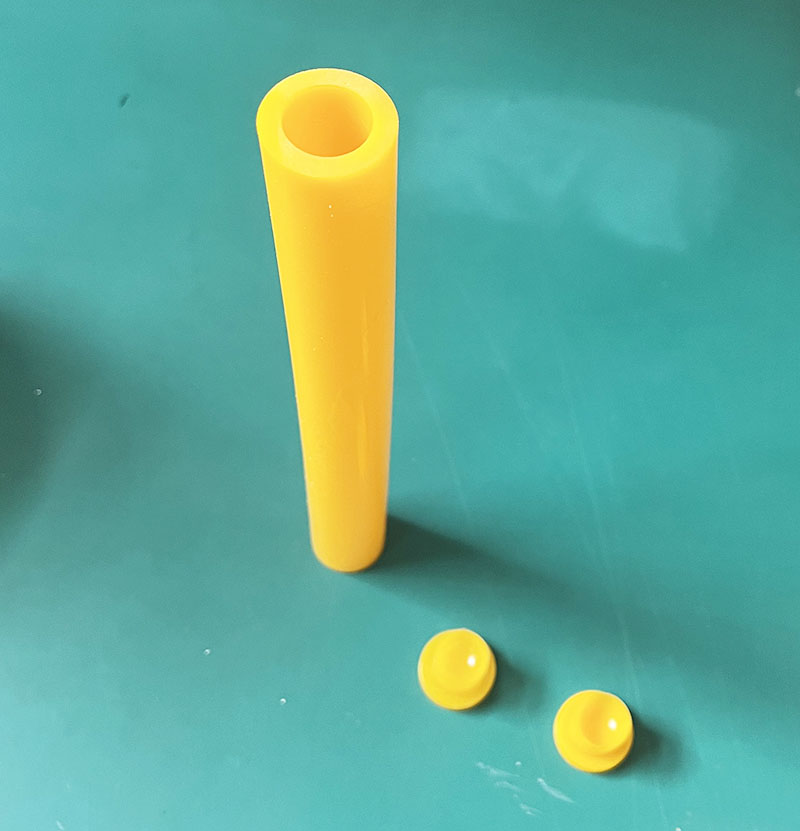
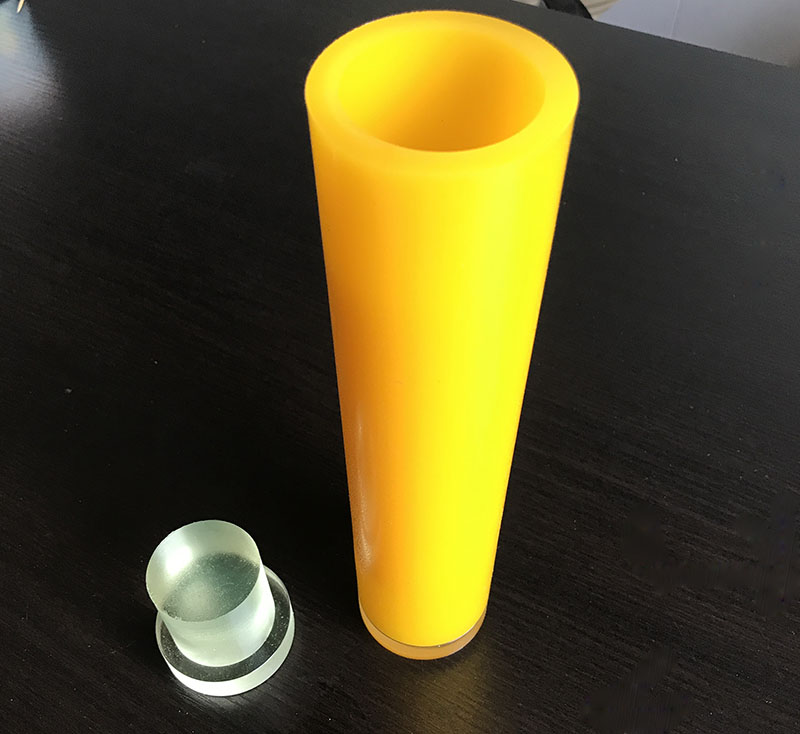
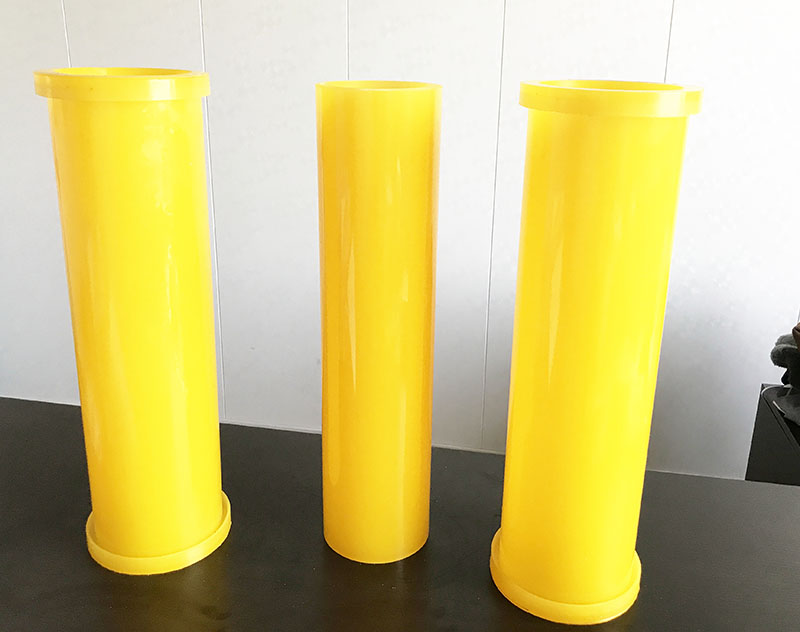